2025 Autor: Howard Calhoun | [email protected]. Última modificación: 2025-06-01 07:13
Hoy en día casi no hay área de la vida humana donde no se use hierro fundido. Este material es conocido por la humanidad desde hace mucho tiempo y ha demostrado ser excelente desde un punto de vista práctico. El hierro fundido es la base de una gran variedad de piezas, conjuntos y mecanismos, y en algunos casos incluso un producto autosuficiente capaz de realizar las funciones que se le asignan. Por lo tanto, en este artículo prestaremos mucha atención a este compuesto que contiene hierro. También descubriremos qué tipos de hierro fundido son, sus características físicas y químicas.
Definición
El hierro fundido es una aleación verdaderamente única de hierro y carbono, en la que Fe es más del 90 % y C no es más del 6,67 %, pero no menos del 2,14 %. Además, el carbono se puede encontrar en el hierro fundido en forma de cementita o grafito.
El carbono le da a la aleación una dureza suficientemente alta, sin embargo, al mismo tiempo, reduce la maleabilidad y la ductilidad. Como resultado, el hierro fundido es un material quebradizo. Además, se agregan aditivos especiales a ciertos grados de hierro fundido, que pueden darle al compuesto ciertas propiedades. El papel de los elementos de aleación puede ser: níquel, cromo, vanadio, aluminio. El índice de densidad del hierro fundido es de 7200 kilogramos por metro cúbico. De lo cual se puede concluir queel peso del hierro fundido es un indicador que no puede llamarse pequeño.

Antecedentes históricos
La fundición de hierro es conocida desde hace mucho tiempo por el hombre. La primera mención de la aleación data del siglo VI a. C.
En la antigüedad, China producía hierro fundido con un punto de fusión bastante bajo. El hierro fundido comenzó a producirse en Europa alrededor del siglo XIV, cuando se utilizaron por primera vez los altos hornos. En ese momento, dicha fundición de hierro se utilizaba para la producción de armas, proyectiles y piezas de construcción.
En Rusia, la producción de hierro fundido comenzó activamente en el siglo XVI y luego se expandió rápidamente. Durante la época de Pedro I, el Imperio ruso pudo pasar por alto a todos los países del mundo en términos de producción de hierro, pero cien años después comenzó a perder terreno nuevamente en el mercado de la metalurgia ferrosa.
El hierro fundido se ha utilizado para crear una variedad de obras de arte desde la Edad Media. En particular, en el siglo X, los maestros chinos lanzaron una figura verdaderamente única de un león, cuyo peso excedía las 100 toneladas. A partir del siglo XV en Alemania, y después en otros países, la fundición de hierro fundido se generalizó. De él se hicieron cercas, celosías, esculturas de parques, muebles de jardín, lápidas.
En los últimos años del siglo XVIII, la fundición de hierro estuvo más involucrada en la arquitectura de Rusia. Y el siglo XIX fue generalmente llamado la "edad del hierro fundido", ya que la aleación se utilizó muy activamente en la arquitectura.

Características
Hay diferentes tiposhierro fundido, sin embargo, el punto de fusión promedio de este compuesto metálico es de aproximadamente 1200 grados centígrados. Esta cifra es de 250 a 300 grados menos que la requerida para la fabricación de acero. Esta diferencia está asociada con un contenido de carbono bastante alto, lo que conduce a sus enlaces menos estrechos con los átomos de hierro a nivel molecular.
En el momento de la fundición y posterior cristalización, el carbono contenido en el hierro fundido no tiene tiempo de penetrar completamente en la red molecular del hierro y, por lo tanto, el hierro fundido finalmente resulta ser bastante frágil. En este sentido, no se usa donde hay cargas dinámicas constantes. Pero al mismo tiempo, es excelente para aquellas piezas que tienen mayores requisitos de resistencia.
Tecnología de producción
Absolutamente todos los tipos de hierro fundido se producen en un alto horno. En realidad, el proceso de fundición en sí es una actividad bastante laboriosa que requiere importantes inversiones materiales. Una tonelada de arrabio requiere unos 550 kilogramos de coque y casi una tonelada de agua. El volumen de mineral cargado en el horno dependerá del contenido de hierro. La mayoría de las veces, se usa mineral, en el que el hierro es al menos el 70%. Una concentración más baja del elemento no es deseable, ya que no sería económico usarlo.
Producción primera etapa
La fundición de hierro es la siguiente. En primer lugar, se vierte el mineral en el horno, así como los grados de carbón coquizable, que sirven para presurizar y mantener la temperatura requerida dentro del pozo del horno. Además, estos productos durante el proceso de combustión participan activamente en las reacciones químicas en curso enpapel de los agentes reductores de hierro.
Al mismo tiempo, se carga un fundente en el horno, que sirve como catalizador. Ayuda a que las rocas se derritan más rápido, lo que favorece la liberación de hierro.
Es importante señalar que el mineral se somete a un pretratamiento especial antes de ser cargado en el horno. Se tritura en una planta trituradora (las partículas pequeñas se derriten más rápido). Luego se lava para eliminar las partículas libres de metales. Después de eso, la materia prima se cuece, debido a esto, se eliminan el azufre y otros elementos extraños.

Segunda etapa de producción
El gas natural se suministra al horno cargado y listo para funcionar a través de quemadores especiales. El coque calienta la materia prima. En este caso, se libera carbono, que se combina con el oxígeno y forma un óxido. Este óxido participa posteriormente en la recuperación del hierro del mineral. Tenga en cuenta que con un aumento en la cantidad de gas en el horno, la velocidad de la reacción química disminuye, y cuando se alcanza una determinada proporción, se detiene por completo.
El exceso de carbono penetra en la masa fundida y se une al hierro, formando eventualmente hierro fundido. Todos aquellos elementos que no se han derretido quedan en la superficie y eventualmente se eliminan. Este desecho se llama escoria. También se puede utilizar para producir otros materiales. Los tipos de hierro fundido obtenidos de esta manera se denominan fundición y arrabio.
Diferenciación
La clasificación moderna de las fundiciones prevé la división de estas aleaciones en los siguientes tipos:
- Blanco.
- La mitad.
- Gris con escamas de grafito.
- Grafito nodular de alta resistencia.
- Dúctil.
Veamos cada uno por separado.

Hierro fundido blanco
Esta fundición es aquella en la que casi todo el carbono está unido químicamente. En ingeniería mecánica, esta aleación no se usa con mucha frecuencia porque es dura, pero muy quebradiza. Además, no se puede mecanizar con varias herramientas de corte y, por lo tanto, se utiliza para piezas de fundición que no requieren ningún procesamiento. Aunque este tipo de hierro fundido permite rectificar con muelas abrasivas. El hierro fundido blanco puede ser tanto ordinario como aleado. Al mismo tiempo, soldarlo causa dificultades, ya que va acompañada de la formación de varias grietas durante el enfriamiento o calentamiento, y también debido a la heterogeneidad de la estructura que se forma en el punto de soldadura.
Las fundiciones blancas resistentes al desgaste se obtienen por cristalización primaria de una aleación líquida durante un enfriamiento rápido. Se utilizan más comúnmente para aplicaciones de fricción seca (por ejemplo, pastillas de freno) o para la producción de piezas con mayor resistencia al desgaste y al calor (rodillos de laminación).
Por cierto, el hierro fundido blanco obtuvo su nombre debido al hecho de que la apariencia de su fractura es una superficie radiante de cristal claro. La estructura de esta fundición es una combinación de ledeburita, perlita y cementita secundaria. Si este hierro fundido se alea, entonces la perlita se transforma entroostita, austenita o martensita.

Medio hierro fundido
La clasificación de las fundiciones estaría incompleta sin mencionar esta variedad de aleación metálica.
Esta fundición se caracteriza por una combinación de eutécticos de carburo y grafito en su estructura. En general, la estructura completa tiene la siguiente forma: grafito, perlita, ledeburita. Si el hierro fundido se somete a tratamiento térmico o aleación, se formará austenita, martensita o troostita acicular.
Este tipo de fundición es bastante frágil, por lo que su uso es muy limitado. La aleación en sí recibió su nombre porque su fractura es una combinación de áreas claras y oscuras de la estructura cristalina.
El material de ingeniería más común
El hierro fundido gris GOST 1412-85 contiene aproximadamente un 3,5 % de carbono, entre un 1,9 y un 2,5 % de silicio, hasta un 0,8 % de manganeso, hasta un 0,3 % de fósforo y menos de un 0,12 % de azufre.
El grafito en tal hierro fundido tiene una forma laminar. No requiere modificación especial.
Las placas de grafito tienen un fuerte efecto debilitante y, por lo tanto, el hierro fundido gris se caracteriza por una resistencia al impacto muy baja y una ausencia casi total de alargamiento (menos del 0,5%).
La fundición gris está bien mecanizada. La estructura de la aleación puede ser la siguiente:
- Ferrita-grafito.
- Ferrita-perlita-grafito.
- Perlita-grafito.
La fundición gris funciona mucho mejor en compresión que en tensión. Él tambiénse suelda bastante bien, pero esto requiere precalentamiento, y se deben usar varillas especiales de hierro fundido con un alto contenido de silicio y carbono como material de relleno. Sin precalentamiento, la soldadura será difícil porque el hierro fundido se blanqueará en el área de soldadura.
El hierro fundido gris se utiliza para producir piezas que funcionan sin cargas de choque (poleas, cubiertas, bancadas).
La designación de esta fundición se produce según el siguiente principio: SCH 25-52. Dos letras indican que se trata de fundición gris, el número 25 es un indicador de la resistencia a la tracción (en MPa o kgf/mm 2), el número 52 es la resistencia a la tracción en el momento de flexión.

Hierro dúctil
La fundición nodular se diferencia fundamentalmente de sus otros "hermanos" en que contiene grafito nodular. Se obtiene introduciendo modificadores especiales (Mg, Ce) en la aleación líquida. El número de inclusiones de grafito y sus dimensiones lineales pueden ser diferentes.
¿Qué tiene de bueno el grafito esferoidal? El hecho de que tal forma debilita mínimamente la base del metal, que, a su vez, puede ser perlítico, ferrítico o perlítico-ferrítico.
Debido al uso de tratamiento térmico o aleación, la base de hierro fundido puede ser acicular-troostita, martensítica, austenítica.
Los grados de hierro dúctil son diferentes, pero en términos generales, su designación es la siguiente: VCh 40-5. Es fácil adivinar que HF es hierro fundido de alta resistencia, el número 40 es un indicadorresistencia a la tracción (kgf/mm2), el número 5 es relativo al alargamiento, expresado como porcentaje.
Hierro dúctil
La estructura del hierro dúctil es la presencia de grafito en forma escamosa o esférica. Al mismo tiempo, el grafito escamoso puede tener diferente finura y compacidad, lo que, a su vez, tiene un impacto directo en las propiedades mecánicas del hierro fundido.
El hierro dúctil industrial a menudo se produce con una base ferrítica, lo que proporciona una mayor ductilidad.
La apariencia de fractura del hierro dúctil ferrítico tiene un aspecto aterciopelado negro. Cuanto mayor sea la cantidad de perlita en la estructura, más ligera será la fractura.
En general, el hierro dúctil se obtiene a partir de fundiciones de hierro blanco debido a un largo languidecer en hornos calentados a una temperatura de 800 a 950 grados centígrados.
Hoy en día, hay dos formas de hacer hierro dúctil: europeo y americano.
El método americano consiste en languidecer la aleación en arena a una temperatura de 800-850 grados. En este proceso, el grafito se ubica entre granos del hierro más puro. Como resultado, el hierro fundido se vuelve viscoso.
En el método europeo, las fundiciones languidecen en el mineral de hierro. La temperatura al mismo tiempo es de aproximadamente 850-950 grados centígrados. El carbono pasa al mineral de hierro, por lo que la capa superficial de las piezas fundidas se descarbura y se vuelve blanda. El hierro fundido se vuelve maleable, mientras que el núcleo permanece quebradizo.
Marcado de hierro maleable: KCh 40-6, donde KCh es, por supuesto, hierro maleable; 40 - índice de resistencia a la tracción;6 - alargamiento, %.

Otros indicadores
En cuanto a la división de las fundiciones por resistencia, aquí se aplica la siguiente clasificación:
- Resistencia típica: σv hasta 20 kg/mm2.
- Resistencia aumentada: σv=20 - 38 kg/mm2.
- Alta resistencia: σv=40 kg/mm2 y superior.
Según la ductilidad, las fundiciones se dividen en:
- Inflexible - menos del 1% de elongación.
- Bajo plástico - del 1% al 5%.
- Plástico - del 5% al 10%.
- Aumento de la plasticidad: más del 10%.
En conclusión, también me gustaría señalar que las propiedades de cualquier hierro fundido se ven significativamente afectadas incluso por la forma y la naturaleza del vertido.
Recomendado:
Designación de elementos de aleación en acero: clasificación, propiedades, marcado, aplicación
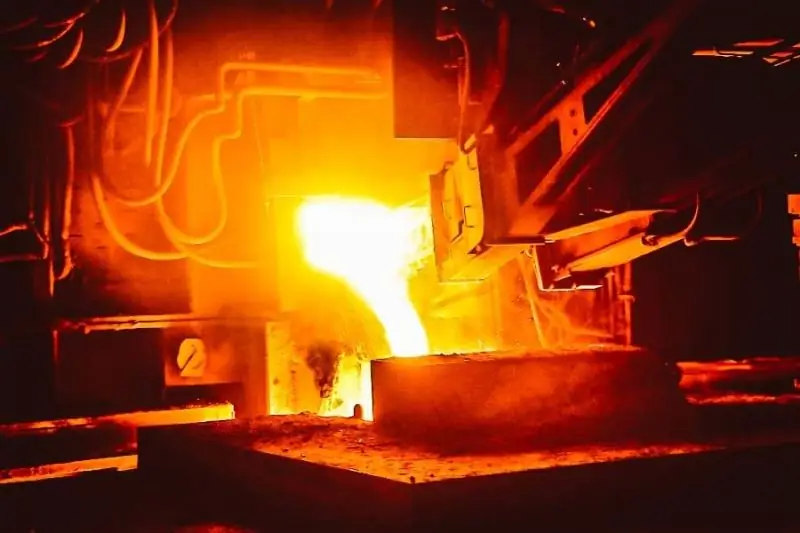
Hoy en día, una variedad de aceros se utilizan en muchas industrias. Mediante la aleación del metal se logra una variedad de propiedades físicas, mecánicas y de calidad. La designación de elementos de aleación en acero ayuda a determinar qué componentes se introdujeron en la composición, así como su contenido cuantitativo
Acero: composición, propiedades, tipos y aplicaciones. Composición del acero inoxidable
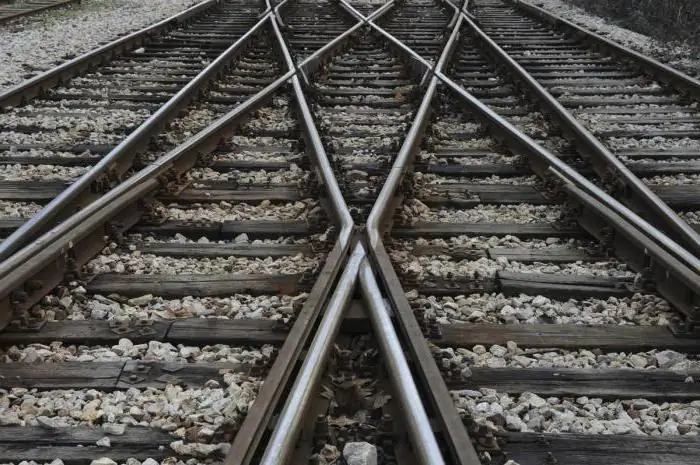
Hoy en día, el acero se utiliza en la gran mayoría de las industrias. Sin embargo, no todo el mundo sabe que la composición del acero, sus propiedades, tipos y aplicaciones son muy diferentes al proceso de producción de este producto
Fundición en molde de silicona: equipamiento. Fundición al vacío en moldes de silicona
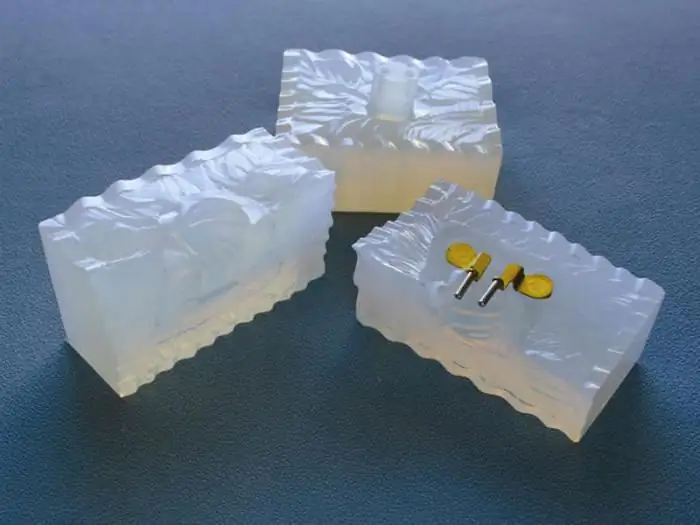
Para la fabricación de una pequeña cantidad de piezas de plástico, se suele utilizar la fundición al vacío en moldes de silicona. Este método es bastante económico (hacer un molde de metal requiere más tiempo y dinero). Además, los moldes de silicona se usan repetidamente y esto también reduce significativamente el costo de producción
Permeabilidad al vapor de espuma: composición, propiedades, estructura, clasificación, aplicación y seguridad

El grosor y la permeabilidad al vapor de la espuma: esto no es todo lo que necesita saber al comprar material. Es importante interesarse por el sonido y las propiedades a prueba de viento. Si las paredes están aisladas con espuma, no necesitarán protección contra el viento. Se mejorará la insonorización del edificio. Así, las propiedades insonorizantes se explican por la estructura celular
Mezcla de hormigón: propiedades, composición, tipos, grados de hormigón, características, cumplimiento de las normas GOST y aplicación
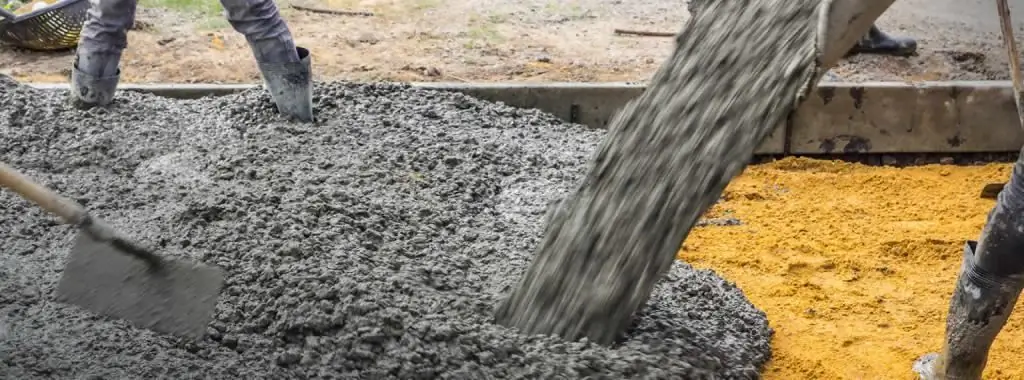
Entre las principales propiedades de la mezcla de hormigón, también llamado hormigón hidrotécnico, cabe destacar la mayor resistencia al agua. Se están construyendo edificios con este material para ser utilizados en áreas pantanosas o en regiones propensas a inundaciones