2025 Autor: Howard Calhoun | [email protected]. Última modificación: 2025-01-24 13:15
La eficiencia y los problemas de la superficie de plasma son extremadamente graves para los ingenieros de materiales. Gracias a esta tecnología, es posible no solo aumentar significativamente la vida útil y la confiabilidad de las piezas y ensamblajes altamente cargados, sino también restaurar, al parecer, productos cien por ciento desgastados y destruidos.
La introducción de la superficie de plasma en el proceso tecnológico aumenta significativamente la competitividad de los productos de ingeniería. El proceso no es fundamentalmente nuevo y se ha utilizado durante mucho tiempo. Pero está constantemente mejorando y ampliando sus capacidades tecnológicas.
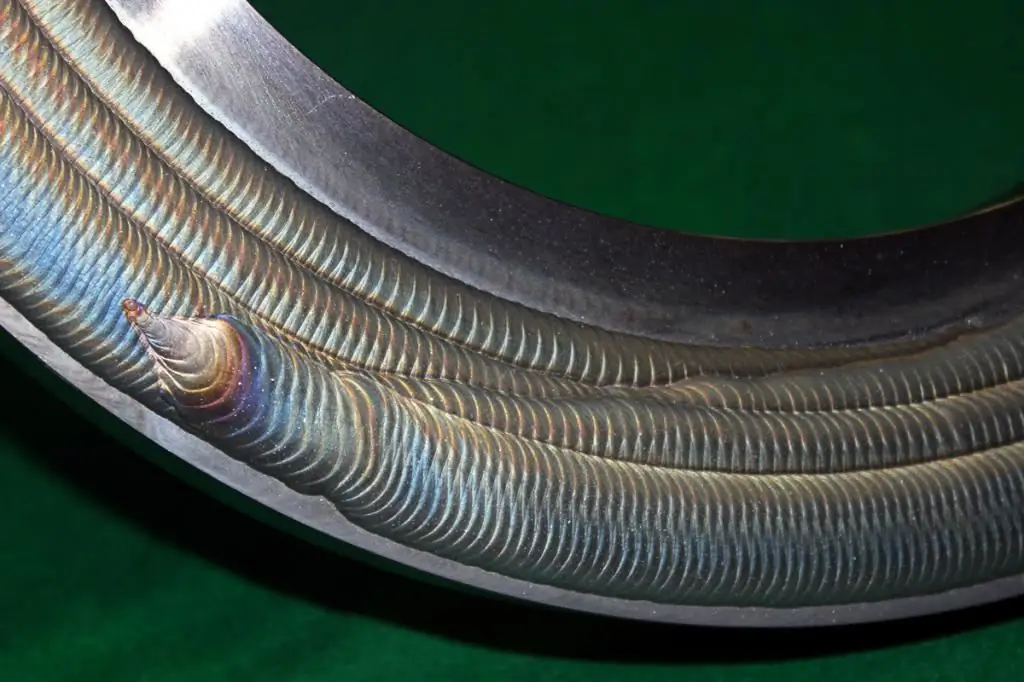
Disposiciones generales
El plasma es un gas ionizado. Se sabe con certeza que el plasma se puede obtener por varios métodos como resultado de efectos eléctricos, térmicos o mecánicos sobre las moléculas de gas. Para su formación, es necesario arrancar los electrones cargados negativamente de los átomos positivos.
En algunas fuentes puedes encontrarinformación de que el plasma es el cuarto estado de agregación de la materia junto con sólido, líquido y gaseoso. El gas ionizado tiene una serie de propiedades útiles y se utiliza en muchas ramas de la ciencia y la tecnología: revestimiento de plasma de metales y aleaciones para restaurar y endurecer productos muy cargados que experimentan cargas cíclicas, nitruración de plasma iónico en una descarga luminiscente para saturación por difusión y endurecimiento de superficies de piezas, para la aplicación de procesos químicos decapado (utilizado en tecnología de fabricación de productos electrónicos).
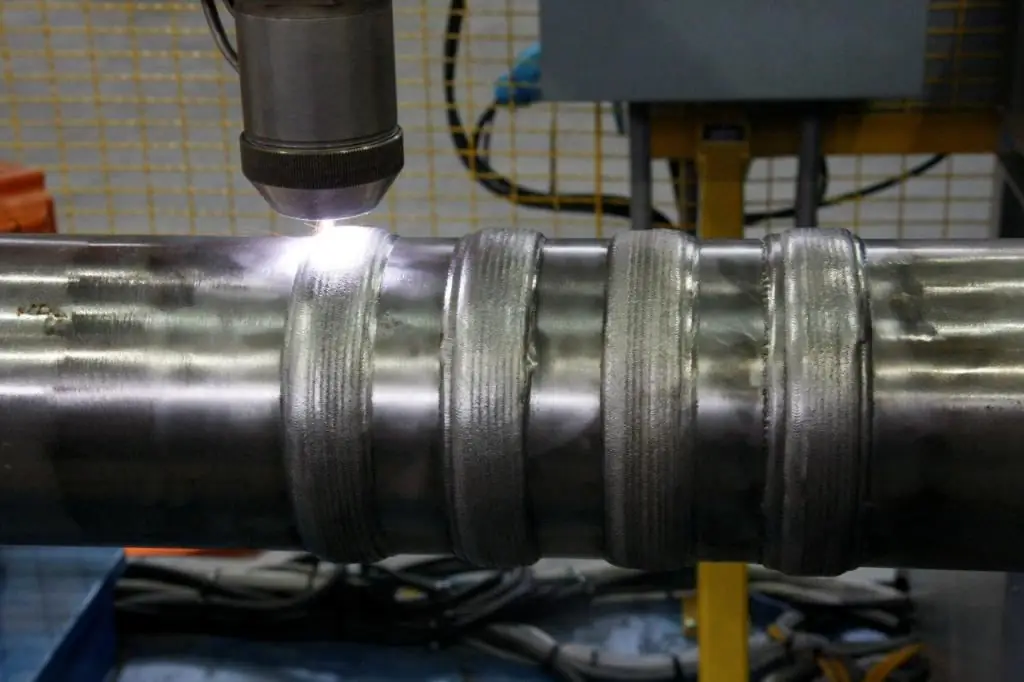
Preparación para el trabajo
Antes de comenzar a salir a la superficie, debe configurar el equipo. De acuerdo con los datos de referencia, es necesario seleccionar y configurar el ángulo correcto de inclinación de la boquilla del quemador a la superficie del producto, alinear la distancia desde el extremo del quemador a la parte (debe ser de 5 a 8 milímetros) e inserte el cable (si el material del cable está saliendo a la superficie).
Si la superficie se realizará mediante fluctuaciones de la boquilla en direcciones transversales, entonces es necesario ajustar el cabezal de tal manera que la soldadura esté exactamente en el medio entre los puntos extremos de las amplitudes de fluctuación de la cabeza. También es necesario ajustar el mecanismo que establece la frecuencia y magnitud de los movimientos oscilatorios del cabezal.
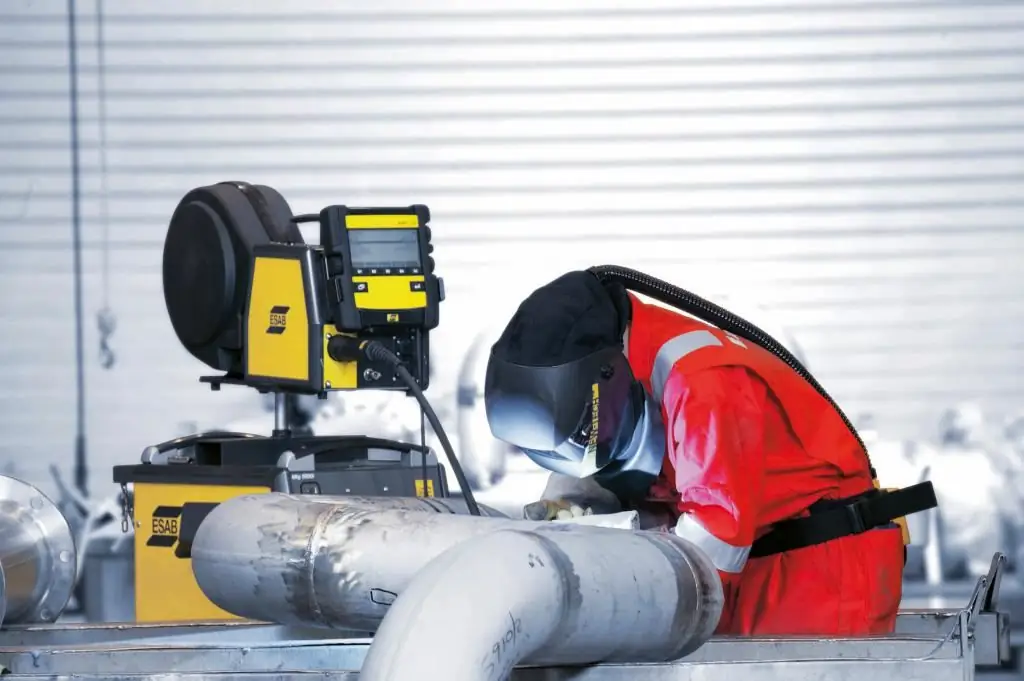
Tecnología de superficie de arco de plasma
El proceso de pulido es bastante simple y puede ser realizado con éxito por cualquier soldador experimentado. Sin embargo, él requiereintérprete de máxima concentración y atención. De lo contrario, puede estropear fácilmente la pieza de trabajo.
Se utiliza una potente descarga de arco para ionizar el gas de trabajo. El desprendimiento de electrones negativos de átomos cargados positivamente se lleva a cabo debido al efecto térmico del arco eléctrico sobre el chorro de la mezcla de gases de trabajo. Sin embargo, bajo una serie de condiciones, el flujo es posible no solo bajo la influencia de la ionización térmica, sino también debido a la influencia de un campo eléctrico potente.
El gas se suministra a una presión de 20-25 atmósferas. Para su ionización se requiere un voltaje de 120-160 voltios con una corriente de unos 500 amperios. Los iones cargados positivamente son capturados por el campo magnético y se precipitan hacia el cátodo. La velocidad y la energía cinética de las partículas elementales es tan grande que cuando chocan con el metal, pueden darle una temperatura enorme, de +10 … +18,000 grados Celsius. En este caso, los iones se mueven a una velocidad de hasta 15 kilómetros por segundo (!). La instalación de superficie de plasma está equipada con un dispositivo especial llamado "antorcha de plasma". Es este nodo el que se encarga de la ionización del gas y de obtener un flujo dirigido de partículas elementales.
La potencia del arco debe ser tal que evite la fusión del material base. Al mismo tiempo, la temperatura del producto debe ser lo más alta posible para activar los procesos de difusión. Por lo tanto, la temperatura debe acercarse a la línea liquidus en el diagrama de cemento de hierro.
El polvo fino de una composición especial o alambre de electrodo se introduce en un chorro de plasma de alta temperatura, en el que el materialse derrite En estado líquido, el revestimiento cae sobre la superficie endurecida.
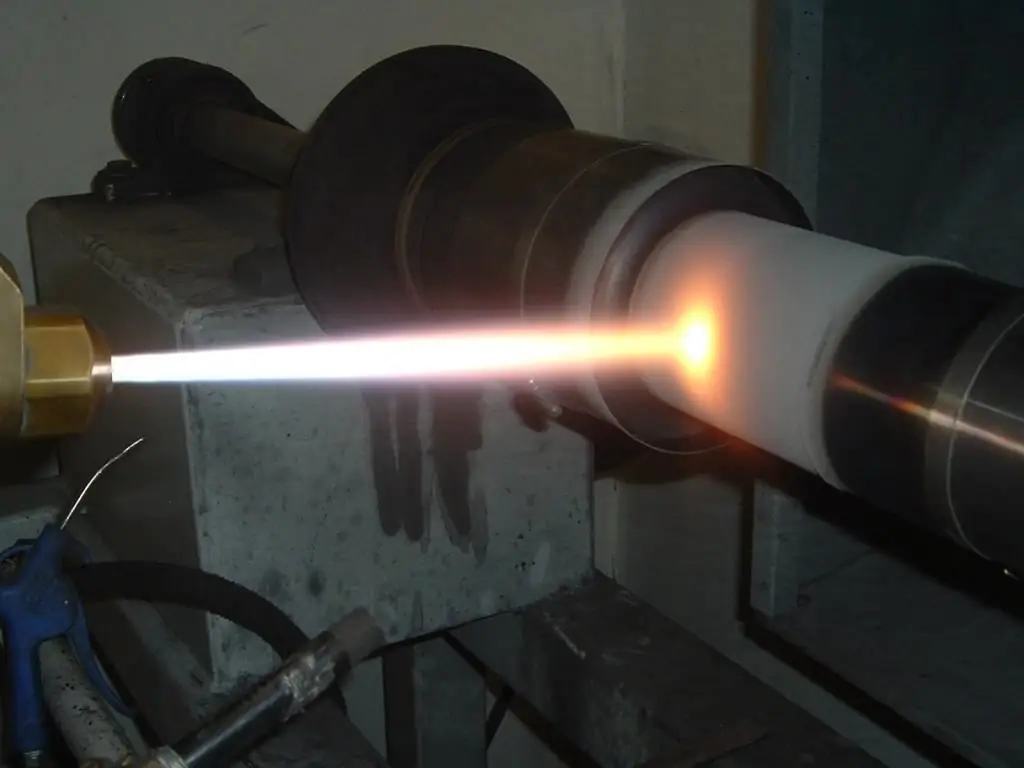
Rociado de plasma
Para implementar la pulverización de plasma, es necesario aumentar significativamente el caudal de plasma. Esto se puede lograr ajustando el voltaje y la corriente. Los parámetros se seleccionan empíricamente.
Los materiales para la pulverización de plasma son metales refractarios y compuestos químicos: tungsteno, tantalio, titanio, boruros, siliciuros, óxido de magnesio y óxido de aluminio.
La ventaja indiscutible de la pulverización frente a la soldadura es la posibilidad de obtener capas muy finas, del orden de varios micrómetros.
Esta tecnología se utiliza para endurecer, cortar, tornear y fresar insertos de carburo reemplazables, así como machos de roscar, brocas, avellanadores, escariadores y otras herramientas.
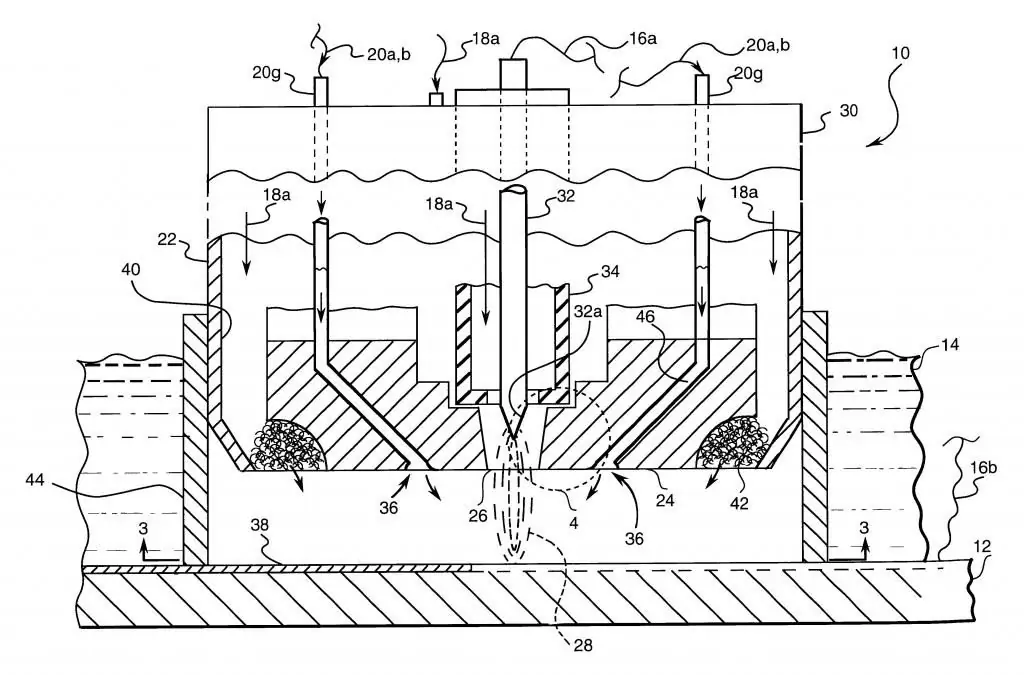
Obtención de un chorro de plasma abierto
En este caso, la propia pieza de trabajo actúa como un ánodo, sobre el cual se deposita el material por plasma. El inconveniente evidente de este método de procesamiento es el calentamiento de la superficie y de todo el volumen de la pieza, lo que puede provocar transformaciones estructurales y consecuencias indeseables: ablandamiento, aumento de la fragilidad, etc.
Chorro de plasma cerrado
En este caso, el quemador de gas, más precisamente su boquilla, actúa como ánodo. Este método se utiliza para el revestimiento de polvo de plasma con el fin de restaurar y mejorar el rendimiento de las piezas ynodos de máquina. Esta tecnología ha ganado particular popularidad en el campo de la ingeniería agrícola.
Ventajas del revestimiento duro de plasma
Una de las principales ventajas es la concentración de energía térmica en un área pequeña, lo que reduce el efecto de la temperatura en la estructura original del material.
El proceso es bien manejable. Si se desea, y con la configuración adecuada del equipo, la capa de superficie puede variar desde unas pocas décimas de milímetro hasta dos milímetros. La posibilidad de obtener una capa controlada es especialmente relevante en este momento, ya que permite aumentar significativamente la eficiencia económica del procesamiento y obtener propiedades óptimas (dureza, resistencia a la corrosión, resistencia al desgaste y muchas otras) de las superficies de los productos de acero.
Otra ventaja no menos importante es la capacidad de realizar soldaduras por plasma y recargues de una amplia variedad de materiales: cobre, latón, bronce, metales preciosos, así como no metales. Los métodos de soldadura tradicionales están lejos de ser siempre capaces de hacer esto.
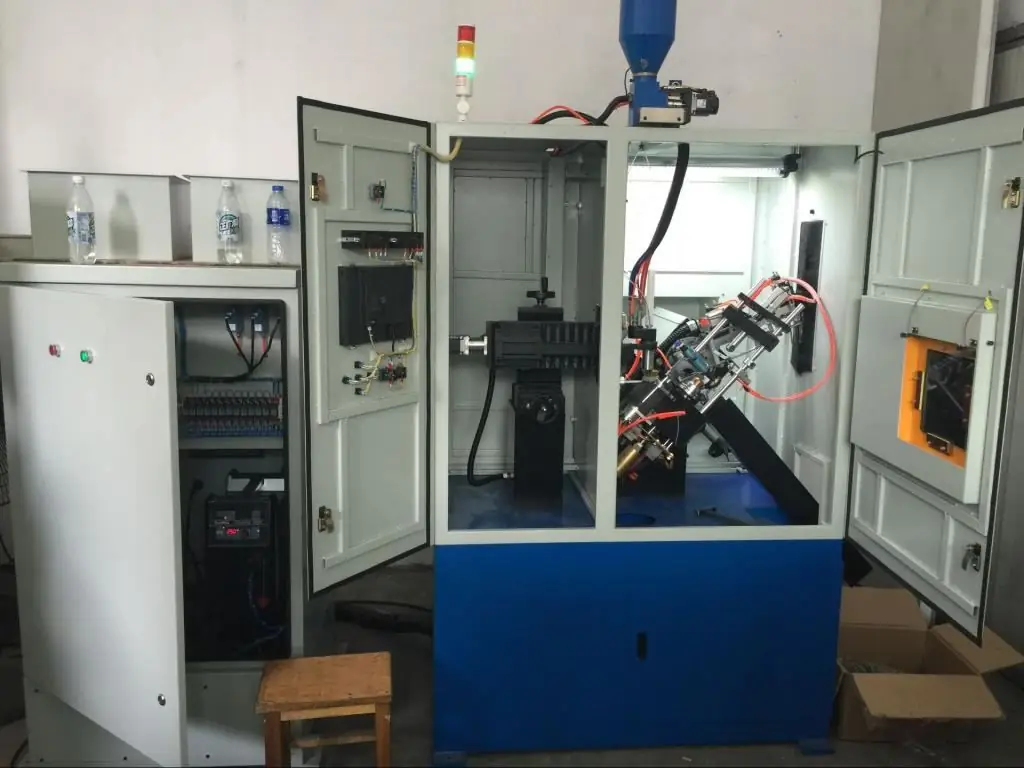
Equipo de revestimiento duro
La instalación para superficies de polvo de plasma incluye un estrangulador, un oscilador, una antorcha de plasma y fuentes de alimentación. Además, debe estar equipado con un dispositivo para alimentar automáticamente gránulos de polvo metálico en el área de trabajo y un sistema de enfriamiento con circulación constante de agua.
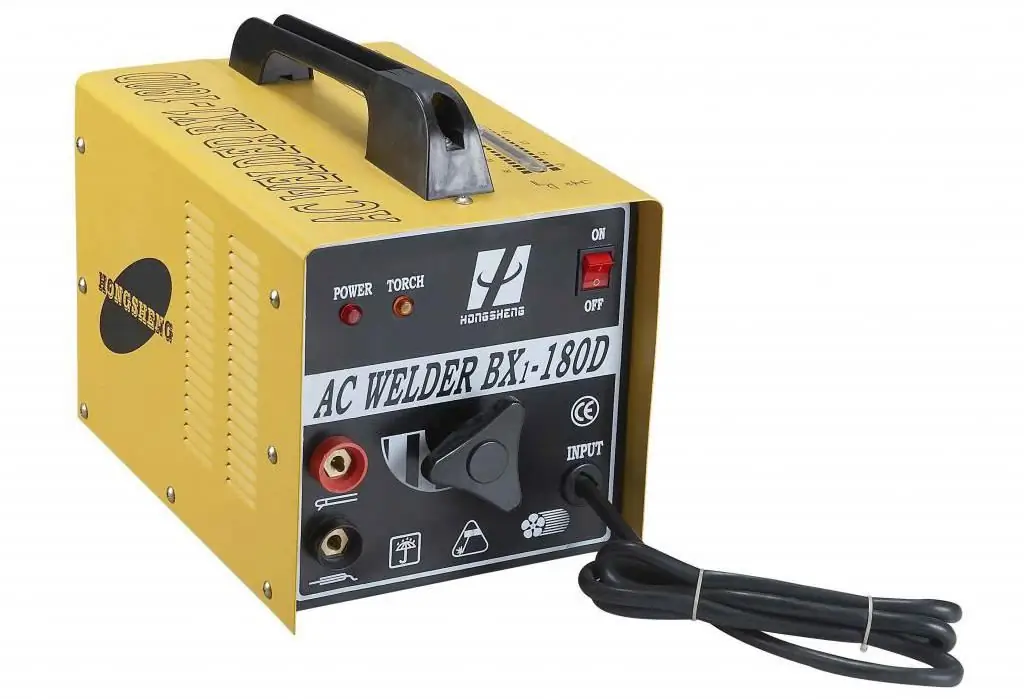
Las fuentes de energía para revestimiento duro de plasma deben cumplir requisitos estrictosconstancia y fiabilidad. Los transformadores de soldadura hacen el mejor trabajo con esta función.
Cuando se recubren materiales en polvo sobre una superficie metálica, se utiliza el llamado arco combinado. Ambos chorros de plasma abiertos y cerrados se utilizan simultáneamente. Al ajustar la potencia de estos arcos, es posible cambiar la profundidad de penetración de la pieza de trabajo. En condiciones óptimas, no aparecerán deformaciones de los productos. Esto es importante en la fabricación de piezas y conjuntos de ingeniería de precisión.
Alimentador de material
El polvo metálico se dosifica mediante un dispositivo especial y se introduce en la zona de fusión. El mecanismo o principio de funcionamiento del alimentador es el siguiente: las palas del rotor empujan el polvo hacia la corriente de gas, las partículas se calientan y se adhieren a la superficie tratada. El polvo se alimenta a través de una boquilla separada. En total, se instalan tres boquillas en el quemador de gas: para el suministro de plasma, para el suministro de polvo de trabajo y para el gas de protección.
Si utiliza alambre, se recomienda utilizar el mecanismo de alimentación estándar de una máquina de soldadura por arco sumergido.
Preparación de superficies
La superficie con plasma y la pulverización de materiales deben ir precedidos de una limpieza a fondo de la superficie para eliminar las manchas de grasa y otros contaminantes. Si durante la soldadura convencional solo se permite realizar una limpieza superficial de las juntas de óxido y escamas, entonces cuando se trabaja con plasma de gas, la superficie de la pieza de trabajo debe estar idealmente (en la medida de lo posible) limpia, sin inclusiones extrañas. La película de óxido más delgada es capaz dedebilitar significativamente la interacción adhesiva entre el revestimiento duro y el metal base.
Con el fin de preparar la superficie para el revestimiento, se recomienda eliminar una capa superficial insignificante de metal mecanizando mediante corte, seguido de desengrasado. Si las dimensiones de la pieza lo permiten, se recomienda lavar y limpiar las superficies en un baño de ultrasonidos.
Características importantes de las superficies metálicas
Hay varias opciones y métodos para la superficie de plasma. El uso de alambre como material para la superficie aumenta significativamente la productividad del proceso en comparación con los polvos. Esto se debe al hecho de que el electrodo (alambre) actúa como un ánodo, lo que contribuye a un calentamiento mucho más rápido del material depositado, lo que significa que le permite ajustar los modos de procesamiento hacia arriba.
Sin embargo, la calidad del recubrimiento y las propiedades de adhesión están claramente del lado de los aditivos en polvo. El uso de finas partículas metálicas permite obtener una capa uniforme de cualquier espesor sobre la superficie.
Polvo de superficie
El uso de superficies en polvo es preferible en términos de calidad de las superficies resultantes y resistencia al desgaste, por lo que las mezclas en polvo se utilizan cada vez más en la producción. La composición tradicional de la mezcla de polvo es partículas de cob alto y níquel. La aleación de estos metales tiene buenas propiedades mecánicas. Después del procesamiento con tal composición, la superficie de la pieza permanece perfectamente lisa y no es necesario su acabado mecánico y eliminación de irregularidades. La fracción de partículas de polvo es de unos pocos micrómetros.
Recomendado:
Procesos tecnológicos en ingeniería mecánica. Sistemas de control de procesos automatizados
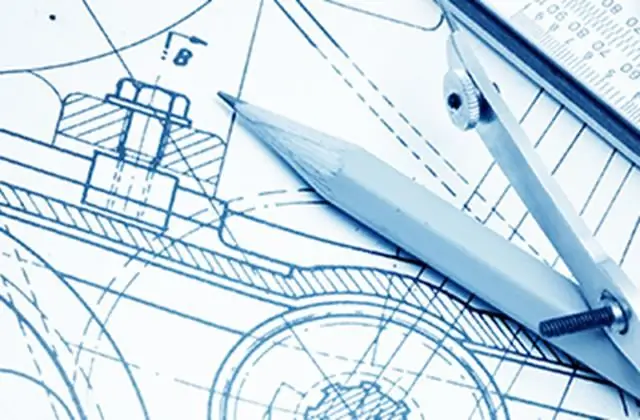
El proceso tecnológico es la base de cualquier operación productiva. Incluye un conjunto de procedimientos llevados a cabo en una secuencia determinada, cuya acción está dirigida a cambiar la forma, el tamaño y las propiedades del producto fabricado. Los principales ejemplos de procesos tecnológicos son el procesamiento mecánico, térmico, de compresión, así como el ensamblaje, el empaque, el tratamiento a presión y mucho más
Recubrimiento de acero con nitruro de titanio. Tecnología de polvo
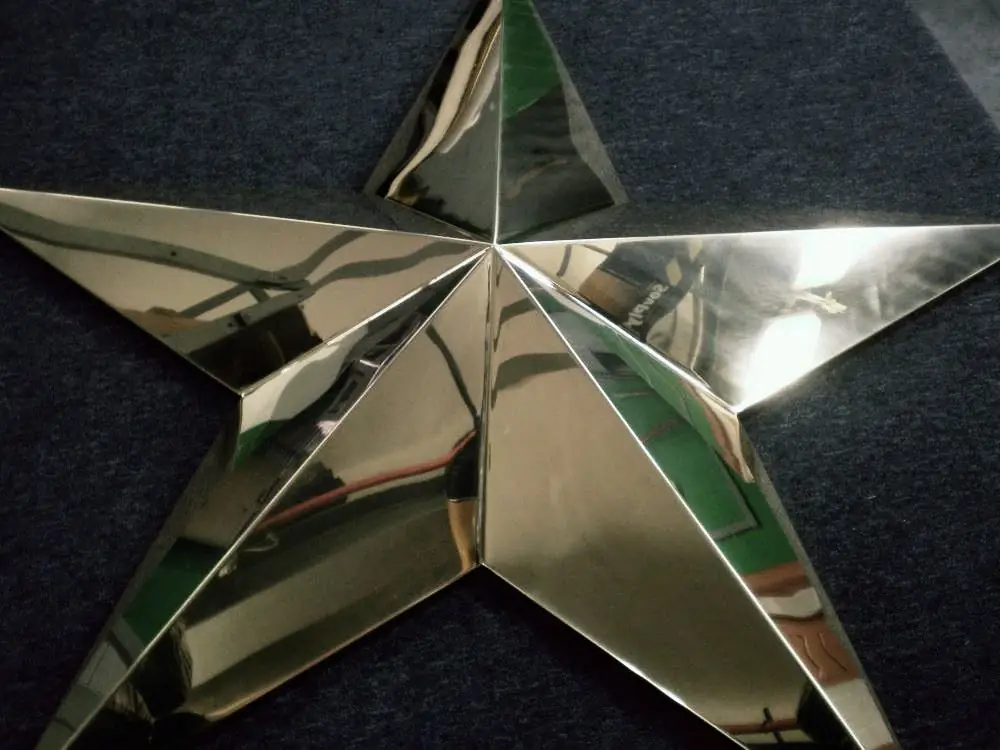
Para cubrir los materiales en nuestro tiempo, se utiliza toda una gama de tecnologías diferentes. Existen tecnologías de recubrimiento al vacío, radiación de electrones y protones, síntesis a alta temperatura y muchas otras. En el mundo moderno, los adornos y productos decorativos "dorados" son cada vez más populares
Ingeniero de procesos: descripción del puesto. Ingeniero de procesos: responsabilidades laborales
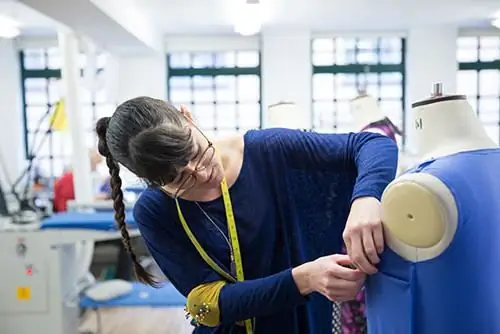
La descripción del trabajo de un ingeniero de procesos es una adición al contrato de trabajo y define los deberes, derechos y grado de responsabilidad de la persona que solicita la vacante especificada. Este documento administrativo tiene por objeto precisar las facultades del aparato administrativo en relación con el tecnólogo especialista, así como designar las funciones de un empleado
Cuentas por cobrar y cuentas por pagar es La relación entre las cuentas por cobrar y las cuentas por pagar. Inventario de cuentas por cobrar y por pagar
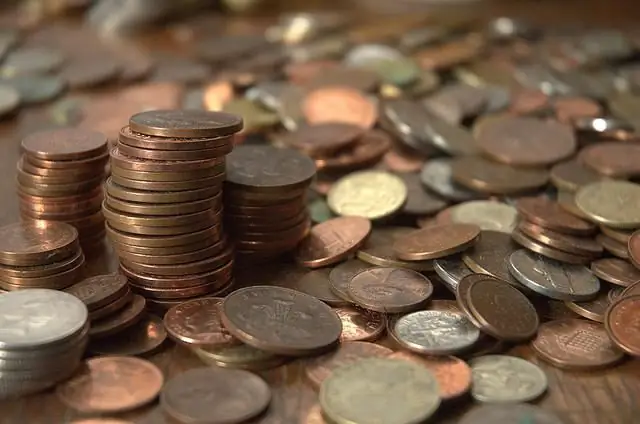
En el mundo moderno, varios elementos contables ocupan un lugar especial en la gestión de cualquier empresa. El material que se presenta a continuación analiza en detalle las obligaciones de deuda bajo el nombre de "cuentas por cobrar y por pagar"
Soldadura a tope: equipos, métodos y tecnología de procesos
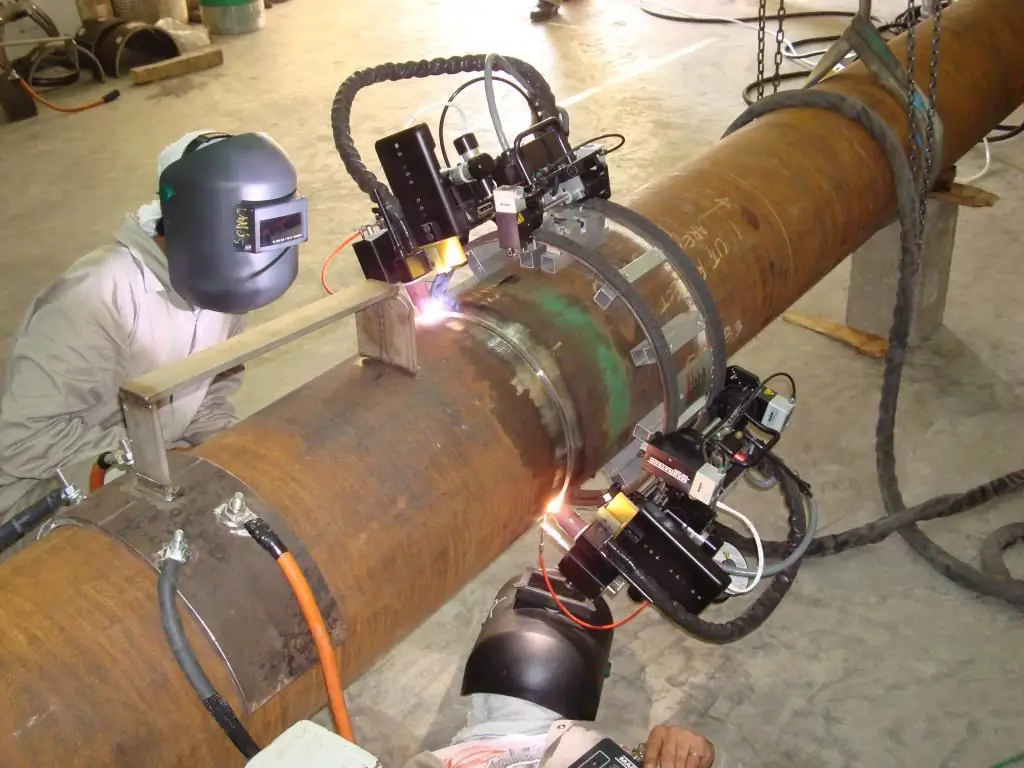
Características de la soldadura a tope flash. Tipos de uniones de soldadura a tope, así como equipos, métodos y tecnología para llevar a cabo el proceso de soldadura a tope. Defectos en la costura de soldadura derivados de la soldadura a tope, así como las razones de su formación