2025 Autor: Howard Calhoun | calhoun@techconfronts.com. Última modificación: 2025-01-24 13:15
Como muestra la práctica, los sistemas de inyección convencionales con un diseño moderno permiten dar forma final al producto terminado con contornos claros. En algunos casos, se utilizan diseños especiales cuando el metal sufre una transformación larga y compleja. Estas unidades están equipadas con un colector circular para mejorar las condiciones de llenado.

Modificaciones laterales
Los sistemas de compuertas laterales están equipados con alimentadores ubicados en ángulo recto con la compuerta. Este tipo se usa a menudo en moldes de una o varias ranuras.
Al acercarse a la cavidad de trabajo, el alimentador tiene un espesor reducido, se agrega con el elemento de entrada, cuya sección transversal afecta la cantidad de metal que pasa a través de la cavidad del molde. En los alimentadores de tipo lateral, la materia prima se mueve a lo largo del plano de separación con el posterior llenado de la parte inferior de la cámara de trabajo. En este caso, los conductos de ventilación están bloqueados, lo que dificulta la eliminación del aire. Como resultado, los sistemas de compuertas laterales son más efectivos para piezas de trabajo poco profundas.
Si mueve la cavidad hacia la parte móvil de la unidad, el metal bajo presión también impedirá la extracciónburbujas de aire de las profundidades. Vale la pena señalar que cuando se funden piezas con barras centrales grandes ubicadas perpendicularmente, pueden aparecer una serie de defectos.

Características del bebedero lateral
La colocación del alimentador lateral a lo largo de la línea tangente le permite nivelar el impacto frontal y la turbulencia. La fundición tiene un elemento ancho que se coloca perpendicular al núcleo, y también hay grandes conexiones de aire. Como resultado, no hay porosidad de aire ni chorros que se aproximan.
Con los bebederos tangenciales se obtiene una fundición anular de la más alta calidad, siempre que el ancho de la pieza sea acorde con el de la pieza a trabajar. Es irracional utilizar un mecanismo de este tipo cuando se funden anillos en bruto con un diámetro escalonado y piezas sólidas. Esto se debe al hecho de que cuando el metal gira, se arremolina y esto afecta negativamente el llenado de la parte central, formando huecos en ella. Para solucionar el problema, se utiliza un bebedero de mayor diámetro.
El cálculo del sistema de compuerta requiere tener en cuenta el ancho del colector de admisión y su ubicación. Estos factores afectan la calidad de la fundición. Cabe señalar que cuando el bebedero se encuentra cerca de la parte ancha de la pieza de trabajo, el metal fluirá en un chorro ancho, arremolinándose y llenando prematuramente las ranuras de ventilación. Si el sistema se monta en el lado estrecho de la pieza, el material fluirá a lo largo de las paredes sin turbulencia significativa.
Sistemas de guías centrales
Las variantes centrales se utilizan para colar losas conse proporciona un campo central libre (marcos, anillos). También se utilizan para producir piezas cilíndricas y en forma de caja con una cavidad central abierta.

Esta característica de diseño le permite montar el bebedero en el centro del eje desde el lado frontal. En este caso, se pueden utilizar varios alimentadores. Los agujeros centrales se utilizan en la fabricación de piezas con cavidades, cuyo fondo tiene un agujero. Se pasa una varilla a través de él, transformándose en un divisor. Este elemento puede pasar estrictamente por el centro o con un desplazamiento, lo que permite colocar el molde en la cavidad de forma asimétrica al elemento de rodadura.
Entre los beneficios de los sistemas de guías centrales para el moldeo por inyección se encuentran los siguientes:
- Es posible llenar la cavidad de trabajo con varios alimentadores sin que se formen chorros de metal.
- El diseño tiene el mismo régimen de temperatura de todas las superficies de trabajo, lo que garantiza la exclusión de deformaciones superficiales.
- Reducción significativa garantizada en la trayectoria del metal sin chorro adicional desde la cámara de compresión.
- Proporciona la misma dirección de entrada de metal y extracción de aire.
Para el correcto funcionamiento de la unidad y la eliminación de turbulencias, el chorro debe dirigirse paralelo a la varilla central y las paredes del molde.
Uso de bebederos
Los dispositivos en cuestión se utilizan exclusivamente en formas con un enchufe de trabajo. La fundición de espacios en blanco de paredes delgadas requiere la instalación de varioscomederos Para trabajar con una parte de paredes gruesas y una aerodinámica débil, un elemento será suficiente. Se instala tangencialmente con el compartimento de entrada, lo que permite eliminar al máximo las impurezas del aire cuando entra metal por un lado.
El procesamiento de piezas de trabajo grandes con forma de caja y configuración de cuerpo se lleva a cabo utilizando varios alimentadores de tipo central. Esto le permite proporcionar energía a todas las áreas remotas de la cavidad de trabajo, así como excluir la aparición de un chorro continuo que provoca la delaminación de la materia prima. El valor total de los alimentadores aumenta y las ventajas del molde de fundición central aparecen si la sección transversal del elemento de entrada se excede tanto como para proporcionar energía a la cavidad de trabajo sin interrupciones en el chorro de metal líquido en cada alimentador.

Alimentadores directos
Los alimentadores centrales sin divisores se utilizan para estructuras de fundición, cuya configuración no permite la instalación de contrapartes laterales. En este caso, los elementos del sistema de compuerta se montan directamente en la pieza, también sirven como alimentador. Es razonable utilizar modificaciones directas para moldear piezas en bruto compactas de paredes gruesas, que se procesan a bajas velocidades mediante alimentadores de gran sección.
El llenado cuando se trabaja en tales condiciones no es particularmente difícil. El énfasis principal está en sellar el metal con la presión final. Los resultados óptimos en el proceso se obtienen cuando la carga sobre la materia prima no se elimina antes del período de apertura del molde de trabajo (cámara del prensado).tipo).

Modelos de colectores circulares
Se utilizan sistemas de inyección similares para fundiciones de acero cuando es imposible proporcionar un llenado suficiente de todas las partes remotas de la cámara de trabajo con un alimentador. El objetivo principal de la unidad es suministrar metal sincrónicamente a todos los compartimentos periféricos, después de lo cual la materia prima ingresa a puntos difíciles de alimentar utilizando varios elementos de entrada.
Este diseño es apropiado en presencia de partes remotas del bebedero que no encajan en las dimensiones generales estándar. Además, una configuración de este tipo es adecuada para moldear piezas en bruto de celosía, que se ven obstaculizadas en la fabricación debido a la estructura de paredes delgadas. Esto es especialmente importante si las varillas se instalan cerca de compartimentos remotos. Cuando la rejilla disminuye, el encuentro de dos chorros en cavidades estrechas prácticamente no experimenta obstáculos de vórtice, en contraste con un proceso similar en cavidades de gran volumen.

Operación
Los sistemas de fundición de colectores circulares se utilizan para mecanizar ruedas dentadas pequeñas de paredes delgadas que tienen un paso ancho y tribok. Los alimentadores con una sección transversal pequeña y un grosor de aproximadamente 0,5 mm se suministran a cada diente desde el colector.
El uso de alimentadores direccionales permite expulsar el aire del metal incluso en lugares de difícil acceso y poca ventilación. Son ideales para la fundición de piezas en bruto en configuraciones de caja y carcasa. El diseño evitacausando impactos frontales y remolinos excesivos.
Formulario de prensa
Este elemento de fundición es un dispositivo complejo para producir productos de metal, polímero y caucho de varias formas. La unidad se utiliza para moldear una variedad de productos bajo la presión de las máquinas de moldeo por inyección. El molde puede ser de varios tipos:
- Tipo mecánico.
- Semiautomático o automático.
- Montaje fijo y desmontable.
- Con planos de división horizontal y vertical.

El conjunto incluye una matriz fija y una parte activa. Las cavidades de formación de estas piezas están diseñadas de forma inversa, lo que permite proporcionar la impresión requerida de la pieza de trabajo. Las materias primas se suministran mediante un sistema de compuertas y la temperatura se controla mediante el agua que circula en el circuito de refrigeración.
Recomendado:
Sistema hidráulico: cálculo, esquema, dispositivo. Tipos de sistemas hidráulicos. Reparar. Sistemas hidráulicos y neumáticos
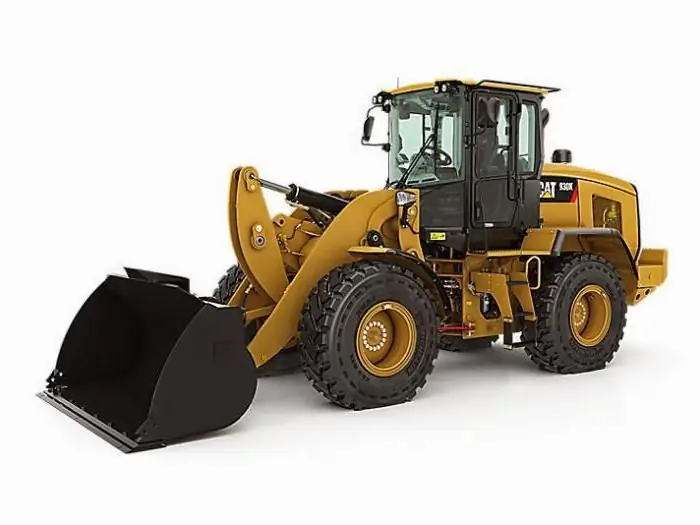
El sistema hidráulico es un dispositivo especial que funciona según el principio de una palanca líquida. Este tipo de unidades se utilizan en los sistemas de frenado de automóviles, en carga y descarga, maquinaria agrícola e incluso en la industria aeronáutica
Tipos de fundición, clasificación, composición, propiedades, marcado y aplicación
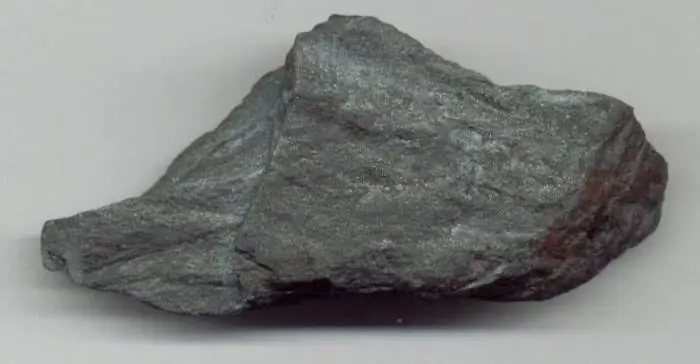
Los tipos de hierro fundido que existen hoy en día le permiten a una persona crear muchos productos. Por lo tanto, hablaremos sobre este material con más detalle en este artículo
Fundición en molde de silicona: equipamiento. Fundición al vacío en moldes de silicona
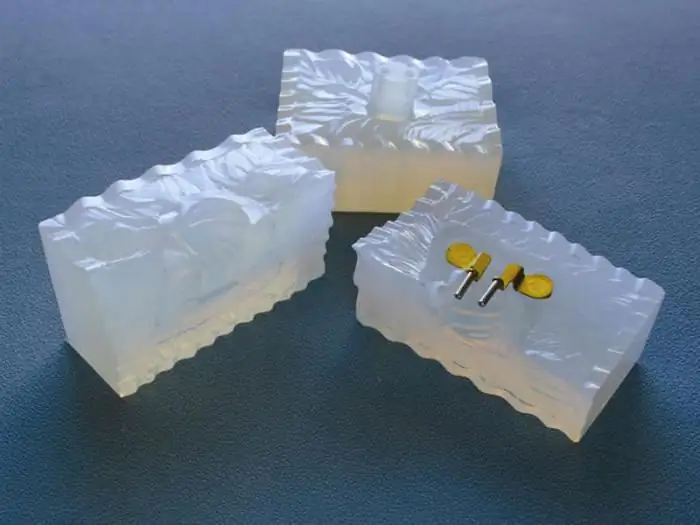
Para la fabricación de una pequeña cantidad de piezas de plástico, se suele utilizar la fundición al vacío en moldes de silicona. Este método es bastante económico (hacer un molde de metal requiere más tiempo y dinero). Además, los moldes de silicona se usan repetidamente y esto también reduce significativamente el costo de producción
Fundición en molde de carcasa: operaciones básicas de fabricación de moldes
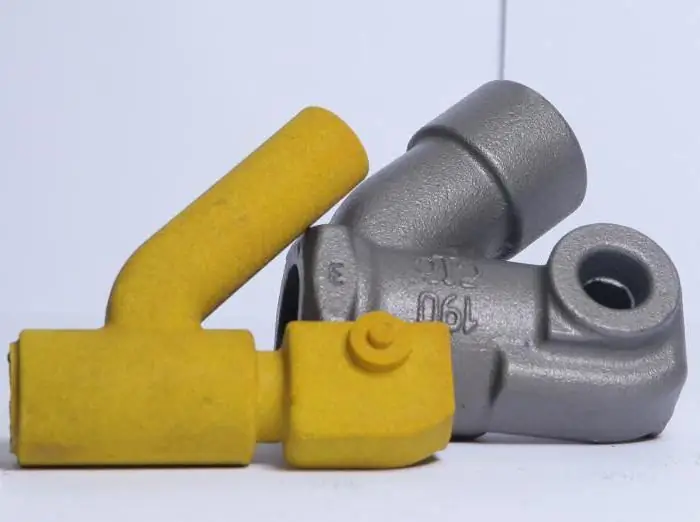
Actualmente, la industria está muy desarrollada y se utilizan muchos métodos diferentes en la fundición. Uno de estos métodos es la fundición de conchas
Tipos de contabilidad. Tipos de cuentas contables. Tipos de sistemas contables
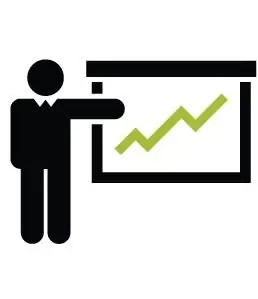
La contabilidad es un proceso indispensable en términos de creación de una política financiera y de gestión eficaz para la mayoría de las empresas. ¿Cuáles son sus características?