2025 Autor: Howard Calhoun | [email protected]. Última modificación: 2025-01-24 13:15
La fundición en moldes de cáscara también se llama fundición de cáscara. Y en el extranjero, este método de trabajo se llama Shell.
Información general
En la industria industrial actual, se utilizan muchos métodos de fundición diferentes. Además de la fundición de cáscara, también se utiliza la fundición de inversión, así como en moldes de metal y varios otros métodos. La ventaja general de estos métodos de fundición, en comparación con el moldeo en arena, es que dan como resultado materiales finales más precisos en términos de forma y dimensiones. Además, se reduce el número de asperezas en la superficie de tales productos. En casos más raros, pero aún sucede que se elimina la necesidad de un mecanizado posterior después de la fundición. Además de todo, el uso de la fundición en moldes de cáscara y otros métodos contribuye a que este proceso pueda mecanizarse al máximo, por lo que también aumenta su automatización. Y esto, por supuesto, aumenta enormemente la productividad de cualquier instalación industrial.
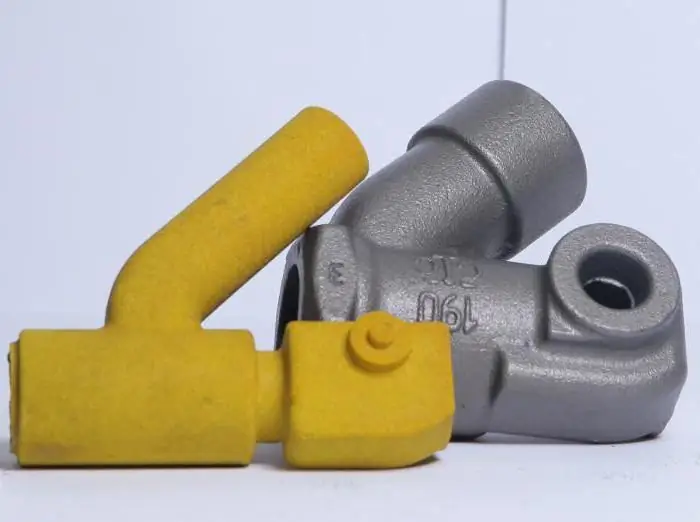
Lanzamiento de proyectiles
Si hablamos específicamente de estométodo, se introdujo por primera vez en las fábricas en 1953. En la actualidad, el método se utiliza bastante. Es la fundición en moldes de carcasa, por ejemplo, lo que produce la mayoría de las piezas para el tractor Kirovets. Todas las piezas que se producen con este método son de acero o hierro fundido de la más alta calidad. Shell casting es un método en el que el resultado final de la fundición tiene una forma que consta de dos conchas de arena y resina. Además, este método de fabricación de piezas se usa solo en los casos en que es necesario crear una pieza con dimensiones pequeñas o medianas, pero al mismo tiempo con alta precisión. Ejemplos de aplicaciones para este método de fundición son piezas de motores o piezas de fundición de pared delgada.
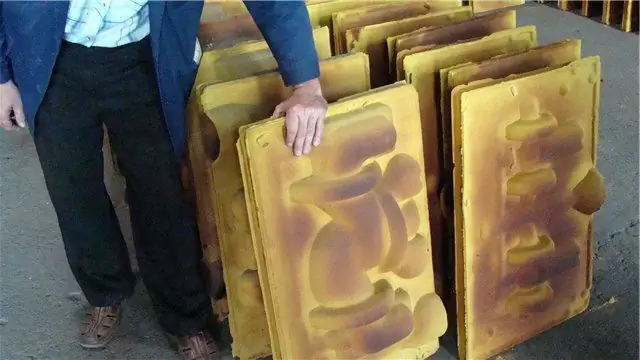
La esencia del camino
Con este método de trabajo se pueden obtener diversas piezas para ventiladores, motores, bombas o máquinas textiles. Sin embargo, la longitud máxima del producto recibido no puede exceder 1 metro, y no puede pesar más de 200 kg.
La esencia de la fundición en moldes de cáscara se basa en ciertas propiedades de las resinas termoendurecibles, que forman parte de las mezclas de arena y resina. La ventaja de usar tales componentes es que estas resinas tienden a endurecerse rápida y permanentemente cuando se tratan a una temperatura de 200-250 grados centígrados.
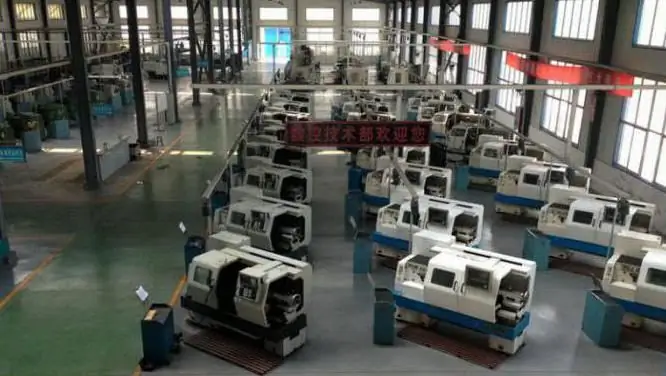
Haciendo un molde de cáscara para fundición
Para hacer un molde para la fundición posterior, es necesario contar con arena de cuarzo de grano fino, que viene con la adición de una resina termoendurecible, que es su elemento de conexión para obtener un molde de cáscara completo. Estos materiales, en particular la resina, se eligen porque se endurecen cuando pasan una determinada barrera de temperatura. El proceso de fabricación es el siguiente. Primero, la resina se calienta a 140-160 grados centígrados. Bajo la influencia de dicho entorno, se convierte en una masa adhesiva líquida que envuelve completamente el molde de arena de cuarzo.
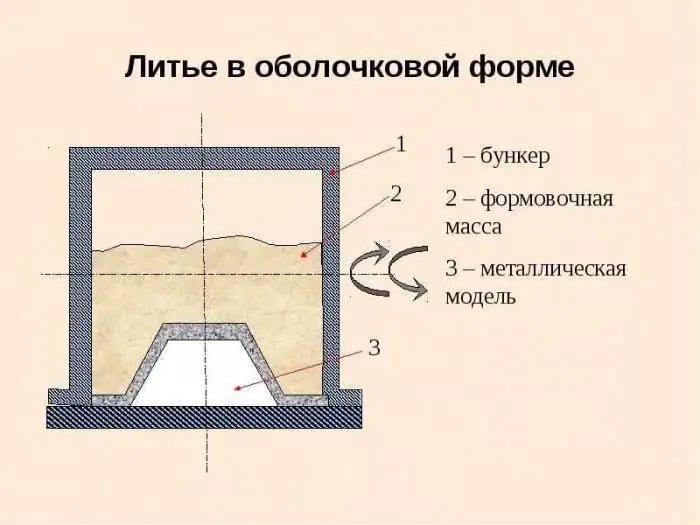
El alcance de la fundición en moldes de cáscara es bastante amplio y, por lo tanto, el proceso de fabricación de moldes se lleva a automático o automatizado.
Una vez que el molde está completamente cubierto con resina, la temperatura aumenta a 200-250 grados centígrados. Este umbral de temperatura es suficiente para que la masa adhesiva se endurezca irreversiblemente y adopte una forma. Además, cuando comienza el proceso de fundición de las piezas, es decir, cuando el metal fundido entra en el molde, la temperatura en él alcanza unos 600 grados. Este modo es suficiente para garantizar que la resina no se derrita, sino que se queme, dejando poros en el propio molde, lo que facilita la salida de gases.
Ventajas y desventajas de la fundición en molde de cáscara
Como cualquier otro proceso de fabricación, este tiene sus pros y sus contras. Si comparamos este método de fundición, por ejemplo, con la fundición enmoldes de arena ordinarios, hay varias ventajas:
- La primera y bastante significativa diferencia es la clase de precisión, que es 7-9. Además, se mejora el acabado superficial de la pieza obtenida hasta 3-6. Además, se reducen los márgenes, que se permiten para el mecanizado posterior de la pieza resultante después de la fundición.
- Una de las grandes ventajas es una reducción significativa en los costos de mano de obra para la fabricación de piezas fundidas.
- Este método de fundición reduce el consumo de materiales de moldeo, así como la cantidad de metal debido a que se reduce el tamaño de los canales de la puerta.
- Se redujo significativamente la cantidad de producción de matrimonio.
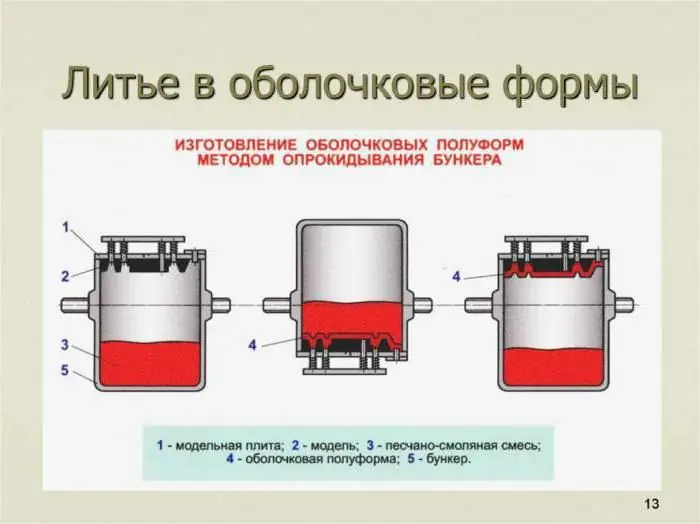
Sin embargo, hay algunas desventajas de colar en moldes de cáscara. Estos incluyen:
- Vida útil del molde de la carcasa: 1 fundición.
- El costo de moldear arena es bastante alto.
- Alto porcentaje de gases nocivos.
Proceso de formación de corpus
El proceso de formación del cuerpo se lleva a cabo en seis etapas:
- El primer paso es el proceso de verter la mezcla sobre un modelo de metal caliente, así como el proceso de mantenerlo durante varias decenas de segundos hasta que se forme una costra fina y fuerte alrededor de la pieza. En la mayoría de los casos, los modelos están hechos de hierro fundido y su calentamiento se realiza hasta 230-315 grados.
- Después de eso, es necesario realizar una operación para eliminar el exceso de arena de moldeo. El espesor de la corteza eventualmente debe ser de 10 a 20milímetro Depende del tiempo de residencia de la mezcla en el modelo, así como de la temperatura.
- Después de eso, es necesario transferir la placa del modelo junto con el molde al horno, donde estarán hasta el final del proceso de curado. Al final de este procedimiento, la resistencia del caparazón debe estar entre 2,4 y 3,1 MPa.
- Después de retirarse del horno, la capa endurecida se desplaza de la placa. Para este procedimiento se utiliza un empujador especial.
- Después de eso, se unen dos o más modelos usando algún tipo de abrazadera o pegando. Estos moldes se pueden utilizar para colar en moldes de concha o simplemente almacenarse. Vida útil casi ilimitada.
- Antes de comenzar el proceso de fundición en el molde terminado, se vierte granalla en ellos, lo que ayuda a prevenir o destruir el molde durante el vertido posterior.
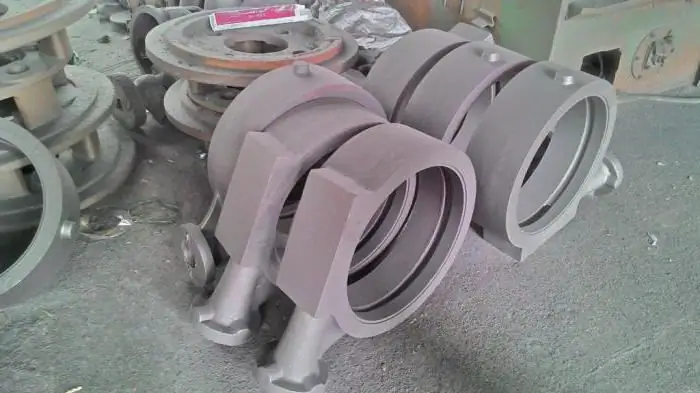
Detalles del reparto
Vale la pena comenzar con el hecho de que las tolerancias típicas que se permiten en la fabricación de herramientas pueden ser de 0,5 mm. La rugosidad de la superficie está permitida en el rango de 0,3 a 0,4 micras. Tales límites se justifican por el hecho de que se utiliza arena de grano fino. También vale la pena señalar: el uso de resina contribuye en gran medida al hecho de que la superficie es muy suave.
Volumen de producción
Para dedicarse a la producción de dichos moldes y piezas, es necesario asistir a la instalación de un modelo de molde. El tiempo requerido para la instalación es menos de una semana. Una vez completada la instalación, la cantidad de salida puedealcance de 5 a 50 piezas por hora. Dichos volúmenes de producción por hora son bastante reales, sin embargo, para esto es necesario preparar el proceso de fundición en consecuencia. Los principales materiales que se requerirán para la fundición son hierro fundido, aluminio, cobre, así como aleaciones de este tipo de metales. Otro material necesario será una aleación que utilice aluminio y magnesio.
Recomendado:
Operaciones de efectivo y crédito de los bancos. Tipos de operaciones bancarias
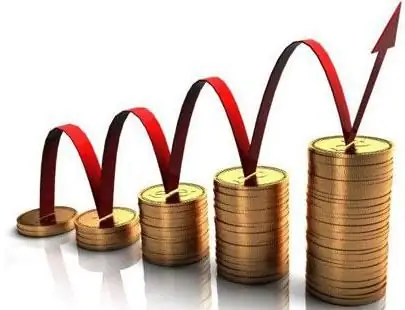
Las principales operaciones que realiza un banco comercial son crédito y efectivo. ¿Cuáles son sus detalles? ¿Según qué reglas se llevan a cabo?
Fundición en molde de silicona: equipamiento. Fundición al vacío en moldes de silicona
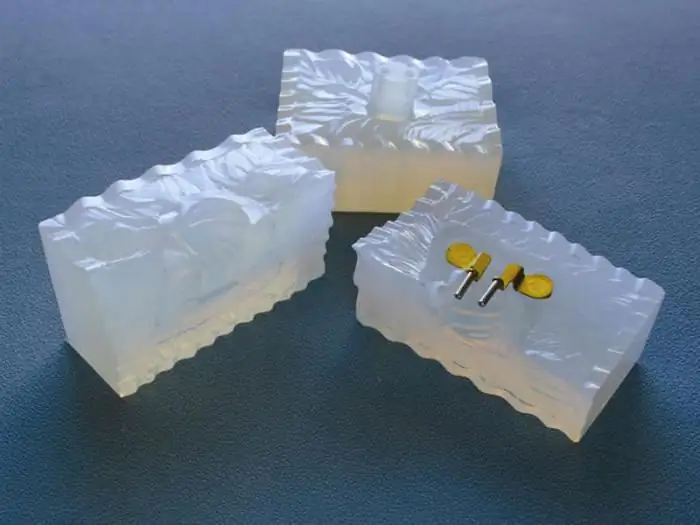
Para la fabricación de una pequeña cantidad de piezas de plástico, se suele utilizar la fundición al vacío en moldes de silicona. Este método es bastante económico (hacer un molde de metal requiere más tiempo y dinero). Además, los moldes de silicona se usan repetidamente y esto también reduce significativamente el costo de producción
Moldes de fundición: características, tecnología, tipos
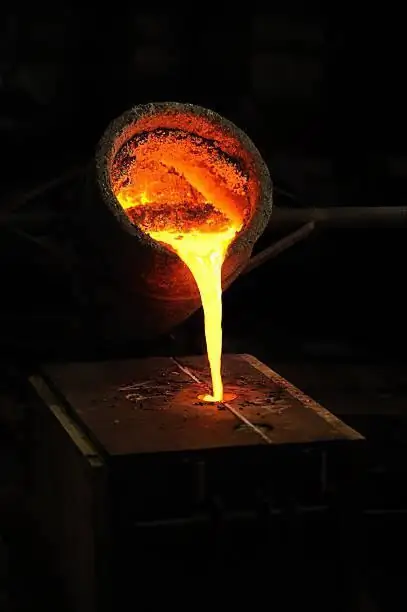
Uno de los procesos más importantes de la industria es el proceso de fundición de varias piezas, materias primas y otras cosas. Sin embargo, para producir con éxito lo deseado, es necesario hacer un molde, lo que determina en gran medida el resultado final
Sistemas de gating: tipos, dispositivo. Molde de fundición
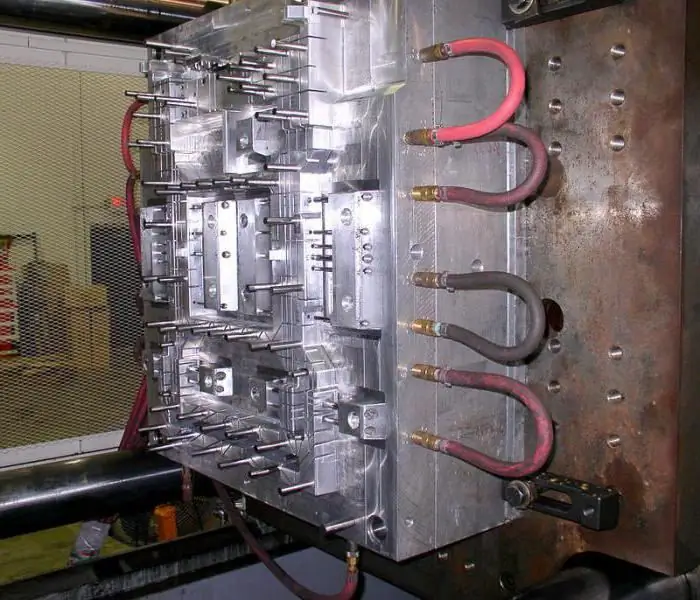
Sistemas de gating: principio de funcionamiento, descripción, características, dispositivo, funcionamiento. Molde para fundición: propósito, características, foto
Tipos de operaciones bancarias. Servicios de liquidación y caja. Operaciones de bancos con valores
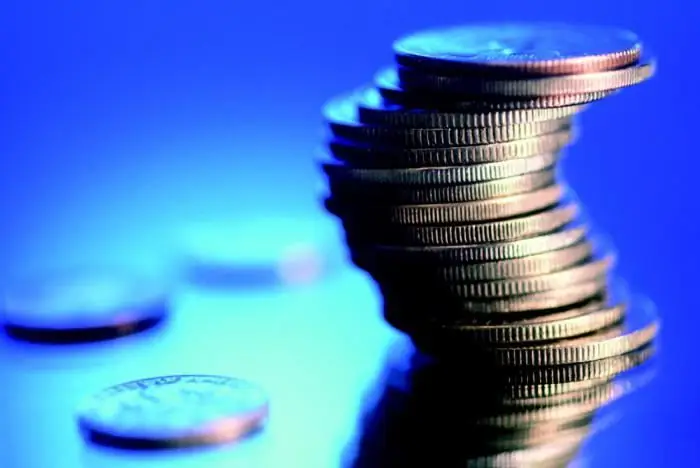
Antes de saber qué tipos de transacciones bancarias existen, debe comprender algunas de las definiciones más importantes. Por ejemplo, ¿cuál es la institución en cuestión en sí? En la terminología económica moderna, el banco actúa como una unidad financiera y crediticia que realiza todo tipo de operaciones tanto con dinero como con valores