2025 Autor: Howard Calhoun | [email protected]. Última modificación: 2025-01-24 13:15
Prácticamente no hay industria donde no se realice soldadura. La gran mayoría de las estructuras metálicas se montan e interconectan mediante cordones de soldadura. Por supuesto, la calidad de este tipo de trabajo en el futuro depende no solo de la confiabilidad del edificio, estructura, máquina o cualquier unidad que se construya, sino también de la seguridad de las personas que de alguna manera interactuarán con estas estructuras. Por lo tanto, para garantizar el nivel adecuado de desempeño de tales operaciones, se utilizan pruebas ultrasónicas de soldaduras, gracias a las cuales es posible detectar la presencia o ausencia de diversos defectos en la unión de productos metálicos. Este método de control avanzado se discutirá en nuestro artículo.
Historial de ocurrencia
La detección ultrasónica de fallas como tal se desarrolló en los años 30. Sin embargo, el primer dispositivo que realmente funcionó nació en 1945 gracias a Sperry Products. Durante las siguientes dos décadas, la última tecnología de control ganó reconocimiento mundial y el número de fabricantes de tales equipos aumentó drásticamente.
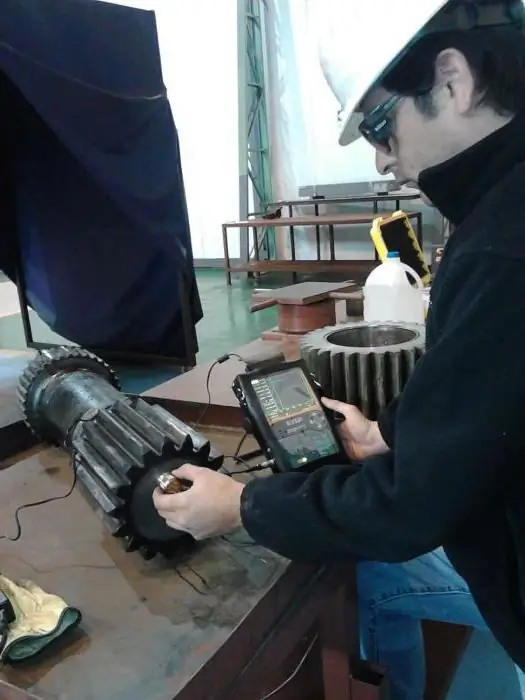
UltrasonidoEl detector de fallas, cuyo precio hoy comienza entre 100 000 y 130 000 mil rublos, inicialmente contenía tubos de vacío. Tales dispositivos eran voluminosos y pesados. Trabajaban exclusivamente con fuentes de alimentación de CA. Pero ya en los años 60, con la llegada de los circuitos semiconductores, los detectores de fallas se redujeron significativamente en tamaño y podían operar con baterías, lo que eventualmente hizo posible usar los dispositivos incluso en condiciones de campo.
Entra en la realidad digital
En las primeras etapas, los instrumentos descritos utilizaban procesamiento de señales analógicas, por lo que, como muchos otros dispositivos similares, estaban sujetos a desviaciones en el momento de la calibración. Pero ya en 1984, Panametrics lanzó el primer detector de fallas digital portátil llamado EPOCH 2002. A partir de ese momento, las unidades digitales se han convertido en equipos altamente confiables, idealmente brindando la calibración necesaria y la estabilidad de medición. El detector de fallas ultrasónico, cuyo precio depende directamente de sus características técnicas y la marca del fabricante, también recibió una función de registro de datos y la capacidad de transferir lecturas a una computadora personal.
En el entorno actual, hay cada vez más interés en los sistemas de matriz en fase, que utilizan una tecnología sofisticada basada en elementos piezoeléctricos de elementos múltiples para generar haces direccionales y crear imágenes transversales similares a las ecografías médicas.
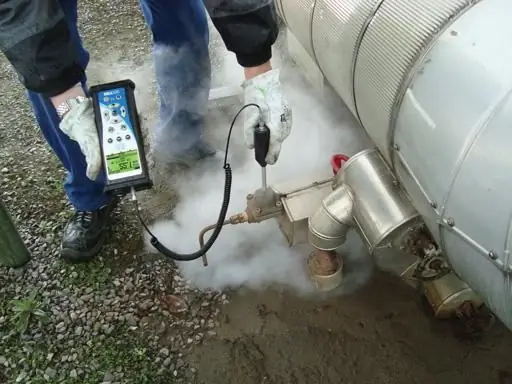
Esferaaplicaciones
El método de control ultrasónico se utiliza en cualquier industria. Su uso ha demostrado que se puede utilizar con la misma eficacia para probar casi todos los tipos de juntas soldadas en la construcción, que tienen un espesor de metal base soldado de más de 4 milímetros. Además, el método se usa activamente para verificar las juntas de gasoductos y oleoductos, varios sistemas hidráulicos y de agua. Y en casos como la inspección de costuras gruesas obtenidas como resultado de la soldadura por electroescoria, la detección ultrasónica de fallas es el único método aceptable de inspección.
La decisión final sobre si una pieza o soldadura es apta para el servicio se toma sobre la base de tres indicadores fundamentales (criterios): amplitud, coordenadas, dimensiones condicionales.
En general, la prueba ultrasónica es exactamente el método más fructífero en términos de imágenes en el proceso de estudio de la costura (detalle).
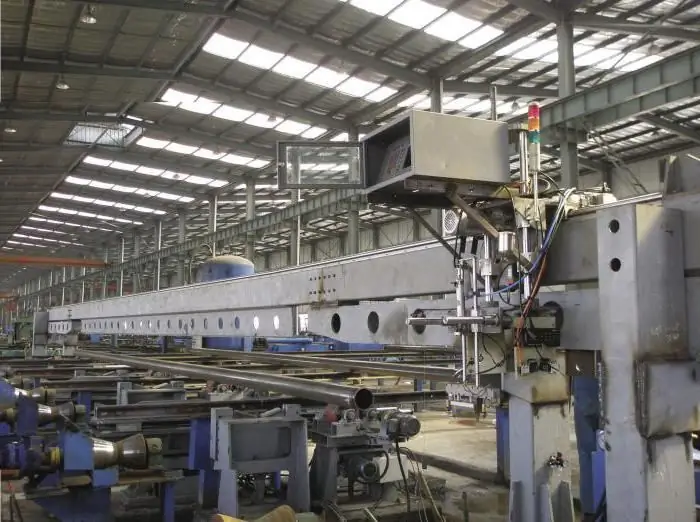
Razones de la demanda
El método descrito de inspección mediante ultrasonido es bueno porque tiene una sensibilidad y una fiabilidad de las indicaciones mucho más altas en el proceso de detección de defectos en forma de grietas, menor costo y alta seguridad en el proceso de uso en comparación con métodos clásicos de inspección radiográfica. Hasta la fecha, la prueba ultrasónica de uniones soldadas se utiliza en el 70-80 % de los casos de inspección.
Transductores ultrasónicos
SinEl uso de estos dispositivos para pruebas ultrasónicas no destructivas es simplemente impensable. Los dispositivos se utilizan para generar excitación, así como para recibir vibraciones de ultrasonido.
Las unidades son diferentes y se clasifican por:
- La forma de crear un contacto con el elemento de prueba.
- El método de conectar elementos piezoeléctricos al circuito eléctrico del detector de fallas y la dislocación del electrodo en relación con el elemento piezoeléctrico.
- Orientación de la acústica con respecto a la superficie.
- Número de elementos piezoeléctricos (simple, doble, multielemento).
- Ancho de banda de las frecuencias operativas (banda estrecha: menos de una octava de ancho de banda, banda ancha: más de una octava de ancho de banda).
Características medibles de los defectos
GOST gobierna todo en el mundo de la tecnología y la industria. Las pruebas ultrasónicas (GOST 14782-86) tampoco son una excepción en este asunto. La norma especifica que los defectos se miden con los siguientes parámetros:
- Área equivalente del defecto.
- Amplitud de la señal de eco, que se determina teniendo en cuenta la distancia al defecto.
- Coordenadas del defecto en el punto de soldadura.
- Tamaños convencionales.
- Distancia condicional entre defectos.
- El número de defectos en la longitud seleccionada de la soldadura o unión.
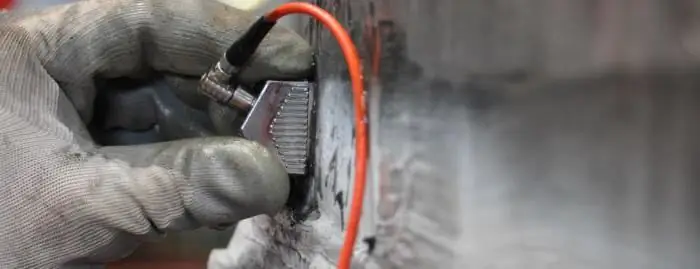
Funcionamiento del detector de fallas
Las pruebas no destructivas, que son ultrasónicas, tienen su propio método de uso, que establece que el principal parámetro medido es la amplitud de la señal de eco obtenidadirectamente del defecto. Para diferenciar las señales de eco por amplitud, se fija el llamado nivel de sensibilidad de rechazo. Esto, a su vez, se configura utilizando la plantilla estándar empresarial (SOP).
El inicio de la operación del detector de defectos va acompañado de su ajuste. Para ello, se establece la sensibilidad de rechazo. Después de eso, en el proceso de estudios de ultrasonido en curso, la señal de eco obtenida del defecto detectado se compara con el nivel de rechazo fijado. Si la amplitud medida excede el nivel de rechazo, los expertos deciden que tal defecto es inaceptable. Entonces la costura o producto es rechazado y enviado para revisión.
Los defectos más comunes de las superficies soldadas son: f alta de fusión, penetración incompleta, agrietamiento, porosidad, inclusiones de escoria. Son estas violaciones las que se detectan de manera efectiva mediante la detección de fallas mediante ultrasonido.
Opciones ultrasónicas
Con el tiempo, el proceso de inspección ha desarrollado varios métodos poderosos para examinar soldaduras. Las pruebas ultrasónicas brindan una cantidad bastante grande de opciones para el examen acústico de las estructuras metálicas consideradas, sin embargo, las más populares son:
- Método de eco.
- Sombra.
- Método espejo-sombra.
- Espejo de eco.
- Método Delta.
Método número uno
La mayoría de las veces en la industria y el transporte ferroviario se utiliza el método de pulsos de eco. Es gracias a él que se diagnostican más del 90% de todos los defectos, lo que es posible gracias al registro y análisis de casi todas las señales reflejadas desde la superficie del defecto.
Este método en sí se basa en el sondeo de un producto metálico con pulsos de vibraciones ultrasónicas, seguido de su registro.
Las ventajas del método son:
- la posibilidad de acceso unidireccional al producto;
- bastante alta sensibilidad a los defectos internos;
- la mayor precisión en la determinación de las coordenadas del defecto detectado.
Sin embargo, también hay desventajas, que incluyen:
- baja resistencia a la interferencia de los reflectores de superficie;
- Fuerte dependencia de la amplitud de la señal en la ubicación del defecto.
La detección de fallas descrita implica el envío de pulsos ultrasónicos al producto por parte del buscador. La señal de respuesta es recibida por él o por el segundo buscador. En este caso, la señal puede reflejarse tanto directamente desde los defectos como desde la superficie opuesta de la pieza, producto (costura).
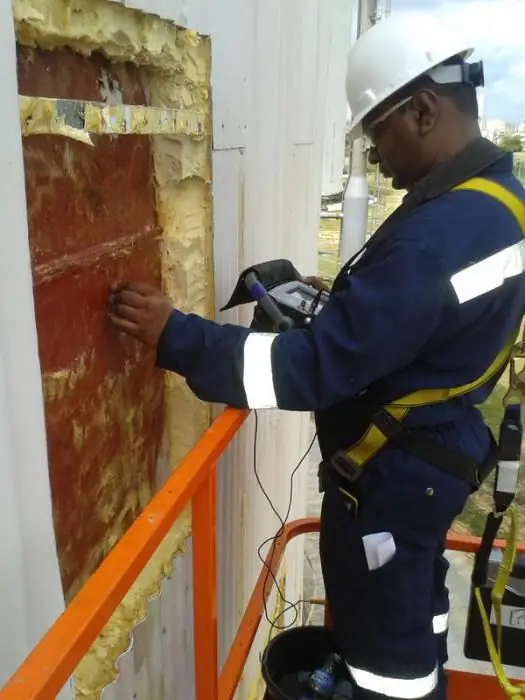
Método de la sombra
Se basa en un análisis detallado de la amplitud de las vibraciones ultrasónicas transmitidas desde el transmisor al receptor. En el caso de que haya una disminución en este indicador, esto indica la presencia de un defecto. En este caso, cuanto mayor sea el tamaño del propio defecto, menor será la amplitud de la señal recibida por el receptor. Para obtener información confiable, el emisor y el receptor deben colocarse coaxialmente en lados opuestosobjeto en estudio. Las desventajas de esta tecnología pueden considerarse la baja sensibilidad en comparación con el método de eco y la dificultad de orientar los PET (transductores piezoeléctricos) en relación con los haces centrales del patrón de radiación. Sin embargo, también hay ventajas, que son una alta resistencia a las interferencias, una baja dependencia de la amplitud de la señal de la ubicación del defecto y la ausencia de una zona muerta.
Método de sombra de espejo
Este control de calidad ultrasónico se usa más comúnmente para inspeccionar juntas de barras de refuerzo soldadas. El principal signo de que se ha detectado un defecto es el debilitamiento de la amplitud de la señal, que se refleja desde la superficie opuesta (más a menudo llamada fondo). La principal ventaja del método es la detección clara de varios defectos, cuya dislocación es la raíz de la soldadura. Además, el método se caracteriza por la posibilidad de acceso unilateral a la costura o pieza.
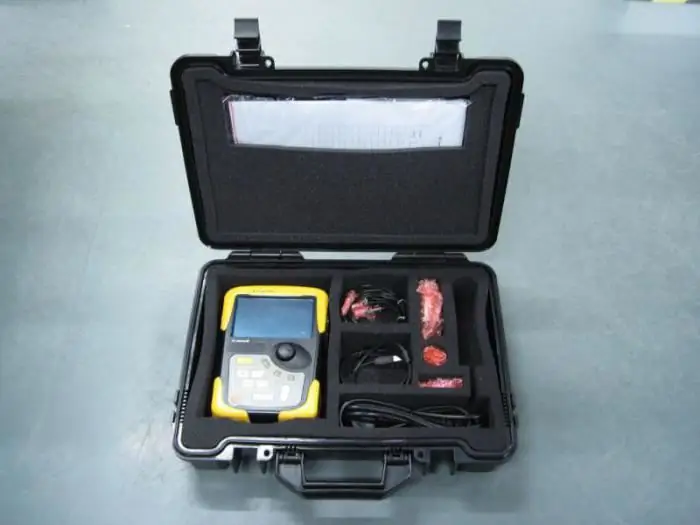
Método de espejo de eco
La forma más efectiva de detectar defectos verticales. La verificación se lleva a cabo utilizando dos sondas, que se mueven a lo largo de la superficie cerca de la costura en un lado de la misma. Al mismo tiempo, su movimiento se lleva a cabo de manera que una sonda fije la señal emitida por otra sonda y reflejada dos veces por el defecto existente.
La principal ventaja del método: se puede utilizar para evaluar la forma de los defectos, cuyo tamaño supera los 3 mm y que se desvían en el plano vertical en más de 10 grados. El más importante -utilice sondas con la misma sensibilidad. Esta versión del examen ultrasónico se usa activamente para verificar productos de paredes gruesas y sus soldaduras.
Método Delta
La prueba ultrasónica especificada de soldaduras utiliza energía ultrasónica reirradiada por el defecto. La onda transversal que incide sobre el defecto se refleja parcialmente especularmente, se transforma parcialmente en longitudinal y también reirradia la onda difractada. Como resultado, se capturan las ondas PET requeridas. La desventaja del método puede considerarse la limpieza de la costura, la complejidad bastante alta de descifrar las señales recibidas durante el control de juntas soldadas con un espesor de hasta 15 milímetros.
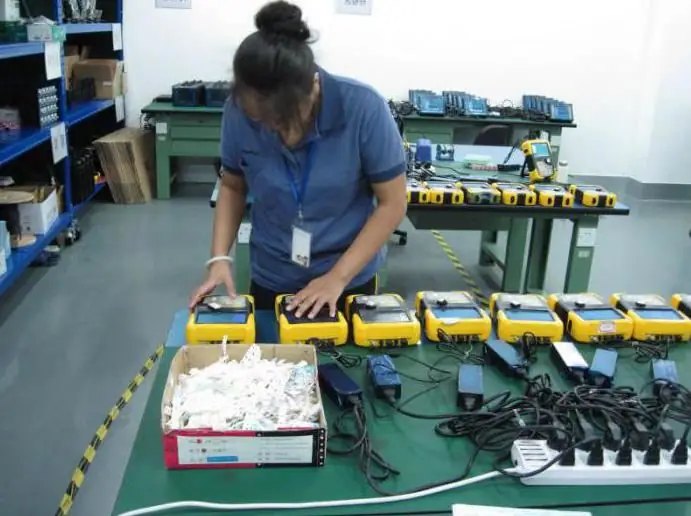
Ventajas del ultrasonido y sutilezas de su aplicación
El examen de uniones soldadas utilizando sonido de alta frecuencia es, de hecho, un ensayo no destructivo, porque este método no es capaz de causar ningún daño a la sección investigada del producto, pero al mismo tiempo determina con bastante precisión la presencia de defectos. Asimismo, merece especial atención el bajo coste de los trabajos realizados y su elevada rapidez de ejecución. También es importante que el método sea absolutamente seguro para la salud humana. Todos los estudios de metales y soldaduras basados en ultrasonido se realizan en el rango de 0,5 MHz a 10 MHz. En algunos casos, es posible realizar trabajos utilizando ondas ultrasónicas con una frecuencia de 20 MHz.
El análisis de una unión soldada mediante ultrasonidos debe necesariamente ir acompañado de todo un complejomedidas preparatorias, como limpieza de la costura o superficie en estudio, aplicación de líquidos de contacto específicos en el área controlada (geles especiales, glicerina, aceite de máquina). Todo esto se hace para garantizar un contacto acústico estable adecuado, que finalmente proporciona la imagen necesaria en el dispositivo.
Inutilizable y desventajas
La prueba ultrasónica es absolutamente irracional para examinar juntas de soldadura de metales con una estructura de grano grueso (por ejemplo, hierro fundido o una soldadura austenítica con un espesor de más de 60 milímetros). Y todo porque en tales casos hay una dispersión suficientemente grande y una fuerte atenuación del ultrasonido.
Tampoco es posible caracterizar sin ambigüedades el defecto detectado (inclusión de tungsteno, inclusión de escoria, etc.).
Recomendado:
Métodos básicos de ensayo para hormigón asfáltico
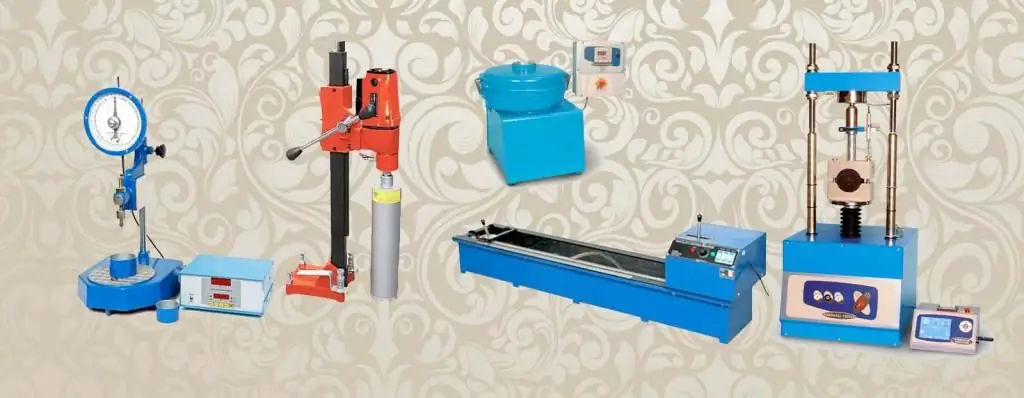
El problema de la calidad de la superficie de las carreteras en nuestro país es extremadamente agudo. Por lo tanto, es muy importante al aceptar el trabajo de los servicios de construcción para llevar a cabo pruebas correctas y de calidad de hormigón armado. Y en base a los resultados de estos trabajos, ya debería tomarse una decisión sobre la puesta en servicio de las instalaciones de infraestructura de transporte por carretera. En este artículo, solo hablaremos sobre las características y reglas (GOST) de las pruebas de hormigón asfáltico
Medidores de resistencia del hormigón. Métodos de ensayo de hormigón
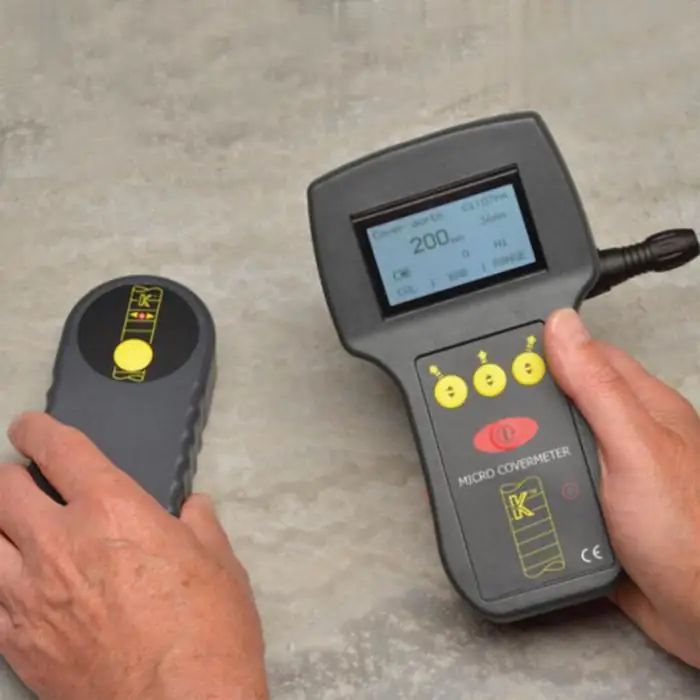
Al construir edificios y estructuras, es muy importante controlar la resistencia del hormigón. Para esto, se utilizan dispositivos especiales. Los parámetros de medición pueden variar bastante
Procesamiento ultrasónico: tecnología, ventajas y desventajas
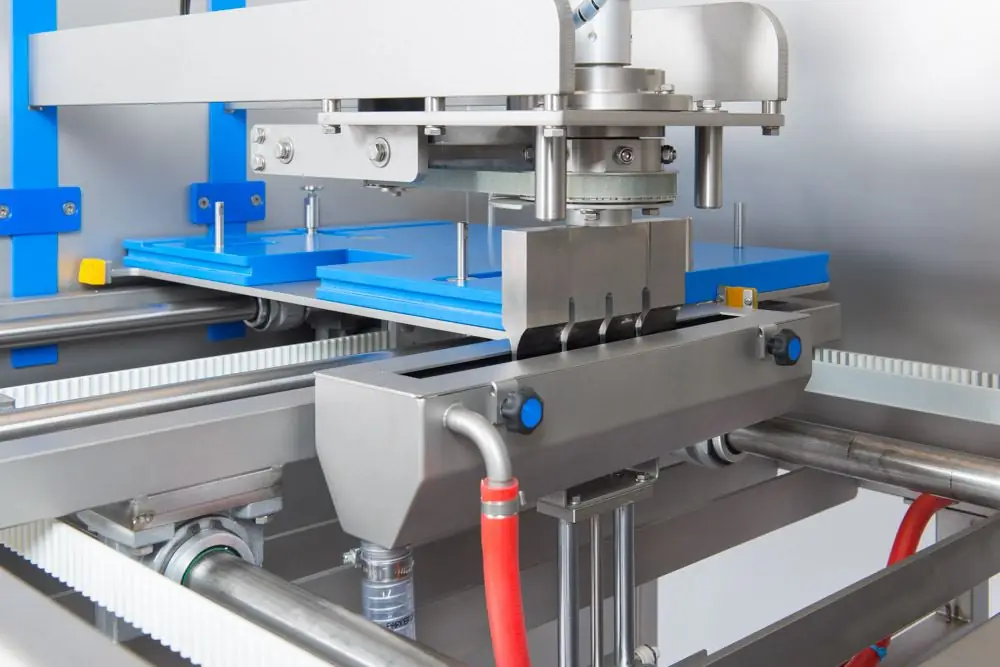
La industria metalúrgica en esta etapa de desarrollo es capaz de resolver las complejas tareas de corte y taladrado de piezas de trabajo de diversos grados de dureza. Esto fue posible gracias al desarrollo de formas fundamentalmente nuevas de influir en el material, incluido un amplio grupo de métodos electromecánicos. Una de las tecnologías más efectivas de este tipo es el tratamiento ultrasónico (UZO), basado en los principios de la radiación electroacústica
Uniones soldadas a tope: características, tipos y tecnología
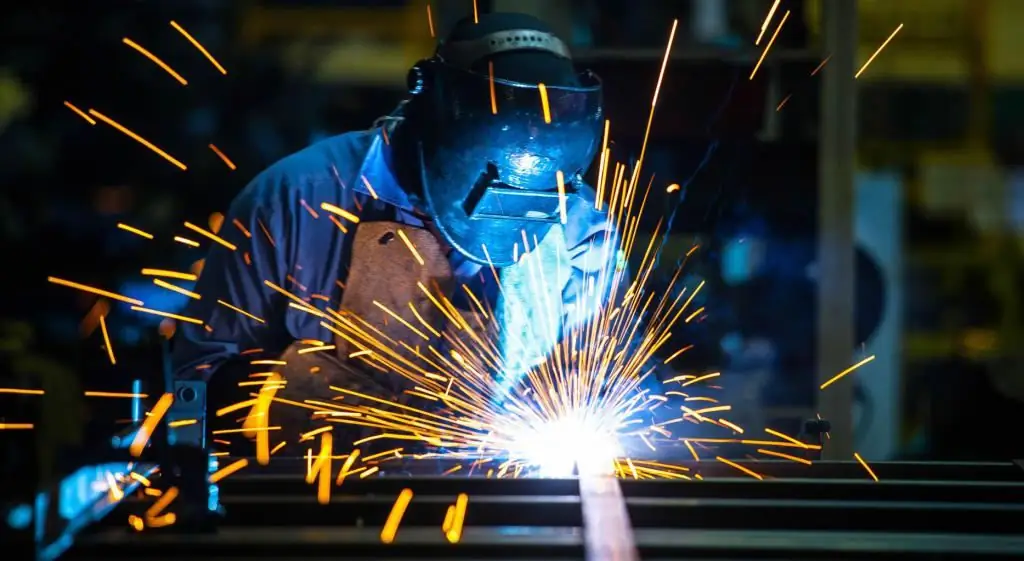
Características y tipos de soldadura. Clasificación de las uniones soldadas a tope según diversos parámetros de la soldadura. Tecnología para crear una junta a tope, según el equipo utilizado. Medidas de seguridad al realizar trabajos de soldadura
Ensayos no destructivos de uniones soldadas: equipos, GOST
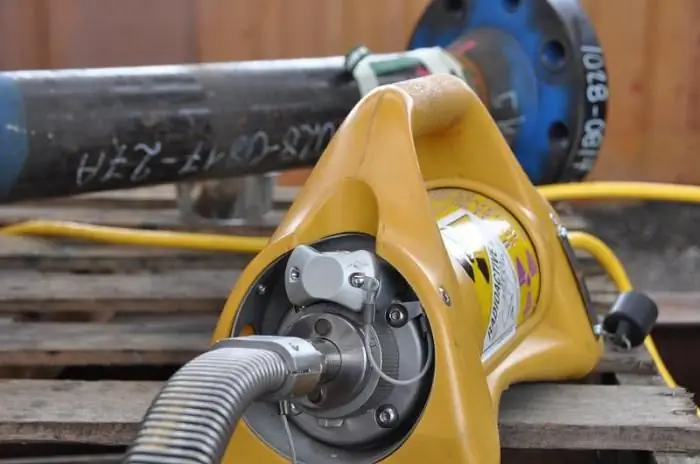
El artículo está dedicado a los métodos de ensayo no destructivo de uniones soldadas. Se describen los métodos de control permitidos por GOST y el equipo utilizado