2025 Autor: Howard Calhoun | [email protected]. Última modificación: 2025-01-24 13:15
El jefe de cualquier empresa, independientemente del campo de actividad, sueña que las ganancias crezcan y los costos de producción permanezcan sin cambios. El sistema "5S" en producción (en la versión inglesa 5S), que se basa únicamente en el uso racional de las reservas internas, ayuda a lograr este resultado.
Este sistema no se creó desde cero. Algo similar a fines del siglo XIX fue propuesto por el estadounidense Frederick Taylor. En Rusia, esto lo hizo el científico, revolucionario, filósofo e ideólogo A. A. Bogdanov, quien publicó un libro sobre los principios de la administración científica en 1911. Sobre la base de las disposiciones establecidas en él, la URSS introdujo el NOT, es decir, la organización científica del trabajo. Pero el más perfecto fue el sistema 5C propuesto por el ingeniero japonés Taiichi Ohno e introducido por él en la planta de producción de Toyota Motor. ¿Qué es y por qué se ha vuelto tan popular el sistema japonés?
El hecho es que se basa en un principio simple que no requiere costos. consiste enel siguiente: cada empleado, desde el limpiador hasta el director, debe optimizar su parte en el flujo de trabajo general tanto como sea posible. Esto conduce a un aumento de la ganancia de la producción en su conjunto ya un aumento de los ingresos de todos sus empleados. Ahora, empresas de todo el mundo, incluida Rusia, han recogido el testigo de la introducción del sistema "5C". En este artículo, intentaremos convencer a los escépticos de que el saber hacer japonés realmente funciona y en absolutamente cualquier campo de actividad.
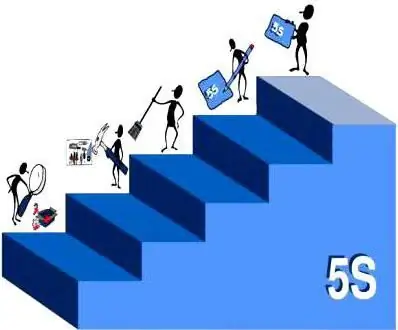
El sistema "5C" en producción, ¿qué es?
International 5S significa cinco pasos ("paso" en inglés paso). Algunos economistas y promotores de una nueva actitud hacia el trabajo explican el nombre por los cinco postulados japoneses que se implementan consistentemente en el sistema 5S: seiri, seiton, seiso, seiketsu y shitsuke. Para nosotros, nuestras "5C" nativas son más cercanas y comprensibles: cinco pasos consecutivos que deben completarse para lograr la prosperidad de nuestra producción. Esto es:
1. Ordenar.
2. Mantener el orden.
3. Mantenerse limpio.
4. Estandarización.
5. Mejora.
Como puede ver, el sistema "5C" no requiere nada sobrenatural en la producción. Tal vez por eso todavía se puede encontrar desconfianza y una actitud frívola hacia ella.
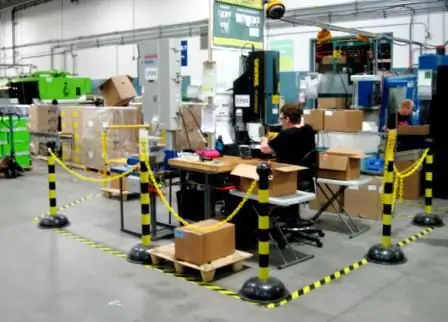
Etapas de creación de un sistema
El sabio japonés Taiichi Ohno, quien, gracias a la introducción de sus métodos en la planta de Toyota, logró ascender deingeniero a director ejecutivo, notó cuántas pérdidas ocurren debido a varias inconsistencias y superposiciones. Por ejemplo, algunos tornillos pequeños no se colocaron a tiempo en el transportador y, como resultado, se detuvo toda la producción. O viceversa, las piezas se suministraron con un margen, resultaron superfluas y, como resultado, uno de los empleados tuvo que devolverlas al almacén, lo que significa perder el tiempo en trabajo vacío. Taiichi Ohno desarrolló un concepto que llamó "justo a tiempo". Es decir, ahora se entregaron al transportador exactamente tantas piezas como se necesitaban.
Se pueden dar otros ejemplos. El sistema "5S" en producción también incluía el concepto de "kanban", que en japonés significa "signo publicitario". Taiichi Ohno sugirió adjuntar una etiqueta llamada "kanban" a cada pieza o herramienta, en la que se proporciona toda la información necesaria sobre la pieza o herramienta. Básicamente, se aplica a cualquier cosa. Por ejemplo, a mercancías, medicinas, carpetas en la oficina. El tercer concepto en el que se basa el sistema 5S en producción es el concepto de “kaizen”, que significa mejora continua. También se concibieron otros conceptos, que eran adecuados solo para procesos de producción altamente especializados. En este artículo, no los consideraremos. Como resultado de todas las innovaciones probadas en la práctica, se han formado 5 pasos que son aplicables a cualquier producción. Analicémoslos en detalle.
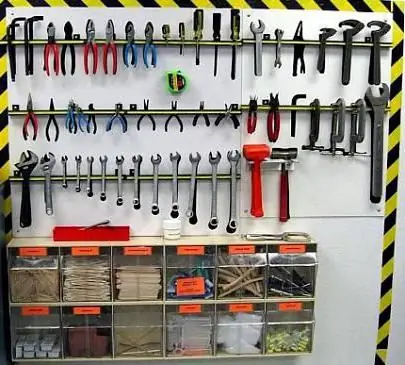
Clasificación
Muchos de nosotros tenemos elementos en nuestros escritorios que, enbásicamente no es necesario. Por ejemplo, formularios antiguos, archivos sin usar, borradores de cálculos, una servilleta en la que había una taza de café. Y entre este caos pueden estar los archivos o documentos necesarios. Los principios básicos del sistema "5S" implican optimizar su flujo de trabajo, es decir, asegurarse de que no se pierda tiempo buscando las cosas correctas entre los escombros de lo innecesario. Esto es clasificar. Es decir, en el lugar de trabajo (cerca de la máquina, en la mesa, en el taller, en cualquier lugar), todos los artículos se colocan en dos pilas: los necesarios y los innecesarios, que deben eliminarse. Además, todo lo que necesita se descompone en las siguientes pilas: "usado a menudo y constantemente", "usado raramente", "casi no usado". Esto completa la clasificación.
Manteniendo el orden
Si solo desmonta los elementos, no tendrá sentido. Es necesario disponer estos elementos (herramientas, documentos) en tal orden que lo que se usa constantemente y con frecuencia esté a la vista, o que se pueda tomar rápidamente y volver a colocar fácilmente. Lo que rara vez se usa se puede enviar a algún lugar en una caja, pero se le debe adjuntar una etiqueta kanban para que después de un tiempo se pueda encontrar con facilidad y precisión. Como puede ver, el sistema 5S en el lugar de trabajo comienza con los pasos más simples, pero en realidad resulta ser muy efectivo. Y además, mejora el estado de ánimo y las ganas de trabajar.
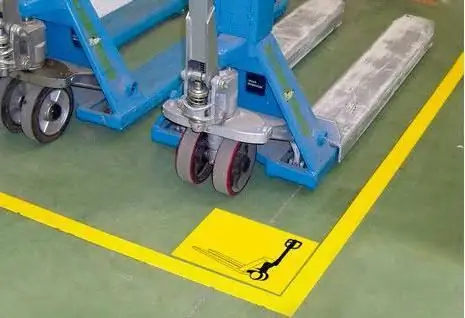
Mantenerse limpio
Este tercer paso es el más lógico para muchos. Nos enseñan a ser limpios desde la infancia. Sobre elen la producción, también es necesario, y no solo las mesas de los trabajadores de oficina o los gabinetes en los establecimientos de restauración, sino también las máquinas, los cuartos de servicio de los limpiadores deben estar limpios. En Japón, los empleados cuidan bien sus lugares de trabajo, se limpian tres veces al día: por la mañana antes del trabajo, a la hora del almuerzo y por la noche, al final de la jornada laboral. Además, sus empresas han introducido un marcado especial de áreas que les permite observar el orden en la producción, es decir, las áreas de productos terminados, el almacenamiento de ciertas piezas, etc. están marcadas con diferentes colores.
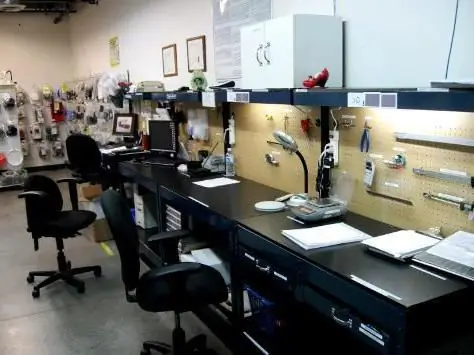
Estandarización
Los principios de estandarización fueron inventados por Taiichi Ohno. También son ampliamente utilizados por el moderno sistema 5S. La gestión de la producción, gracias a la estandarización, recibe una maravillosa herramienta para el control de todos los procesos. Como resultado, las causas de los retrasos en el cronograma se eliminan rápidamente y se corrigen los errores que conducen al lanzamiento de productos de baja calidad. En la planta de Toyota Motor, la estandarización se veía así: los capataces elaboraban planes de trabajo diarios, se publicaban instrucciones precisas en el lugar de trabajo y, al final de la jornada laboral, trabajadores especiales verificaban qué desviaciones del plan ocurrieron durante el día y por qué. Esta es la regla básica de la estandarización, es decir, instrucciones precisas, planes de trabajo y control sobre su implementación. Ahora, muchas empresas, por ejemplo, las plantas de ENSTO en Estonia, están introduciendo un sistema de bonificación para los empleados que cumplen estrictamente con las disposiciones del sistema 5C y, sobre esta base, aumentan su productividad, lo quees un gran incentivo para adoptar este sistema como forma de vida.
Mejora
El quinto paso, que completa el sistema "5S" en producción, se basa en el concepto de kaizen. Significa que todos los empleados, independientemente de su puesto, deben esforzarse por mejorar el proceso de trabajo en el área que se les ha encomendado. La esencia filosófica del kaizen es que nuestra vida entera mejora cada día, y como el trabajo es parte de la vida, tampoco debe permanecer al margen de las mejoras.
El campo de actividad aquí es amplio, porque la perfección no tiene límites. Según los conceptos de los japoneses, los propios trabajadores deberían querer mejorar su proceso de producción, sin instrucciones ni coacción. Ahora, muchas organizaciones están formando equipos de trabajadores que monitorean la calidad del producto, enseñan su experiencia positiva a otros y ayudan a lograr la excelencia.
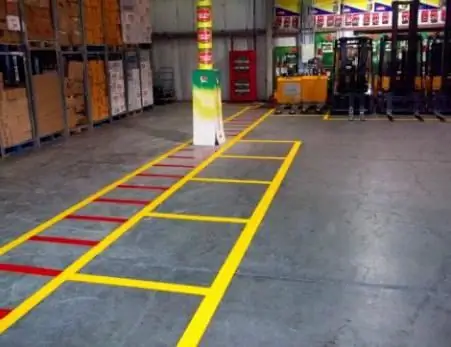
Errores básicos
Para que el sistema "5C" comience a funcionar, no basta con organizarlo o contratar empleados que obliguen a sus compañeros a implementarlo. Es importante que las personas se den cuenta de la utilidad de esta innovación y la acepten como un estilo de vida. La introducción del sistema "5S" en Rusia en producción enfrenta dificultades precisamente porque nuestra mentalidad rusa es diferente de la japonesa. Muchas de nuestras producciones se caracterizan por lo siguiente:
1. Los empleados, especialmente si no hay incentivos para ellos, no buscan aumentar las ganancias de la empresa. Ellos estan preguntando,¿Por qué intentar enriquecer aún más al jefe si ya lo tiene todo?
2. Los propios líderes no están interesados en la introducción del sistema "5S", porque no ven la conveniencia en ello.
3. Muchas directivas "abajo desde arriba" se acostumbran a llevar a cabo solo por "tick". En Japón, hay una actitud completamente diferente hacia su trabajo. Por ejemplo, el mismo Taiichi Ohno, al presentar el sistema "5S", no pensó en el beneficio personal, sino en el beneficio de la empresa en la que solo era un ingeniero.
4. En muchas empresas, el sistema 5S se está introduciendo a la fuerza. La producción ajustada, que implica la eliminación de pérdidas de todo tipo (tiempo de trabajo, materias primas, buenos empleados, motivación y otros indicadores), no funciona, ya que los trabajadores comienzan a resistirse a las innovaciones a nivel subconsciente, lo que finalmente reduce todos los esfuerzos a cero..
5. Los gerentes que implementan el sistema no comprenden completamente su esencia, lo que provoca fallas en los procesos de producción establecidos.
6. La estandarización a menudo se convierte en burocracia, una buena acción está cubierta de instrucciones y directivas que solo interfieren con el trabajo.
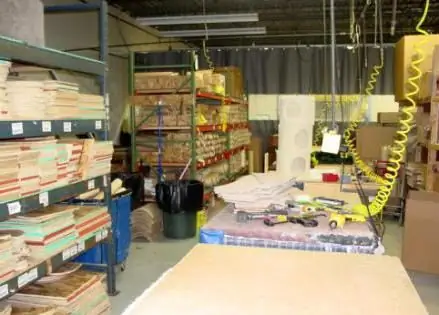
Reseñas
Los rusos que han introducido el sistema "5S" en la producción, los comentarios sobre esta innovación son muy ambiguos. Ventajas destacadas:
- mejor estar en el lugar de trabajo;
- no distraigas del trabajo con pequeñas cosas innecesarias;
- flujo de trabajo más claro;
- la fatiga disminuyó al final del turno;
- ligeramente aumentadosalario aumentando la productividad laboral;
- Disminución de lesiones laborales.
Contras notadas:
- al clasificar obligan a tirar todo;
- la normalización ha llevado a un aumento de la burocracia;
- La introducción del sistema "5C" no ha exacerbado los problemas en todas las áreas de la empresa;
- Poner el sistema 5S en primer lugar ha eclipsado cuestiones importantes como la f alta de repuestos.
Recomendado:
Sistema "Rapida": descripción, características y reseñas
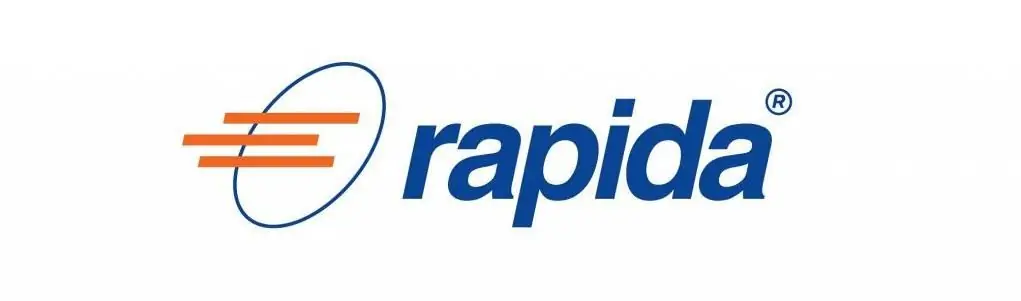
El sistema de pago "Rapida" es un servicio universal. Sus servicios son adecuados tanto para usuarios comunes como para propietarios de negocios. Considere las características de la plataforma y cómo se lleva a cabo el procedimiento para registrar e identificar a los clientes
Gestión centralizada: sistema, estructura y funciones. Principios del modelo de gestión, pros y contras del sistema
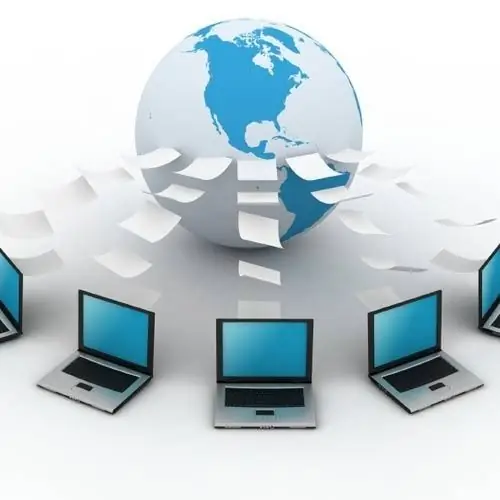
¿Qué modelo de gestión es mejor, centralizado o descentralizado? Si alguien en respuesta señala a uno de ellos, está poco versado en la gestión. Porque no hay modelos malos y buenos en la gestión. Todo depende del contexto y de su competente análisis, que te permita elegir la mejor forma de gestionar la empresa aquí y ahora. La gestión centralizada es un gran ejemplo de esto
Producción moderna. La estructura de la producción moderna. Problemas de la producción moderna

Una industria desarrollada y un alto nivel de la economía del país son factores clave que influyen en la riqueza y el bienestar de su gente. Tal estado tiene grandes oportunidades económicas y potencial. Un componente significativo de la economía de muchos países es la producción
Producción de gas. Métodos de producción de gas. Producción de gas en Rusia
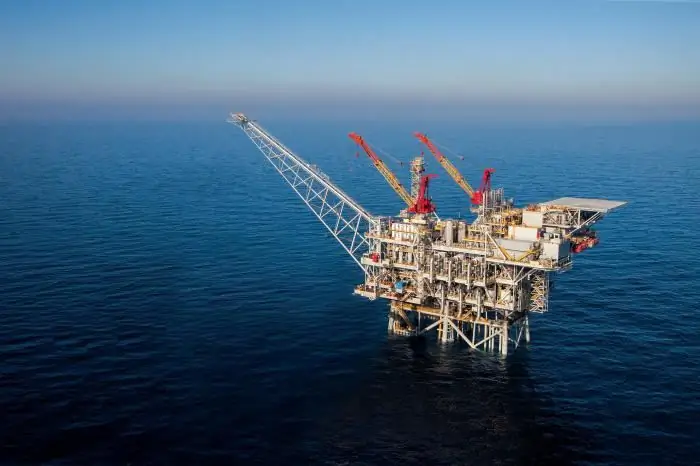
El gas natural se forma mezclando varios gases en la corteza terrestre. En la mayoría de los casos, la profundidad de ocurrencia varía desde varios cientos de metros hasta un par de kilómetros. Vale la pena señalar que el gas se puede formar a altas temperaturas y presiones. En este caso, no hay acceso de oxígeno al lugar. Hasta la fecha, la producción de gas se ha implementado de varias maneras, cada una de las cuales consideraremos en este artículo. Pero hablemos de todo en orden
"Kanban", sistema de producción: descripción, esencia, funciones y reseñas
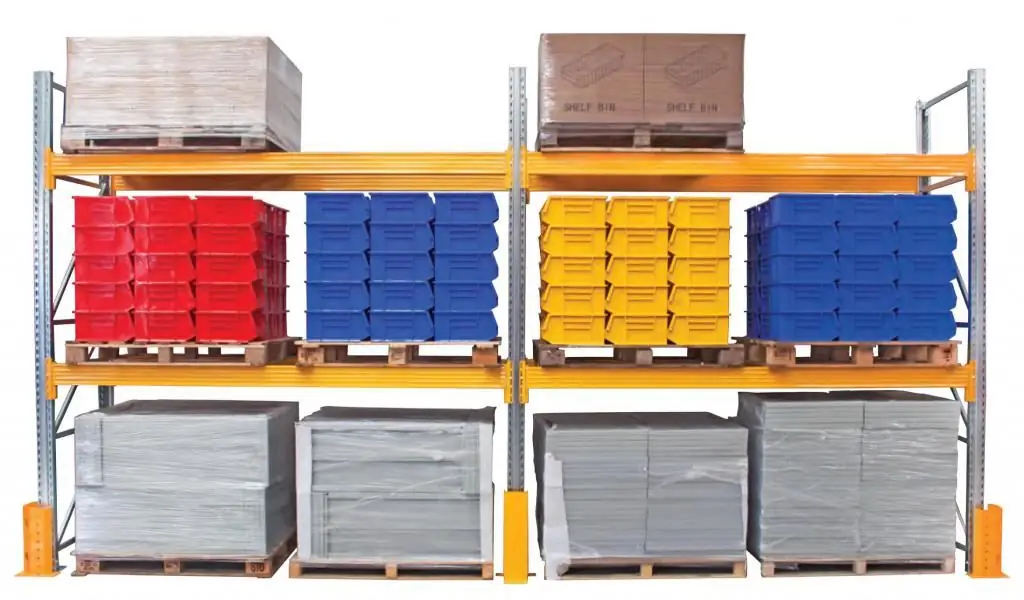
Kanban es el método de gestión de la producción industrial más conocido dentro del concepto Just-in-Time. Con costes de organización mínimos, puede reducir significativamente el tiempo de trabajo y el coste de los recursos materiales