2025 Autor: Howard Calhoun | [email protected]. Última modificación: 2025-01-24 13:15
La metrología es la ciencia de las medidas, los medios y métodos para asegurar su unidad, así como las formas de lograr la precisión requerida. Su objeto es la selección de información cuantitativa sobre los parámetros de los objetos con una determinada fiabilidad y precisión. El marco regulatorio de la metrología son las normas. En este artículo, consideraremos el sistema de tolerancias y aterrizajes, que es una subsección de esta ciencia.
El concepto de intercambiabilidad de piezas
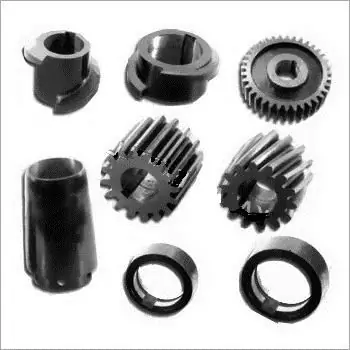
En las fábricas modernas, los tractores, automóviles, máquinas herramienta y otras máquinas no se producen por unidades o decenas, sino por cientos e incluso miles. Con tales volúmenes de producción, es muy importante que cada pieza o conjunto fabricado encaje exactamente en su lugar durante el montaje sin ajustes adicionales de cerrajería. Después de todo, tales operaciones son bastante laboriosas, costosas y requieren mucho tiempo, lo que no es aceptable en la producción en masa. Es igualmente importante que las piezas que ingresan al ensamblaje permitan el reemplazo.a otros fines comunes con ellos, sin perjuicio del funcionamiento de toda la unidad acabada. Esta intercambiabilidad de piezas, ensamblajes y mecanismos se denomina unificación. Este es un punto muy importante en la ingeniería mecánica, permite ahorrar no solo el costo de diseño y fabricación de piezas, sino también el tiempo de producción, además, simplifica la reparación del producto como resultado de su funcionamiento. La intercambiabilidad es la propiedad de los componentes y mecanismos para ocupar su lugar en los productos sin selección previa y realizar sus funciones principales de acuerdo con las especificaciones.
Piezas acopladas
Dos partes, fijas o conectadas de forma móvil entre sí, se denominan acoplamiento. Y el valor por el que se lleva a cabo esta articulación suele denominarse tamaño de apareamiento. Un ejemplo es el diámetro del agujero en la polea y el diámetro del eje correspondiente. El valor por el cual la conexión no ocurre generalmente se denomina tamaño libre. Por ejemplo, el diámetro exterior de la polea. Para garantizar la intercambiabilidad, las dimensiones de acoplamiento de las piezas siempre deben ser precisas. Sin embargo, tal procesamiento es muy complicado ya menudo poco práctico. Por ello, en tecnología se utiliza un método para obtener piezas intercambiables cuando se trabaja con la llamada precisión aproximada. Se encuentra en el hecho de que para diferentes condiciones de operación, los nodos y las partes establecen las desviaciones permitidas de sus tamaños, bajo las cuales es posible el funcionamiento impecable de estas partes en la unidad. Tales compensaciones, calculadas para una variedad de condiciones de operación, se construyen en un determinadoun cierto esquema, su nombre es "un sistema unificado de tolerancias y aterrizajes".
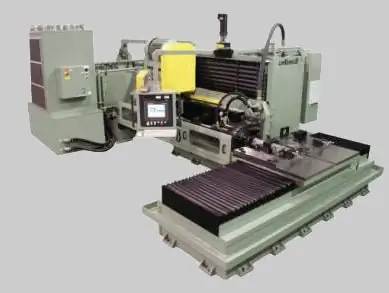
El concepto de tolerancias. Cantidad características
Los datos calculados de la pieza suministrada en el dibujo, a partir de los cuales se cuentan las desviaciones, se denomina comúnmente tamaño nominal. Por lo general, este valor se expresa en milímetros enteros. El tamaño de la pieza, que realmente se obtiene durante el procesamiento, se denomina tamaño real. Los valores entre los que fluctúa este parámetro suelen denominarse límite. De estos, el parámetro máximo es el límite de tamaño más grande y el parámetro mínimo es el más pequeño. Las desviaciones son la diferencia entre el valor nominal y el límite de una pieza. En los dibujos, este parámetro generalmente se indica en forma numérica en un tamaño nominal (el valor superior se indica arriba y el valor inferior a continuación).
Ejemplo de entrada
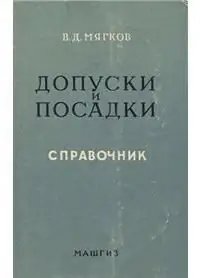
Si el dibujo muestra el valor 40+0, 15-0, 1, entonces esto significa que el tamaño nominal del la parte es de 40 mm, el límite más grande es +0.15, el más pequeño es -0.1 La diferencia entre el valor límite nominal y máximo se denomina desviación superior, y entre el mínimo, la inferior. A partir de aquí, los valores reales se determinan fácilmente. De este ejemplo se deduce que el valor límite mayor será igual a 40+0, 15=40,15 mm, y el menor: 40-0, 1=39,9 mm. La diferencia entre los tamaños límite más pequeños y más grandes se denomina tolerancia. Calculado de la siguiente manera: 40, 15-39, 9=0,25 mm.
Huecos y estanqueidad
Consideremosun ejemplo específico donde las tolerancias y los ajustes son clave. Supongamos que necesitamos una pieza con un agujero 40+0, 1 para encajar en un eje de dimensiones 40-0, 1 -0, 2. Se puede ver en la condición de que el diámetro para todas las opciones será menor que el orificio, lo que significa que con tal conexión necesariamente se producirá un espacio. Tal aterrizaje generalmente se denomina móvil, ya que el eje girará libremente en el orificio. Si el tamaño de la pieza es 40+0, 2+0, 15, entonces, bajo cualquier condición, será mayor que el diámetro del orificio. En este caso, el eje debe presionarse y habrá una interferencia en la conexión.
Conclusiones
Con base en los ejemplos anteriores, se pueden sacar las siguientes conclusiones:
- Gap es la diferencia entre las dimensiones reales del eje y del agujero, cuando este último es mayor que el primero. Con esta conexión, las piezas tienen rotación libre.
- Se suele denominar precarga a la diferencia entre las dimensiones reales del agujero y del eje, cuando esta última es mayor que la primera. Con esta conexión, las piezas se presionan.
Ajustes y clases de precisión
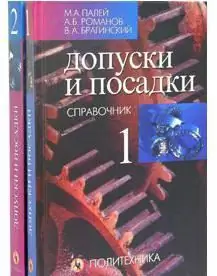
Los aterrizajes generalmente se dividen en fijos (caliente, presión, presión fácil, sordo, apretado, denso, tenso) y móviles (deslizamiento, carrera, movimiento, carrera fácil, carrera ancha). En ingeniería mecánica e instrumentación, existen ciertas reglas que regulan las tolerancias y los aterrizajes. GOST proporciona ciertas clases de precisión en la fabricación de ensamblajes utilizando desviaciones dimensionales específicas. De la prácticaSe sabe que los detalles de las máquinas agrícolas y de carreteras sin dañar su funcionamiento pueden fabricarse con menos precisión que para tornos, instrumentos de medición y automóviles. En este sentido, las tolerancias y los ajustes en ingeniería mecánica tienen diez clases de precisión diferentes. Los más precisos de ellos son los primeros cinco: 1, 2, 2a, 3, 3a; los dos siguientes se refieren a precisión media: 4 y 5; y los tres últimos a bruto: 7, 8 y 9.
Para saber con qué clase de precisión se debe hacer la pieza, en el dibujo, junto a la letra que indica el ajuste, coloque un número que indique este parámetro. Por ejemplo, marcar C4 significa que el tipo es deslizante, clase 4; X3 - tipo corriente, clase 3ra. Para todos los aterrizajes de segunda clase, no se pone una designación digital, ya que es la más común. Puede obtener información detallada sobre este parámetro en el libro de referencia de dos volúmenes "Tolerancias y ajustes" (Myagkov V. D., edición de 1982).
Sistema de eje y orificio
La tolerancia y los ajustes se suelen considerar como dos sistemas: agujeros y ejes. El primero de ellos se caracteriza por el hecho de que en él todos los tipos con el mismo grado de precisión y clase se refieren al mismo diámetro nominal. Los agujeros tienen valores constantes de desviaciones límite. Se obtiene una variedad de aterrizajes en dicho sistema como resultado de cambiar la desviación máxima del eje.
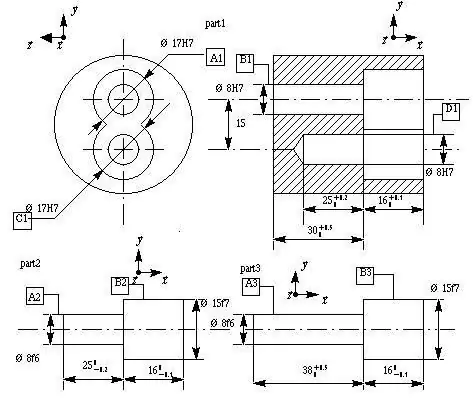
El segundo de ellos se caracteriza porque todos los tipos con el mismo grado de precisión y clase se refieren al mismo diámetro nominal. El eje tiene valores límite constantes.desviaciones Se lleva a cabo una variedad de aterrizajes como resultado de cambiar los valores de las desviaciones máximas de los agujeros. En los dibujos del sistema de orificios, se acostumbra designar la letra A y el eje, la letra B. Cerca de la letra, se coloca el signo de la clase de precisión.
Ejemplos de símbolos
Si en el dibujo se indica "30A3", significa que la pieza en cuestión debe ser maquinada con un sistema de agujeros de tercera clase de precisión, si se indica "30A", significa que se utiliza el mismo sistema, pero la segunda clase. Si la tolerancia y el ajuste se realizan de acuerdo con el principio del eje, entonces el tipo requerido se indica en el tamaño nominal. Por ejemplo, una pieza con la designación "30B3" corresponde al procesamiento del sistema de eje de la tercera clase de precisión.
En su libro, M. A. Paley ("Tolerancias y ajustes") explica que en ingeniería mecánica el principio de un agujero se usa con más frecuencia que el de un eje. Esto se debe al hecho de que requiere menos equipo y herramientas. Por ejemplo, para procesar un agujero de un diámetro nominal dado según este sistema, solo se necesita un escariador para todos los descansos de esta clase, y se necesita un tapón de límite para cambiar el diámetro. Con un sistema de eje, se requiere un escariador y un tapón separados para asegurar que cada uno encaje dentro de la misma clase.
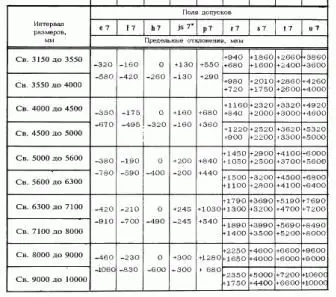
Tolerancias y ajustes: tabla de desviaciones
Para determinar y seleccionar las clases de precisión, se acostumbra utilizar literatura de referencia especial. Por lo tanto, las tolerancias y los ajustes (en este artículo se proporciona una tabla con un ejemplo) son, por regla general, valores muy pequeños. Parapara no escribir ceros extra, en la literatura se designan en micras (milésimas de milímetro). Una micra corresponde a 0,001 mm. Por lo general, los diámetros nominales se indican en la primera columna de dicha tabla y las desviaciones del orificio se indican en la segunda. El resto de los gráficos dan diferentes tamaños de aterrizajes con sus correspondientes desviaciones. El signo más al lado de dicho valor indica que debe agregarse al tamaño nominal, el signo menos indica que debe restarse.
Historias
La tolerancia y los ajustes de las conexiones roscadas deben tener en cuenta el hecho de que las roscas se acoplan solo en los lados del perfil, solo los tipos herméticos al vapor pueden ser una excepción. Por tanto, el principal parámetro que determina la naturaleza de las desviaciones es el diámetro medio. La tolerancia y los ajustes para los diámetros exterior e interior se establecen de manera que se elimine por completo la posibilidad de pellizcos a lo largo de los canales y la parte superior de la rosca. Los errores de reducir la dimensión exterior y aumentar la dimensión interior no afectarán el proceso de maquillaje. Sin embargo, las desviaciones en el paso de la rosca y el ángulo del perfil harán que el sujetador se atasque.
Tolerancias de rosca de espacio
Los ajustes de tolerancia y holgura son los más comunes. En tales conexiones, el valor nominal del diámetro medio es igual al valor medio más grande de la rosca de la tuerca. Las desviaciones generalmente se cuentan desde la línea del perfil perpendicular al eje de la rosca. Esto está determinado por GOST 16093-81. Las tolerancias para el diámetro de la rosca de tuercas y pernos se asignan según el grado de precisión especificado (indicado por un número). Aceptadola siguiente serie de valores para este parámetro: q1=4, 6, 8; d2=4, 6, 7, 8; D1=4, 6, 7, 8; D2=4, 5, 6, 7. No se establecen tolerancias para ellos. La colocación de los campos de diámetro de rosca en relación con el valor nominal del perfil ayuda a determinar las principales desviaciones: las superiores para los valores externos de los pernos y las inferiores para los valores internos de las tuercas. Estos parámetros dependen directamente de la precisión y el paso de conexión.
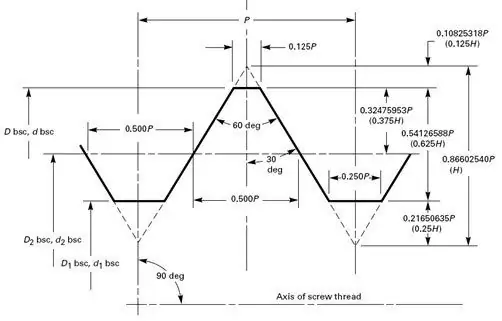
Tolerancias, ajustes y medidas técnicas
Para la producción y procesamiento de piezas y mecanismos con parámetros específicos, el tornero tiene que usar una variedad de herramientas de medición. Por lo general, para mediciones aproximadas y verificación de las dimensiones de los productos, se utilizan reglas, calibradores y calibres internos. Para mediciones más precisas: calibradores, micrómetros, calibres, etc. Todo el mundo sabe qué es una regla, por lo que no nos detendremos en ella.
El calibrador es una herramienta sencilla para medir las dimensiones exteriores de las piezas de trabajo. Consiste en un par de patas curvas giratorias fijadas en el mismo eje. También hay un tipo de pinza de resorte, se ajusta al tamaño requerido con un tornillo y una tuerca. Tal herramienta es un poco más conveniente que una simple, porque retiene el valor especificado.
El calibrador está diseñado para tomar medidas internas. Hay un tipo regular y de primavera. El dispositivo de esta herramienta es similar a un calibrador. La precisión del instrumento es de 0,25 mm.
Un calibrador es un dispositivo más preciso. Pueden medir tanto superficies externas como internas.piezas procesadas. El tornero, cuando trabaja en un torno, usa un calibrador para medir la profundidad de una ranura o repisa. Esta herramienta de medición consta de un eje con graduaciones y mordazas y un marco con un segundo par de mordazas. Con la ayuda de un tornillo, el marco se fija en la barra en la posición requerida. La precisión de la medición es de 0,02 mm.
Medidor de profundidad: este dispositivo está diseñado para medir la profundidad de ranuras y socavaduras. Además, la herramienta le permite determinar la posición correcta de los salientes a lo largo del eje. El dispositivo de este dispositivo es similar a un calibrador.
Los micrómetros se utilizan para determinar con precisión el diámetro, el grosor y la longitud de la pieza de trabajo. Dan lecturas con una precisión de 0,01 mm. El objeto medido se encuentra entre el tornillo micrométrico y el talón fijo, el ajuste se realiza girando el tambor.
Los calibres interiores se utilizan para mediciones precisas de las superficies internas. Hay dispositivos fijos y deslizantes. Estas herramientas son varillas con extremos esféricos de medición. La distancia entre ellos corresponde al diámetro del agujero que se está determinando. Los límites de medida para el calibre interior son 54-63 mm, con un cabezal adicional se pueden determinar diámetros hasta 1500 mm.
Recomendado:
Mujer ingeniera. Profesiones de ingeniería de las mujeres
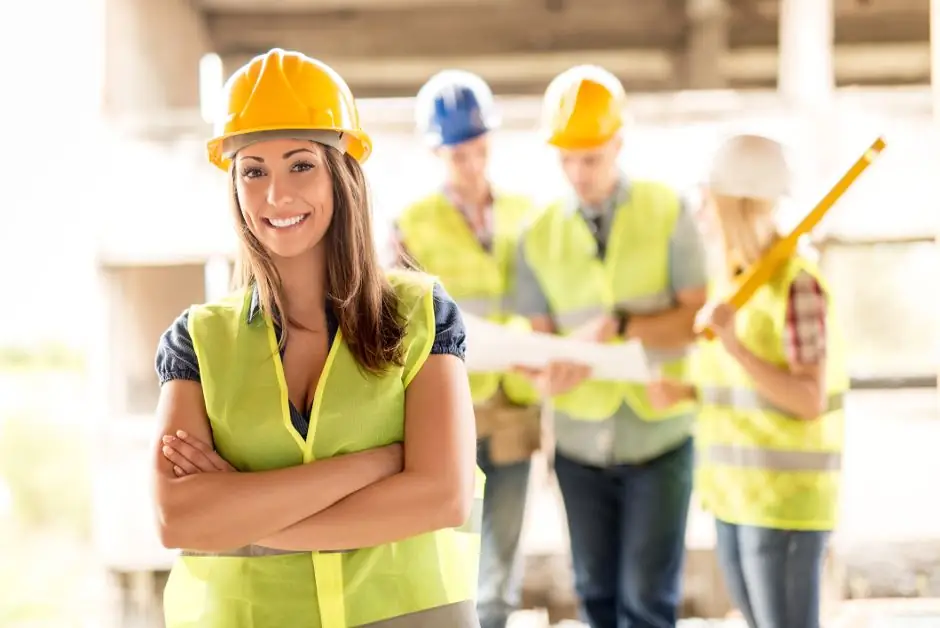
Atendiendo al mercado laboral, es fácil ver que en los últimos años ha habido una demanda de especialidades técnicas. El trabajo de diseño complejo, la planificación y el diseño atraen hoy no solo al sexo fuerte. ¿Qué atrae a las damas a tales especialidades y cómo entender que en una naturaleza refinada hay un deseo por un campo técnico?
Procesos tecnológicos en ingeniería mecánica. Sistemas de control de procesos automatizados
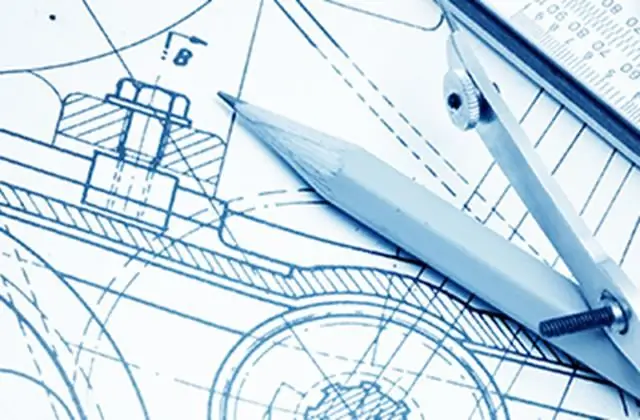
El proceso tecnológico es la base de cualquier operación productiva. Incluye un conjunto de procedimientos llevados a cabo en una secuencia determinada, cuya acción está dirigida a cambiar la forma, el tamaño y las propiedades del producto fabricado. Los principales ejemplos de procesos tecnológicos son el procesamiento mecánico, térmico, de compresión, así como el ensamblaje, el empaque, el tratamiento a presión y mucho más
¡La ingeniería mecánica es una profesión escasa en el mercado laboral
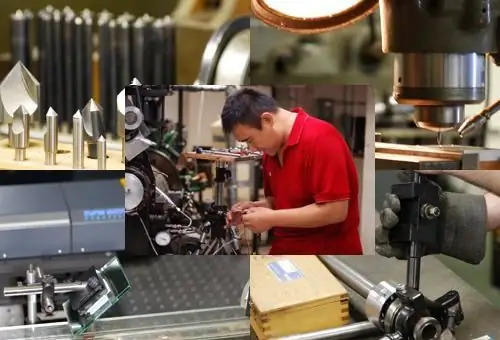
Hoy en día, la profesión de ingeniero mecánico es bastante común en el mercado laboral. A pesar de la graduación anual de ingenieros de las universidades, es muy difícil encontrar un especialista calificado y competente
Tipos de hilos utilizados en ingeniería mecánica
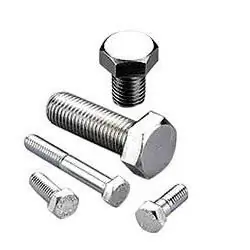
Un hilo es una espiral adornada con un paso constante aplicada a una superficie cónica o cilíndrica. Es el elemento principal para conectar dos tipos de sujetadores. Hasta la fecha, para aplicaciones generales de construcción de maquinaria, las principales roscas externas e internas son métricas
Tecnología de la ingeniería mecánica: información sobre la especialidad
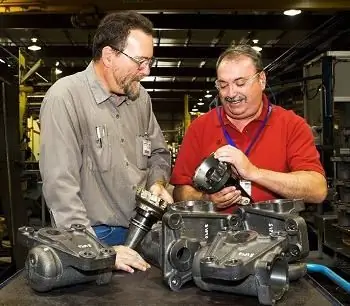
La tecnología de ingeniería es una especialidad que sigue teniendo demanda: cada año al menos 4 personas solicitan una plaza presupuestaria