2025 Autor: Howard Calhoun | [email protected]. Última modificación: 2025-01-24 13:15
En los procesos de obtención de aceros de alta resistencia, las operaciones de aleación y modificación de la composición base juegan un papel importante. La base de tales procedimientos es la técnica de adición de impurezas metálicas de varias propiedades, pero la regulación gas-aire también es de no poca importancia. Es a esta operación tecnológica a la que se orienta el funcionamiento del convertidor de oxígeno, que es ampliamente utilizado en metalurgia en la producción de aleaciones de acero en grandes volúmenes.
Diseño del convertidor
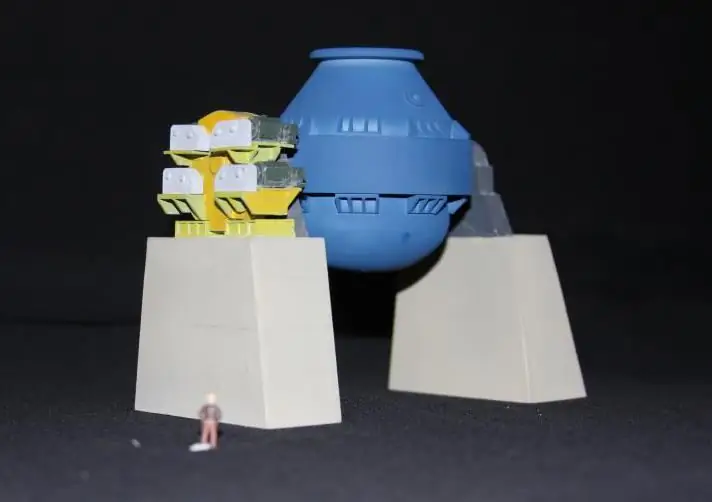
El equipo es un recipiente en forma de pera, provisto de un revestimiento interior y un orificio de grifo para la liberación de productos de fundición. En la parte superior de la estructura se proporciona una abertura con cuello para el suministro de lanza, chatarra, hierro fundido, mezclas de aleaciones y eliminación de gases. El tonelaje varía de 50 a 400 Tn. Como materiales para la fabricación de la estructura se utiliza chapa o acero medio soldado.unos 50-70 mm de espesor. Un dispositivo convertidor de oxígeno típico brinda la posibilidad de separar el fondo; estas son modificaciones con purga de fondo con mezclas de gas y aire. Entre los elementos auxiliares y funcionales de la unidad, se pueden destacar un motor eléctrico, una infraestructura de tuberías para la circulación de flujos de oxígeno, cojinetes de empuje, una plataforma amortiguadora y un marco de soporte para el montaje de la estructura.
Anillos de soporte y muñón
El convertidor se encuentra sobre cojinetes de rodillos, que se fijan en el bastidor. El diseño puede ser estacionario, pero esto es raro. Por lo general, en las etapas de diseño, se determina la posibilidad de transportar o mover la unidad en ciertas condiciones. Es por estas funciones que el equipo en forma de anillos de soporte y pasadores es responsable. El grupo de rodamientos brinda la posibilidad de torsión del equipo alrededor del eje de los muñones. Los modelos anteriores de convertidores asumieron la combinación del equipo portador y el cuerpo del equipo de fusión, pero debido a la exposición a altas temperaturas y la deformación de los materiales auxiliares, esta solución de diseño fue reemplazada por un esquema de interacción más complejo, pero confiable y duradero entre la unidad funcional y el recipiente.
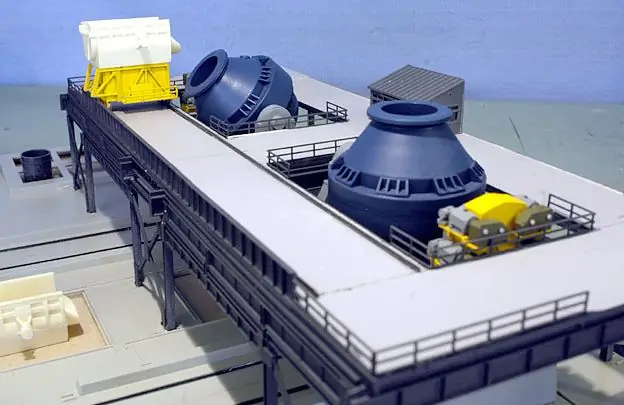
El convertidor de oxígeno moderno, en particular, cuenta con un anillo de soporte separado, en cuya estructura también se introducen muñones y una carcasa fija. El desfase tecnológico entre la carcasa y la base de apoyo evita los efectos negativos de la temperatura en los elementos sensibles de las suspensiones y mecanismos móviles. El sistema de fijación del propio convertidor se implementa mediante topes. El propio anillo de soporte es un portador, formado por dos medios anillos y placas de muñón fijadas en los puntos de acoplamiento.
Mecanismo giratorio
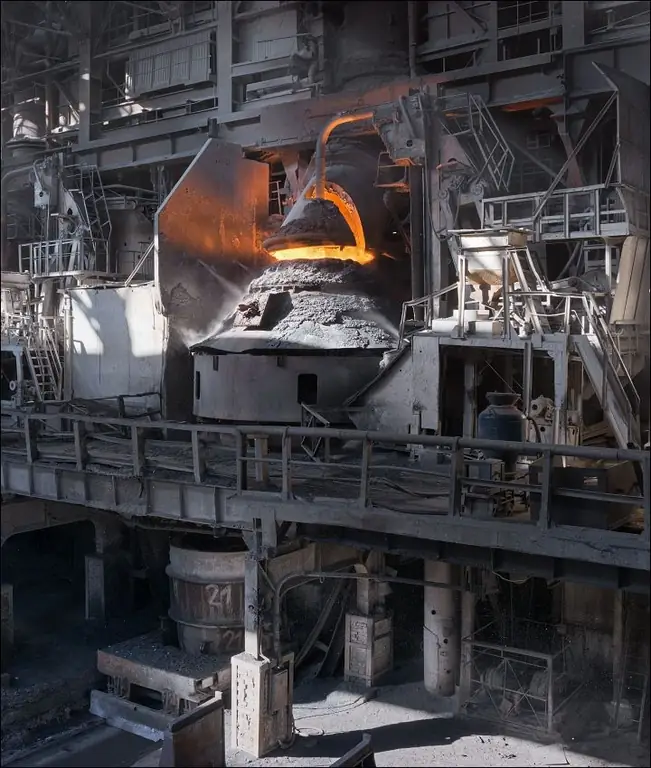
El accionamiento eléctrico permite que el convertidor gire 360°. La velocidad de rotación media es de 0,1-1 m/min. Por sí misma, esta función no siempre es necesaria, según la organización de las operaciones tecnológicas durante el flujo de trabajo. Por ejemplo, puede ser necesario un giro para orientar el cuello directamente al punto de suministro de chatarra, fundición de hierro, drenaje de acero, etc. La funcionalidad del mecanismo de giro puede ser diferente. Hay sistemas unidireccionales y bidireccionales. Por regla general, los convertidores de oxígeno con una capacidad de carga de hasta 200 toneladas asumen un giro en una sola dirección. Esto se debe al hecho de que en tales diseños se requiere menos torsión al inclinar el cuello. Para eliminar el consumo de exceso de energía durante la operación de equipos pesados, está provisto de un mecanismo de rotación bidireccional, que compensa el costo de manipular el cuello. La estructura del sistema de torsión incluye una caja de cambios, un motor eléctrico y un husillo. Esta es la disposición tradicional de un accionamiento estacionario montado sobre una regla de hormigón. Los mecanismos articulados más tecnológicos están fijados en el muñón y accionados por un engranaje conducido con un sistema de rodamientos, que también son accionados por motores eléctricos a través de un sistema de ejes.
Dimensiones del convertidor
Durante el diseño, los parámetros de diseño deben calcularse en función del volumen aproximado de purga que se producirá, excluyendo la eyección de material fundido. En los últimos años se han desarrollado unidades que aceptan materiales en volúmenes de 1 a 0,85 m3/t. También se calcula la pendiente de la garganta, cuyo ángulo promedia de 20° a 35°. Sin embargo, la práctica de operar tales instalaciones muestra que exceder la pendiente de 26° degrada la calidad del revestimiento. En profundidad, las dimensiones del convertidor son de 1-2 m, pero a medida que aumenta la capacidad de carga, la altura de la estructura también puede aumentar. Los convertidores convencionales de hasta 1 m de profundidad pueden aceptar una carga de no más de 50 toneladas. En cuanto al diámetro, varía en promedio de 4 a 7 m. El espesor del cuello es de 2-2,5 m.
Forro BOF
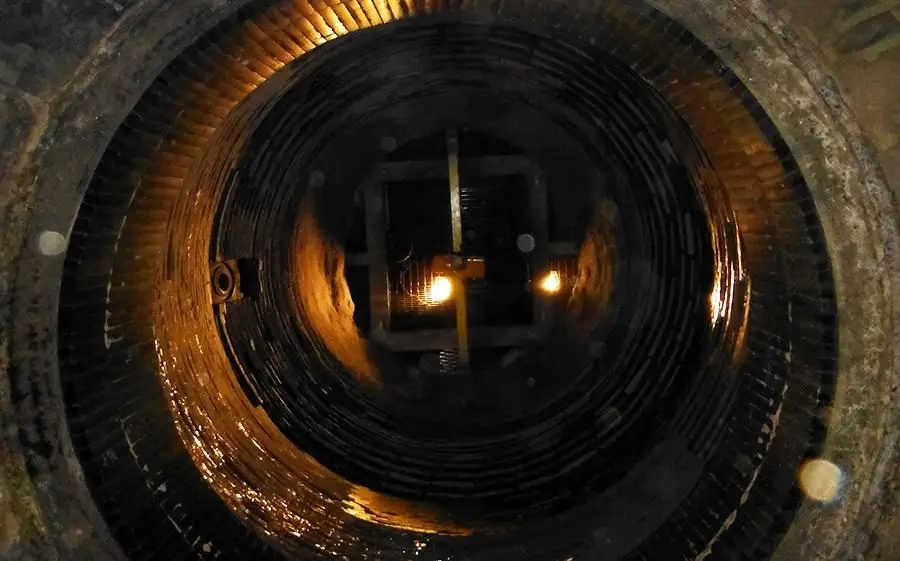
Procedimiento tecnológico obligatorio, durante el cual las paredes internas del convertidor se dotan de una capa protectora. Al mismo tiempo, debe tenerse en cuenta que, a diferencia de la mayoría de los hornos metalúrgicos, este diseño está sujeto a cargas térmicas mucho más altas, lo que también determina las características del revestimiento. Este es un procedimiento que implica la colocación de dos capas protectoras: funcional y de refuerzo. Una capa de refuerzo protector con un espesor de 100-250 mm se encuentra directamente adyacente a la superficie del cuerpo. Su tarea es reducir la pérdida de calor y evitar el desgaste de la capa superior. El material utilizado es magnesita o ladrillo de magnesita-cromita, que puede servir durante años sin renovación.
La capa de trabajo superior tiene un grosor de aproximadamente 500-700 mm y se reemplaza con bastante frecuencia a medida que se desgasta. En esta etapa, el BOF se trata con compuestos refractarios aglomerados con resina o arena que no se disparan. El material base para esta capa de revestimiento es dolomita con aditivos de magnesita. El cálculo de carga estándar se basa en un efecto de temperatura de aproximadamente 100-500 °C.
Revestimiento de hormigón proyectado
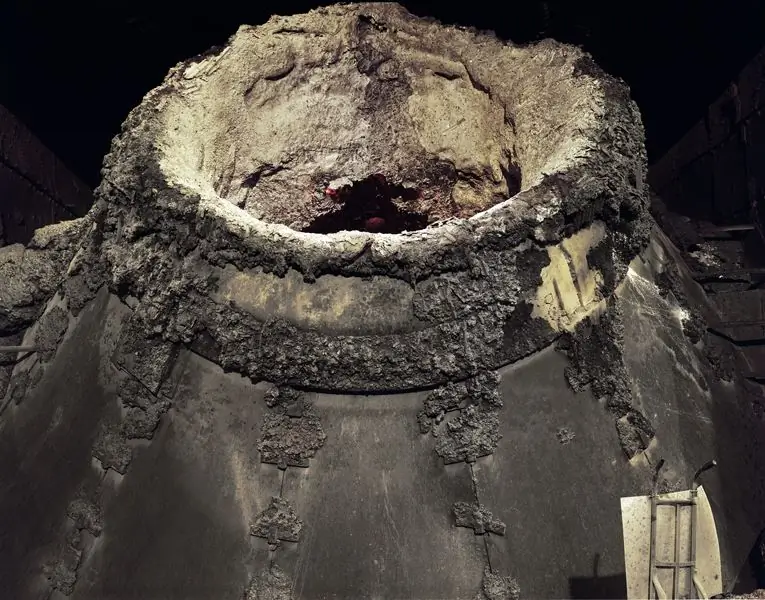
Bajo influencias químicas y de temperatura agresivas, las superficies internas de la estructura del convertidor pierden rápidamente sus cualidades; nuevamente, esto se refiere al desgaste externo de la capa de trabajo de protección térmica. El revestimiento de hormigón proyectado se utiliza como una operación de reparación. Esta es una tecnología de reducción en caliente en la que se coloca una composición refractaria con la ayuda de un equipo especial. No se aplica de forma continua, sino puntualmente en áreas muy desgastadas del revestimiento de la base. El procedimiento se realiza en máquinas especiales de hormigón proyectado que alimentan una lanza refrigerada por agua con una masa de polvo de coque y polvo de magnesita en la zona dañada.
Tecnologías de fundición
Tradicionalmente, existen dos enfoques para la implementación de la fusión del convertidor de oxígeno: Bessemer y Thomas. Sin embargo, los métodos modernos se diferencian de ellos por el bajo contenido de nitrógeno en el horno, lo que mejora la calidad del proceso de trabajo. La tecnología se está llevando a cabo en las siguientes etapas:
- Cargando chatarra. Alrededor del 25-27% de la masa total de la carga se carga en el convertidor inclinado por medio de cucharas.
- Rellenohierro fundido o aleación de acero. El metal líquido a temperaturas de hasta 1450 °C se vierte en un convertidor inclinado mediante cucharones. La operación no dura más de 3 minutos.
- Purga. En esta parte, la tecnología de siderurgia en convertidores de oxígeno permite diferentes enfoques en cuanto al suministro de una mezcla gas-aire. El flujo se puede dirigir desde arriba, abajo, abajo y de forma combinada, según el tipo de diseño del equipo.
- Recepción de muestras. Se mide la temperatura, se eliminan las impurezas no deseadas y se espera el análisis de la composición. Si sus resultados cumplen con los requisitos de diseño, se libera la masa fundida y, de lo contrario, se realizan ajustes.
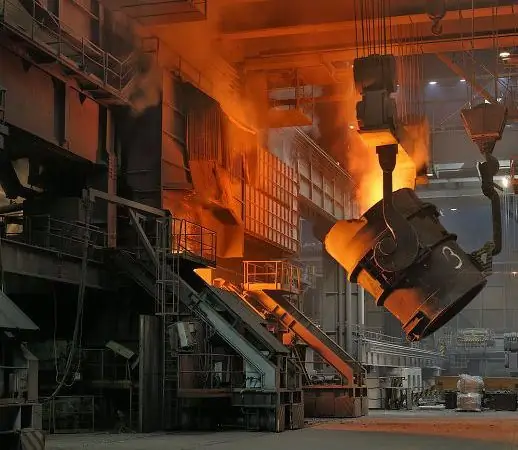
Pros y contras de la tecnología
El método es valorado por su alta productividad, esquemas simples de suministro de oxígeno, confiabilidad estructural y costos relativamente bajos en general para la organización del proceso. En cuanto a las desventajas, éstas, en particular, incluyen restricciones en cuanto a la adición de lodos y reciclables. La misma chatarra con otras inclusiones no puede ser más del 10%, y esto no permite modificar la estructura de la fundición en la medida requerida. Además, soplar consume una gran cantidad de hierro útil.
Aplicación de tecnología
La combinación de ventajas y desventajas determinó en última instancia la naturaleza del uso de convertidores. En particular, las plantas metalúrgicas producen acero de baja aleación, al carbono y aleado de alta calidad, suficiente para el uso del material en la industria pesada y la construcción. Recepción de aceros enEl convertidor de oxígeno está aleado y mejora las propiedades individuales, lo que amplía el alcance del producto final. A partir de las materias primas resultantes se fabrican tuberías, alambres, rieles, herrajes, herrajes, etc. La tecnología también se usa ampliamente en la metalurgia no ferrosa, donde se obtiene cobre blister con suficiente soplado.
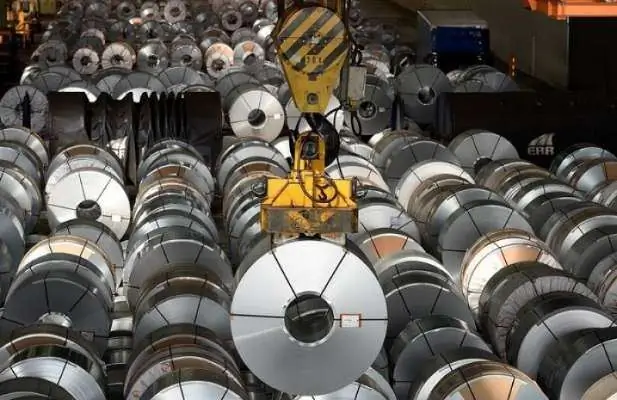
Conclusión
La fundición en instalaciones convertidoras se considera una técnica moralmente obsoleta, pero se sigue utilizando debido a la combinación óptima de productividad y costes económicos del proceso. En gran medida, la demanda de tecnología también se ve facilitada por las ventajas estructurales de los equipos utilizados. La misma posibilidad de carga directa de chatarra, carga, lodos y otros residuos, aunque de forma limitada, amplía las posibilidades de modificación de la aleación. Otra cosa es que para la operación completa de convertidores de gran tamaño con la capacidad de girar, se requiere la organización de una sala adecuada en la empresa. Por lo tanto, la fundición con purga de oxígeno en grandes volúmenes es realizada principalmente por grandes empresas.
Recomendado:
Manguito de oxígeno: descripción, GOST, tipos y diámetro
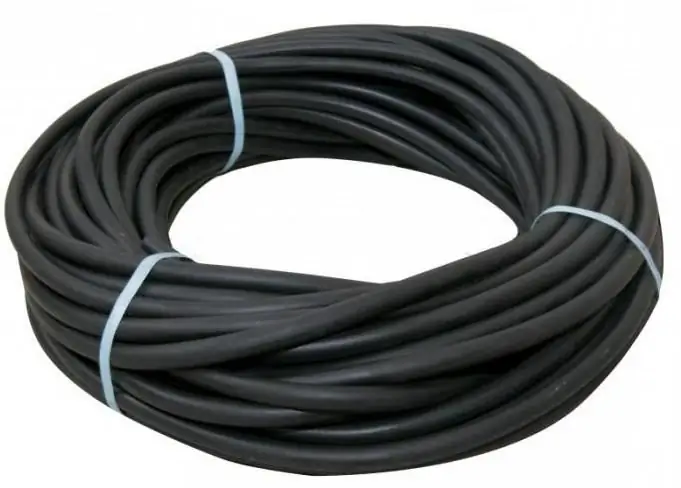
Actualmente, las personas están utilizando activamente varios gases u oxígeno para sus propios fines. Dado que es necesario transportar una sustancia gaseosa en un ambiente completamente sellado, se han desarrollado mangueras, que se denominan mangueras de oxígeno
Botellas de oxígeno. El repostaje adecuado es la clave para la salud y la seguridad
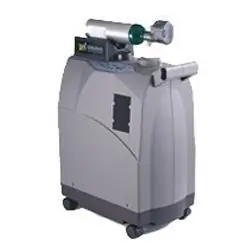
Una de las preparaciones más importantes y peligrosas para el buceo es el correcto llenado de las botellas de oxígeno. El artículo explica cómo llenar correctamente los cilindros de oxígeno y por qué hay casos de explosión de cilindros de oxígeno
Mangueras de oxígeno: descripción, dimensiones, GOST y comentarios
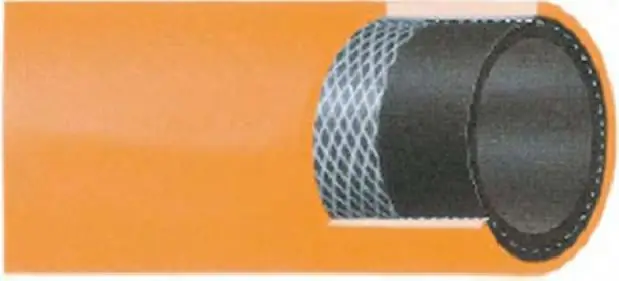
Actualmente, muchos trabajos se realizan mediante soldadura. Por esta razón, las mangueras de oxígeno se han convertido en un material bastante popular y también son fáciles de transportar
Convertidor de soldadura: principio de funcionamiento
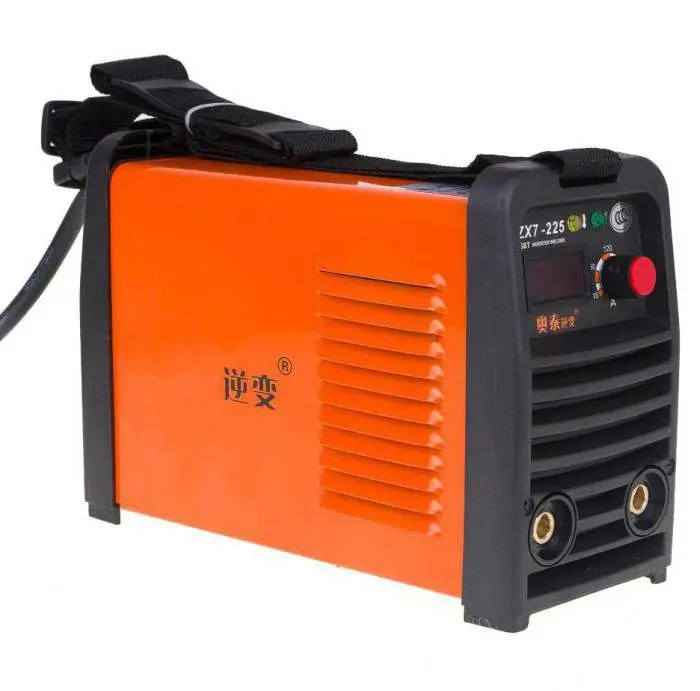
Actualmente, el proceso de soldadura para conectar cualquier estructura se usa de manera bastante activa. Los soldadores experimentados saben que con corriente continua el arco arde de manera más estable que con corriente alterna, lo que significa que la calidad de la soldadura será mayor. El convertidor de soldadura desempeña el papel de un transformador que convierte CA en CC
Cobre libre de oxígeno: características, beneficios, aplicaciones
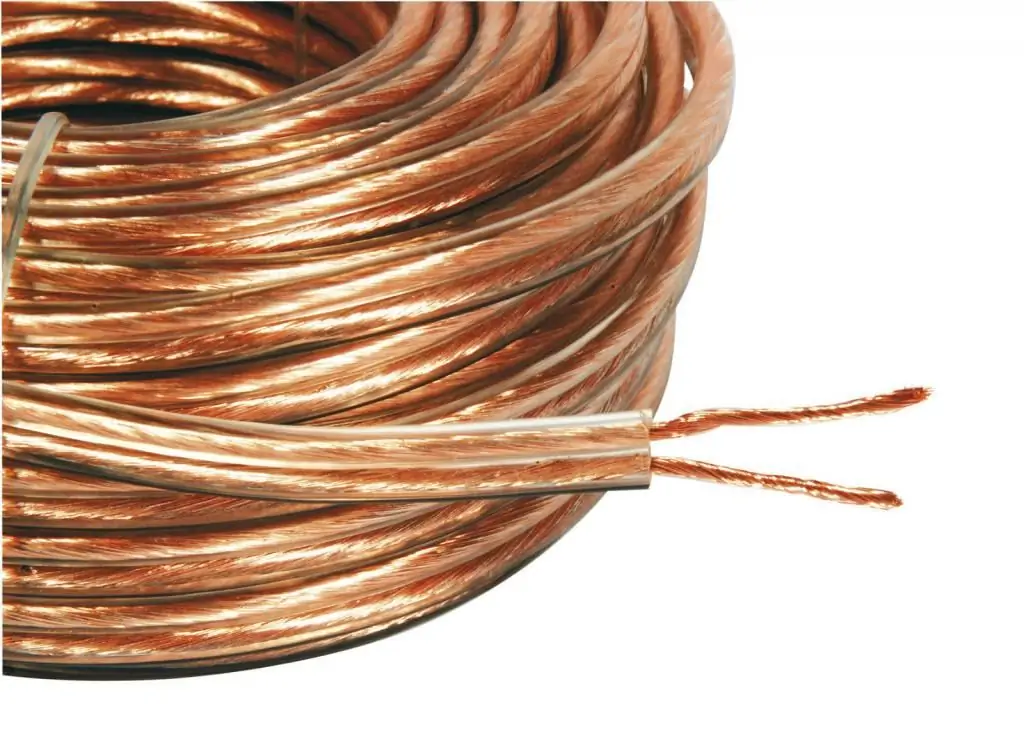
El cobre es un mineral que vive en la vida humana desde hace muchos milenios. En la antigüedad se utilizaba principalmente para obtener bronce, en aleación con estaño. En latín, su nombre es Cuprum. Se lo dio la antigua isla de Chipre, que fue uno de los primeros lugares donde se extrajo y fundió el cobre de las minas