2025 Autor: Howard Calhoun | [email protected]. Última modificación: 2025-01-24 13:15
El mineral de hierro se obtiene de la forma habitual: minería a cielo abierto o subterránea y posterior transporte para su preparación inicial, donde el material es triturado, lavado y procesado.
El mineral se vierte en un alto horno y se sopla con aire caliente y calor, lo que lo convierte en hierro fundido. Luego se retira del fondo del horno a moldes conocidos como raspadores, donde se enfría para producir arrabio. Se convierte en hierro forjado o se procesa en acero de varias maneras.
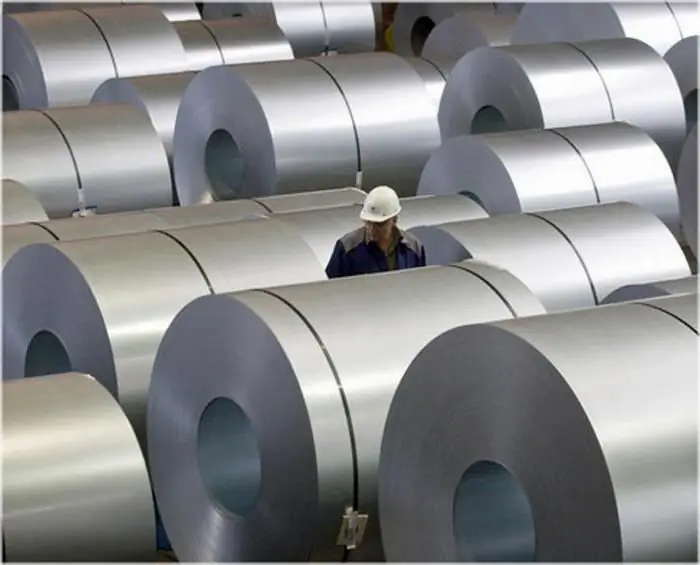
¿Qué es el acero?
Al principio había hierro. Es uno de los metales más comunes en la corteza terrestre. Se puede encontrar en casi todas partes, en combinación con muchos otros elementos, en forma de mineral. En Europa, el trabajo del hierro se remonta a 1700 aC
En 1786, los científicos franceses Berthollet, Monge y Vandermonde determinaron con precisión que la diferencia entre el hierro, el hierro fundido y el acero se debe al diferente contenido de carbono. Sin embargo, el acero, hecho de hierro, se convirtió rápidamente en el metal más importante de la Revolución Industrial. A principios del siglo XX, la producción mundial de acero era del 28millones de toneladas, esto es seis veces más que en 1880. Al comienzo de la Primera Guerra Mundial, su producción era de 85 millones de toneladas. Durante varias décadas, prácticamente ha reemplazado al hierro.
El contenido de carbono afecta las características del metal. Hay dos tipos principales de acero: aleado y sin alear. La aleación de acero se refiere a elementos químicos distintos del carbono agregado al hierro. Así, se utiliza una aleación de 17 % de cromo y 8 % de níquel para crear acero inoxidable.
Actualmente, existen más de 3000 marcas catalogadas (composiciones químicas), sin contar las creadas para satisfacer necesidades individuales. Todos ellos contribuyen a hacer del acero el material más adecuado para los retos del futuro.
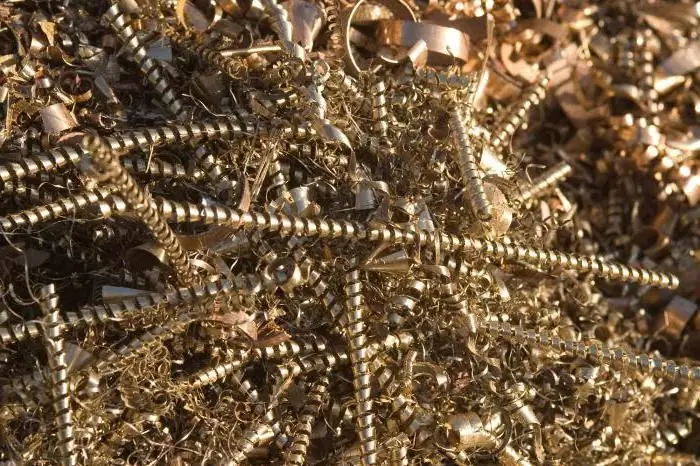
Materias primas siderúrgicas: primarias y secundarias
La fundición de este metal usando muchos componentes es el método de minería más común. Los materiales de carga pueden ser tanto primarios como secundarios. La composición principal de la carga, por regla general, es 55% de arrabio y 45% de la chatarra restante. Las ferroaleaciones, el hierro fundido convertido y los metales comercialmente puros se utilizan como elemento principal de la aleación; por regla general, todos los tipos de metales ferrosos se clasifican como secundarios.
El mineral de hierro es la materia prima más importante y básica en la industria siderúrgica. Se necesitan alrededor de 1,5 toneladas de este material para producir una tonelada de arrabio. Se utilizan alrededor de 450 toneladas de coque para producir una tonelada de arrabio. Muchas herrajesincluso se usa carbón vegetal.
El agua es una materia prima importante para la industria siderúrgica. Se utiliza principalmente para el enfriamiento del coque, el enfriamiento de altos hornos, la producción de vapor en las puertas de los hornos de carbón, la operación de equipos hidráulicos y la eliminación de aguas residuales. Se necesitan alrededor de 4 toneladas de aire para producir una tonelada de acero. El fundente se utiliza en el alto horno para extraer contaminantes del mineral de fundición. La piedra caliza y la dolomita se combinan con las impurezas extraídas para formar escoria.
Tanto los altos hornos como los de acero revestidos con refractarios. Se utilizan para revestimiento de hornos destinados a la fundición de mineral de hierro. Para el moldeo se utiliza dióxido de silicio o arena. Los metales no ferrosos se utilizan para producir acero de varios grados: aluminio, cromo, cob alto, cobre, plomo, manganeso, molibdeno, níquel, estaño, tungsteno, zinc, vanadio, etc. Entre todas estas ferroaleaciones, el manganeso se usa ampliamente en la fabricación de acero..
Los desechos de hierro de estructuras de fábricas desmanteladas, maquinaria, vehículos viejos, etc. se reciclan y se utilizan ampliamente en la industria.
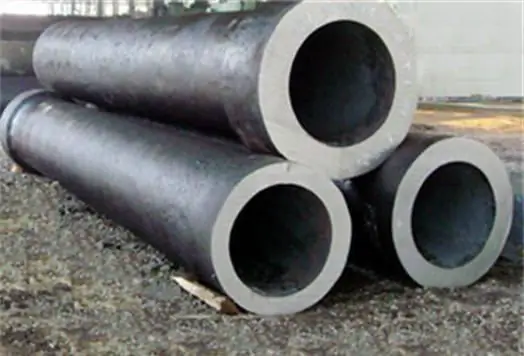
Hierro por acero
La fundición de acero con hierro fundido es mucho más común que con otros materiales. El hierro fundido es un término que generalmente se refiere al hierro gris, sin embargo, también se identifica con un gran grupo de ferroaleaciones. El carbono constituye aproximadamente del 2,1 al 4 % en peso, mientras que el silicio suele ser del 1 al 3 % en peso en la aleación.
La fundición de hierro y acero se realiza a una temperaturapunto de fusión entre 1150 y 1200 grados, que es aproximadamente 300 grados más bajo que el punto de fusión del hierro puro. El hierro fundido también exhibe buena fluidez, excelente maquinabilidad, resistencia a la deformación, oxidación y fundición.
El acero es también una aleación de hierro con un contenido de carbono variable. El contenido de carbono del acero es de 0,2 a 2,1% en masa y es el material de aleación más económico para el hierro. Fundir acero a partir de hierro fundido es útil para una variedad de propósitos estructurales y de ingeniería.
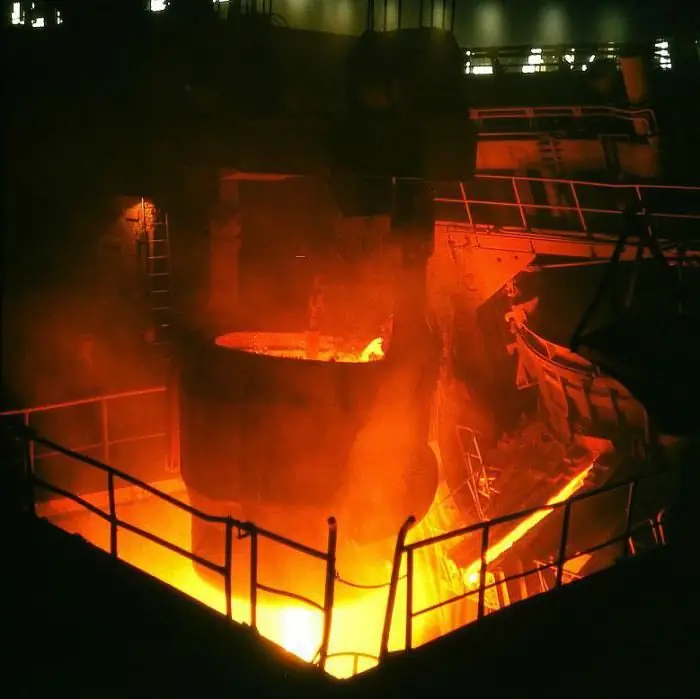
Mineral de hierro para acero
El proceso de fabricación del acero comienza con el procesamiento del mineral de hierro. La roca que contiene mineral de hierro se tritura. El mineral se extrae utilizando rodillos magnéticos. El mineral de hierro de grano fino se procesa en terrones de grano grueso para su uso en un alto horno. El carbón se refina en un horno de coque para producir una forma casi pura de carbono. Luego, la mezcla de mineral de hierro y carbón se calienta para producir hierro fundido, o arrabio, a partir del cual se fabrica acero.
En el horno de oxígeno principal, el mineral de hierro fundido es la principal materia prima y se mezcla con diversas cantidades de chatarra de acero y aleaciones para producir varios grados de acero. En un horno de arco eléctrico, la chatarra de acero reciclado se funde directamente en acero nuevo. Alrededor del 12% del acero está hecho de material reciclado.
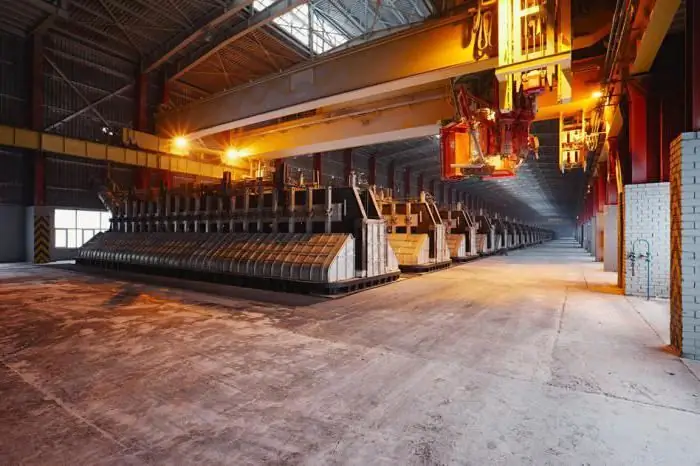
Tecnología de fundición
La fundición es un proceso mediante el cual se obtiene un metal en forma de elemento,ya sea como un compuesto simple a partir de su mineral calentándolo por encima de su punto de fusión, generalmente en presencia de agentes oxidantes como el aire o agentes reductores como el coque.
En la tecnología siderúrgica, el metal que se combina con oxígeno, como el óxido de hierro, se calienta a una temperatura alta y el óxido se forma en combinación con el carbono en el combustible, que se libera como monóxido de carbono o carbono dióxido. Otras impurezas, denominadas colectivamente venas, se eliminan añadiendo un chorro con el que se combinan para formar escoria.
La siderurgia moderna utiliza un horno de reverbero. El mineral concentrado y el flujo (generalmente piedra caliza) se cargan en la parte superior, mientras que la mata fundida (compuesto de cobre, hierro, azufre y escoria) se extrae del fondo. Es necesario un segundo tratamiento térmico en un horno convertidor para eliminar el hierro del acabado mate.
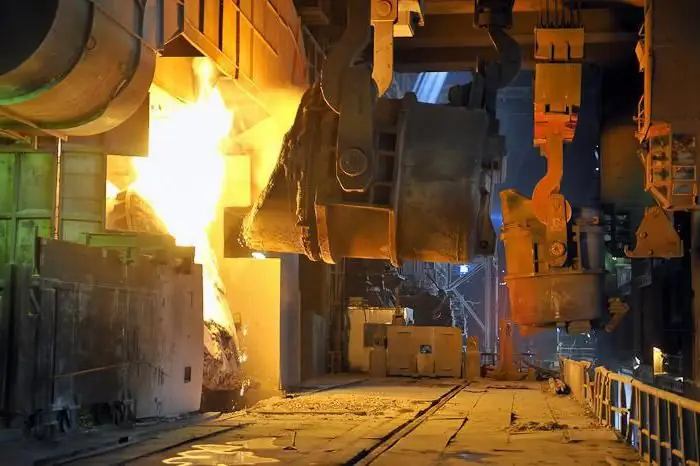
Método del convector de oxígeno
El proceso BOF es el proceso de fabricación de acero líder en el mundo. La producción mundial de acero para convertidores en 2003 ascendió a 964,8 millones de toneladas o el 63,3% de la producción total. La producción de convertidores es una fuente de contaminación ambiental. Los principales problemas de ésta son la reducción de emisiones, vertidos y reducción de residuos. Su esencia radica en el uso de energía secundaria y recursos materiales.
El calor exotérmico es generado por reacciones de oxidación durante la purga.
El principal proceso de fabricación de acero utilizando nuestro propioacciones:
- El hierro fundido (a veces llamado metal caliente) de un alto horno se vierte en un recipiente grande con revestimiento refractario llamado cucharón.
- El metal en la cuchara se envía directamente a la etapa principal de producción de acero o pretratamiento.
- Se inyecta oxígeno de alta pureza a una presión de 700-1000 kilopascales a una velocidad supersónica en la superficie del baño de hierro a través de una lanza enfriada por agua que se suspende en un recipiente y se mantiene unos pies por encima del baño.
La decisión del pretratamiento depende de la calidad del metal caliente y de la calidad final deseada del acero. Los primeros convertidores inferiores extraíbles que se pueden desmontar y reparar todavía están en uso. Se han cambiado las lanzas utilizadas para soplar. Para evitar que la lanza se atasque durante el soplado, se utilizaron collares ranurados con una punta de cobre larga y ahusada. Las puntas de la punta, después de la combustión, queman el CO formado cuando se insufla en CO2 y proporcionan calor adicional. Para eliminar la escoria se utilizan dardos, bolas refractarias y detectores de escoria.
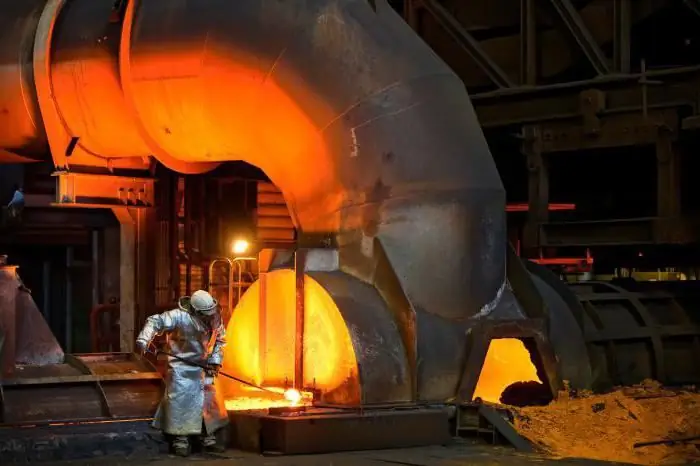
Método del convector de oxígeno: ventajas y desventajas
No requiere el costo del equipo de purificación de gas, ya que la formación de polvo, es decir, la evaporación del hierro, se reduce 3 veces. Debido a la disminución del rendimiento del hierro, se observa un aumento del rendimiento del acero líquido en un 1,5 - 2,5%. La ventaja es que la intensidad de soplado en este método aumenta, lo que dala capacidad de aumentar el rendimiento del convertidor en un 18%. La calidad del acero es mayor porque la temperatura en la zona de purga es menor, lo que da como resultado una menor formación de nitrógeno.
Las deficiencias de este método de fundición de acero provocaron una disminución de la demanda de consumo, ya que el nivel de consumo de oxígeno aumenta en un 7% debido al alto consumo de combustión de combustible. Hay un mayor contenido de hidrógeno en el metal reciclado, por lo que se necesita un tiempo después de finalizar el proceso para realizar una purga con oxígeno. Entre todos los métodos, el convertidor de oxígeno tiene la formación de escoria más alta, la razón es la incapacidad de monitorear el proceso de oxidación dentro del equipo.
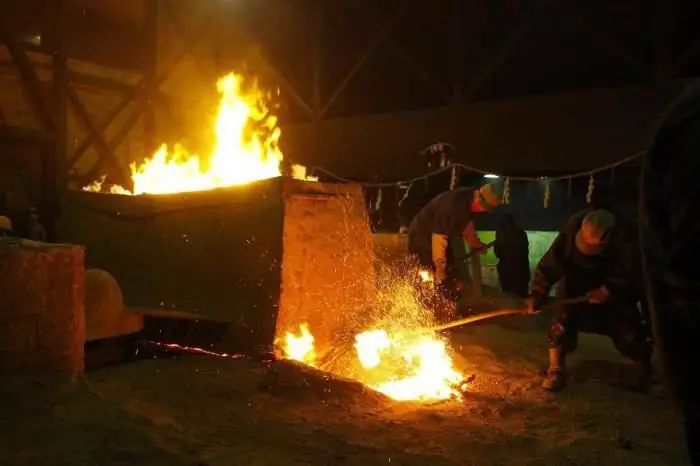
Método de hogar abierto
El proceso de hogar abierto durante la mayor parte del siglo XX fue la parte principal del procesamiento de todo el acero fabricado en el mundo. William Siemens, en la década de 1860, buscó un medio para elevar la temperatura en un horno metalúrgico, resucitando una antigua propuesta para utilizar el calor residual generado por el horno. Calentó el ladrillo a una temperatura alta y luego usó el mismo camino para introducir aire en el horno. El aire precalentado aumentó significativamente la temperatura de la llama.
Se utiliza como combustible gas natural o aceites pesados atomizados; el aire y el combustible se calientan antes de la combustión. El horno se carga con arrabio líquido y chatarra de acero junto con mineral de hierro, piedra caliza, dolomita y fundentes.
La estufa en sí está hecha demateriales altamente refractarios como los ladrillos de hogar de magnesita. Los hornos de solera abierta pesan hasta 600 toneladas y generalmente se instalan en grupos, de modo que el enorme equipo auxiliar necesario para cargar los hornos y procesar el acero líquido se puede usar de manera eficaz.
Aunque el proceso de hogar abierto ha sido reemplazado casi por completo en la mayoría de los países industrializados por el proceso básico de oxígeno y el horno de arco eléctrico, produce alrededor de 1/6 de todo el acero producido en todo el mundo.
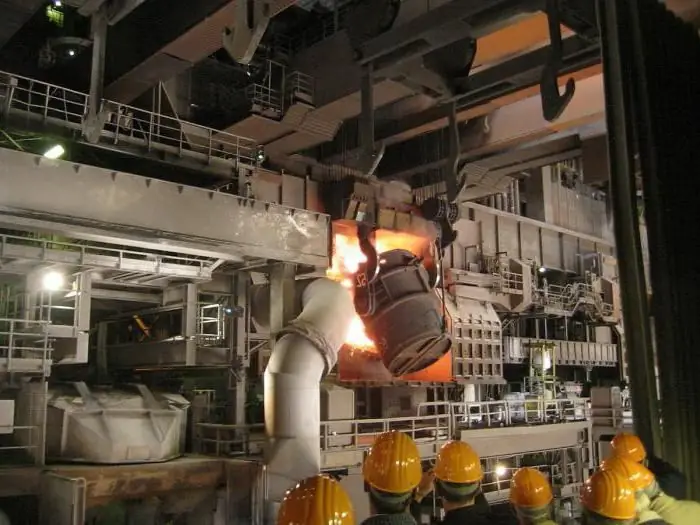
Ventajas y desventajas de este método
Las ventajas incluyen la facilidad de uso y la facilidad de producción de acero aleado con varios aditivos que le dan al material varias propiedades especializadas. Los aditivos y aleaciones necesarios se añaden inmediatamente antes de finalizar la fundición.
Las desventajas incluyen una eficiencia reducida en comparación con el método del convertidor de oxígeno. Además, la calidad del acero es inferior en comparación con otros métodos de fundición de metales.
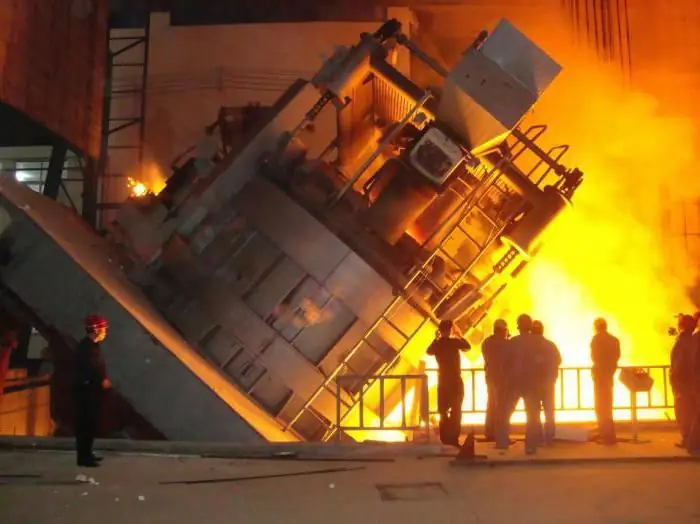
Método de fabricación de acero eléctrico
El método moderno de fundición de acero utilizando nuestras propias reservas es un horno que calienta un material cargado con un arco eléctrico. Los hornos de arco industriales varían en tamaño desde unidades pequeñas con una capacidad de aproximadamente una tonelada (utilizadas en fundiciones para la producción de productos de hierro) hasta unidades de 400 toneladas utilizadas en metalurgia secundaria.
Hornos de arco,utilizados en laboratorios de investigación pueden tener una capacidad de sólo unas pocas decenas de gramos. Las temperaturas de los hornos de arco eléctrico industriales pueden alcanzar los 1800 °C (3272 °F), mientras que las instalaciones de laboratorio pueden superar los 3000 °C (5432 °F).
Los hornos de arco se diferencian de los hornos de inducción en que el material de carga se expone directamente a un arco eléctrico y la corriente en los terminales pasa a través del material cargado. El horno de arco eléctrico se utiliza para la producción de acero, consiste en un revestimiento refractario, generalmente enfriado por agua, de gran tamaño, cubierto con un techo retráctil.
El horno se divide principalmente en tres secciones:
- Carcasa compuesta por paredes laterales y cubeta inferior de acero.
- El hogar consiste en un refractario que extrae el recipiente inferior.
- El techo con revestimiento refractario o enfriado por agua se puede hacer como una sección esférica o un cono truncado (sección cónica).
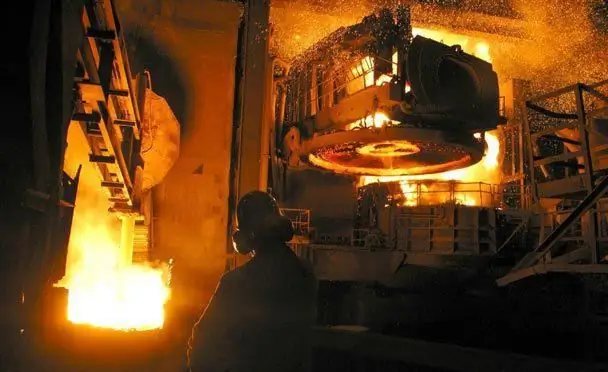
Ventajas y desventajas del método
Este método ocupa una posición de liderazgo en el campo de la producción de acero. El método de fundición de acero se utiliza para crear metal de alta calidad que está completamente desprovisto o contiene una pequeña cantidad de impurezas no deseadas, como azufre, fósforo y oxígeno.
La principal ventaja del método es el uso de electricidad para el calentamiento, por lo que puede controlar fácilmente la temperatura de fusión y lograr una velocidad increíble de calentamiento del metal. El trabajo automatizado se convertiráuna adición agradable a la excelente oportunidad para el procesamiento de alta calidad de chatarra diversa.
Las desventajas incluyen un alto consumo de energía.
Recomendado:
Acero inoxidable alimentario: GOST. ¿Cómo identificar el acero inoxidable de calidad alimentaria? ¿Cuál es la diferencia entre el acero inoxidable alimentario y el acero inoxidable

El artículo habla de grados de acero inoxidable apto para alimentos. Lea cómo distinguir el acero inoxidable alimentario del técnico
Acero resistente a la corrosión. Grados de acero: GOST. Acero inoxidable - precio
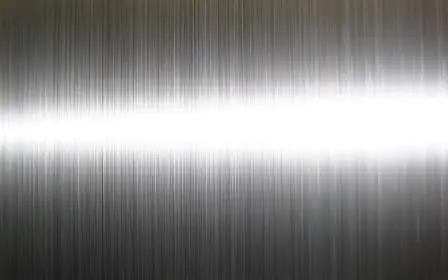
Por qué los materiales metálicos se descomponen. ¿Qué son los aceros y aleaciones resistentes a la corrosión? Composición química y clasificación según el tipo de microestructura del acero inoxidable. Factores que afectan la fijación de precios. Sistema de designación de grado de acero (requisitos GOST). Área de aplicación
Obtención de alcoholes: métodos y materias primas
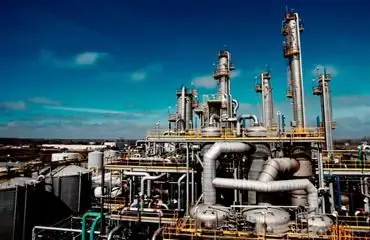
La obtención de alcoholes es un proceso tecnológico bastante complicado. Existen métodos bioquímicos y químicos para la obtención de alcoholes. La obtención de alcohol metílico se lleva a cabo mediante el uso de diversas tecnologías
Producción de espuma de poliuretano: tecnología, materias primas, equipos
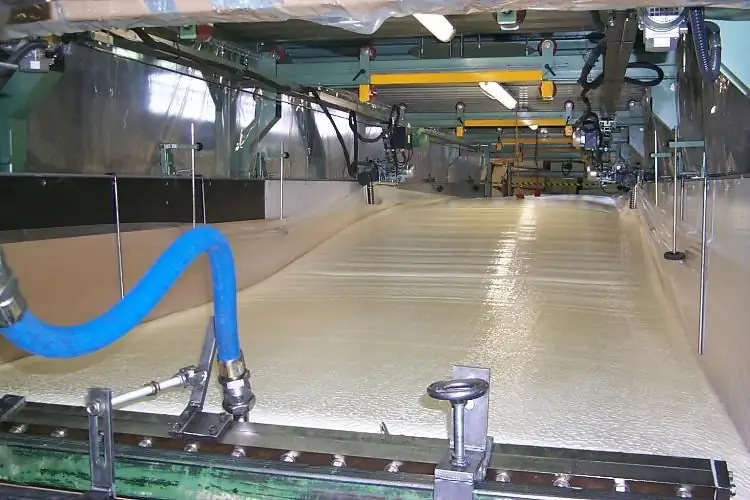
La espuma de montaje de los medios habituales para sellar las aberturas de las ventanas pasó hace mucho tiempo al estado de un material de construcción completo, que se usa ampliamente en una variedad de tipos de trabajo. La variedad de aplicaciones de este producto también determina la necesidad de un enfoque diferenciado de las tecnologías de su fabricación. Sin embargo, las diferencias en los métodos de producción de espuma de poliuretano son más de naturaleza cosmética, sin afectar los procesos tecnológicos básicos
Producción de tubos de PVC: tecnología, materias primas y equipos
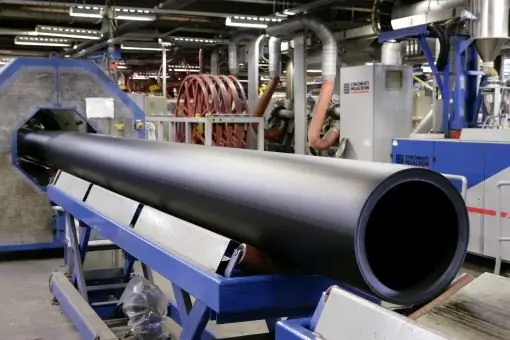
Los productos tubulares a base de cloruro de polivinilo (PVC) se utilizan ampliamente en una variedad de áreas e industrias, desde el sector privado hasta las grandes empresas de petróleo y gas. Pero el proceso de su consolidación en el mercado fue gradual, ya que las propiedades físicas y técnicas del material polimérico son inferiores a las contrapartes metálicas tradicionales en una serie de criterios. Sin embargo, la producción moderna de tuberías de PVC, debido a la introducción de tecnologías avanzadas, ha aumentado significativamente el rendimiento de los productos