2025 Autor: Howard Calhoun | [email protected]. Última modificación: 2025-01-24 13:15
La calidad de la soldadura está determinada por la resistencia de la costura. Al mismo tiempo, el control de la conexión debe ser no destructivo, lo que obliga a los maestros a recurrir a métodos de verificación especiales una vez que se completa la operación. En algunos casos, también se permite la inspección externa sin instrumentos, pero en el caso de estructuras críticas, la inspección visual no puede limitarse. Puede complementarse con la detección de defectos de color en las soldaduras, uno de los métodos más efectivos, convenientes y confiables para analizar tales uniones.

Características del método de verificación
Este método de verificación de soldaduras se refiere al capilar, pero se enfoca únicamente en la resolución de problemas externos. Es decir, no se puede utilizar para comprobar la estructura interna de la zona de unión, a diferencia, por ejemplo, de la detección de defectos por ultrasonidos. Por lo general, los metales propensos al agrietamiento se someten a tales pruebas. Además, el control de color le permite identificar con eficacia las discontinuidades que salen a la superficie.
En cuanto al principio de verificación, se basa en la sensibilidad de los metales a la interacción con materiales no ferrosos no defectuososcópicos. Contrariamente a la creencia popular, el análisis comola información controlada no utiliza las características de la superficie de la pieza, sino los cambios provocados por la irritación de la estructura con productos químicos. El método de detección de defectos de color se basa en los procesos de exposición química, lo que le permite procesar información sobre los cambios y proporcionar datos sobre los defectos metálicos identificados en la salida.
El método en sí rara vez se usa solo. Por lo general, se usa en el complejo de verificación general, junto con ultrasonido. Primero sigue el análisis de color, seguido de la prueba ultrasónica.
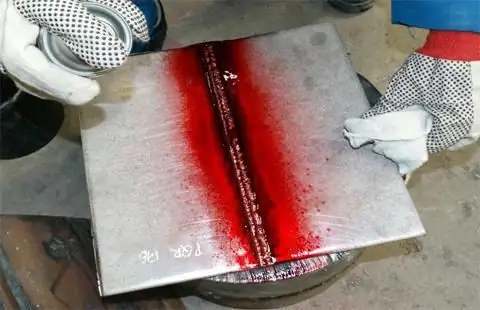
Materiales aplicados
Como ya se mencionó, la detección de fallas no está completa sin el uso de productos químicos especiales. El kit estándar para la detección de defectos de color incluye tres tipos de componentes: indicador penetrante, agente de limpieza y revelador. Es decir, el control de sensibilidad de color se activará mediante el procesamiento de tres etapas del área de trabajo. En cada etapa se utilizan materiales especiales.
Los penetrantes son, de hecho, sustancias colorantes que pueden presentarse en diferentes formas. También se utilizan productos en polvo, pero para su uso deben introducirse operaciones adicionales de acción térmica o mezcla con líquidos. Los penetrantes adecuados para un metal en particular para la detección de fallas no ferrosas se seleccionan en función de varias propiedades de rendimiento. Tiene en cuenta, en particular, la resistencia al fuego, el respeto por el medio ambiente y la toxicidad, la eliminación de la necesidad de decapado posterior, etc.
Requisitos paralugar de control
La operación de detección de fallas solo puede llevarse a cabo en una habitación especialmente preparada. Es importante tener en cuenta los requisitos de los equipos de comunicación del lugar, de las características del aire, soporte técnico, etc. La sala debe estar ventilada, no tener fuentes de llama abierta o calor intenso. La iluminación debe ser general y local, las lámparas cercanas al sitio de la operación deben protegerse de los efectos térmicos.
Al principio, debe tener cuidado de crear un microclima óptimo: solo en condiciones favorables se puede llevar a cabo una detección de defectos de color de calidad. GOST 18442-80, en particular, indica que el aire debe estar seco y cálido; si es necesario, para lograr estas características, puede usar un calentador infrarrojo que secará el revelador a un nivel de 5 ° C. El equipamiento técnico dependerá de los métodos de aplicación de los componentes químicos. En particular, se pueden utilizar pistolas pulverizadoras, botes de aerosol, brochas, etc. para aplicar el mismo penetrante.
Preparando la costura base
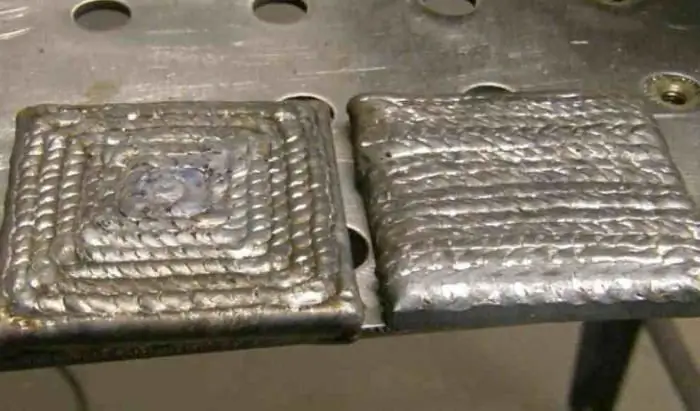
La sección de conexión también se está preparando para la operación de detección de defectos. Si hay una aspereza pronunciada o contaminación en la superficie, entonces puede usar material de grano fino y hacer un procesamiento ligero. Lo siguiente es desengrasar. Para esta tarea se puede utilizar uno de los componentes del kit de detección de fallas, pero es importante que proporcione el efecto desengrasante, y mejor aún, aumentesensibilidad de control No se recomienda usar queroseno para tales fines, pero se puede usar gasolina y acetona. Si no hay ventilación en la habitación, el desengrase se realiza solo con soluciones acuosas a base de agentes sintéticos en polvo de baja concentración. Si se planea la detección de defectos de color de una pieza pequeña, también se puede utilizar la inmersión total en una composición desengrasante. En otros casos, se utiliza la técnica de rociar sobre el área objetivo o la aplicación con un trapo empapado en la solución.
Aplicar penetrante
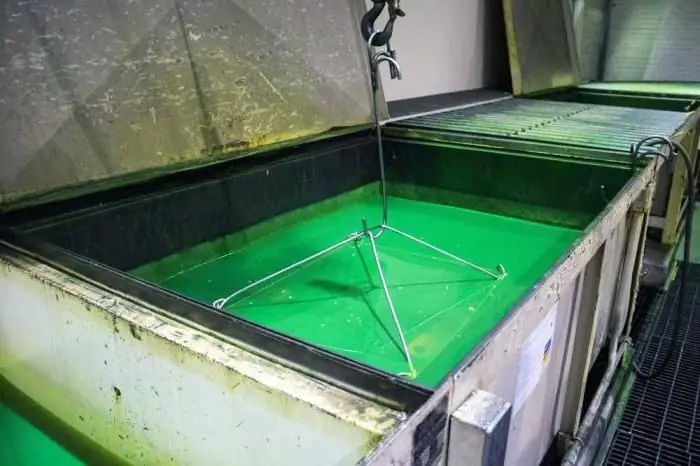
En primer lugar, se aplica el indicador penetrante. Al igual que el desengrasado, este procedimiento se puede realizar por pulverización, inmersión o cepillado, según las características de la pieza. Además, la aplicación debe realizarse en varias capas (4-6) y para que cada capa anterior de la composición no tenga tiempo de secarse. Además, para que la detección de defectos de color de las soldaduras muestre un resultado óptimo y preciso, cada capa posterior debe cubrir un área más grande en relación con la anterior. Esto se debe a que cada nueva capa disolverá el contorno de la mancha anterior, evitando transiciones bruscas y descolgamientos, que pueden percibirse como falsas grietas. Si la operación se realiza en condiciones de temperatura negativa, entonces el propio penetrante debe tener un estado de unos 15 °C.
Eliminación de penetrantes
Inmediatamente después de la aplicación, la película indicadora debe retirarse con un pañuelo limpio o un paño sin asperezas.montón. Previamente se debe humedecer el material con alcohol etílico y limpiar la superficie hasta eliminar completamente el recubrimiento. Pueden surgir problemas si se trabaja en la superficie de un metal en bruto; en este caso, tiene sentido utilizar abrasivos ligeros. A continuación, se aplica una mezcla de aceite y queroseno. Cubre toda el área objetivo y luego también se retira con trapos o servilletas. Durante las dos etapas descritas, la detección de defectos de color debe mantener la superficie limpia y seca alrededor de la costura. Esto es importante para mantener la precisión de los procedimientos de control posteriores.
Aplicar revelador
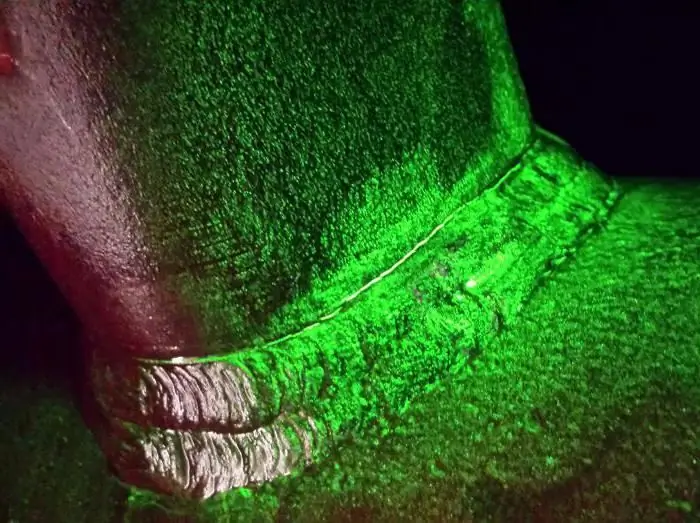
Al igual que con las capas indicadoras y los limpiadores, el revelador se aplica de diversas formas, desde brochas hasta pistolas rociadoras. Lo principal en esta etapa es observar la uniformidad y solidez del recubrimiento formado. Por lo tanto, es necesario revisar cuidadosamente las herramientas de rociado, las boquillas y otros elementos de los dispositivos que afectan la calidad de la entrega del producto al sitio de destino. Todo esto afectará aún más al control de la detección de defectos de color, así como a la calidad de las operaciones de verificación posteriores. El secado se realiza después de aplicar el revelador. No se puede realizar, esperando la polimerización en condiciones naturales, pero para acelerar el proceso, se permite el uso de calentadores puntuales de baja potencia.
Inspección del área controlada
Cuando el revelador esté seco, puede prepararse para inspeccionarlo esperando otros 30 minutos más o menos. El control adicional mediante el método de detección de defectos de color implica el uso de una lupa,proporcionando un aumento mínimo de 5x. Si se utiliza la técnica capa por capa, la prueba se puede realizar tan pronto como 2 minutos después del procesamiento con el revelador.
Durante el proceso de evaluación, el operador captura las características de la mancha que queda; en particular, registra las dimensiones de los contornos, la forma, etc. La tarea principal de la detección de defectos de color es detectar los defectos de la superficie que se manifiestan claramente después de los procedimientos de finalización. Se pueden identificar tanto daños mecánicos como rastros de ataque corrosivo, así como grietas con descolgamiento excesivo.
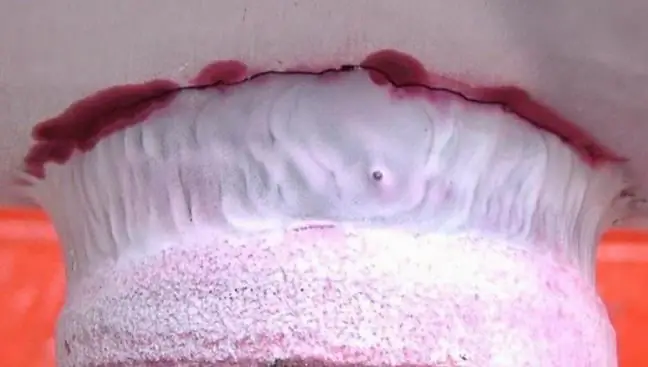
Seguridad en la detección de fallas
Los requisitos para las medidas de seguridad se deben a la amenaza de incendio y explosión durante la detección de fallas. Por lo tanto, es necesario al menos preparar un mono, que incluya una bata de algodón, un tocado y guantes de goma, cuya superficie debe cubrirse con talco. En el sitio mismo, las medidas de seguridad deben observarse en su totalidad. Durante el procedimiento, no debe haber fuentes abiertas de fuego o chispas. Si la prueba de penetración de color se realiza regularmente en la misma habitación, se deben instalar letreros apropiados de protección contra incendios y de no fumar. Los trapos, toallitas y productos inflamables deben guardarse en un recipiente ignífugo.
Conclusión
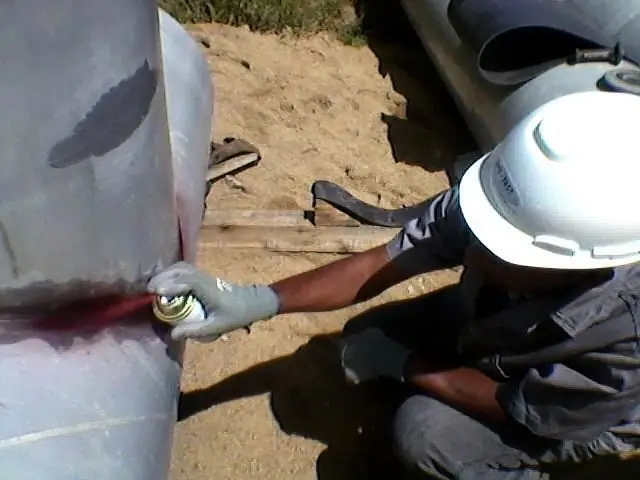
Sería un error considerar este método para evaluar la calidad de una soldaduracomo óptimo, eligiéndolo de la gama general de otros métodos. Este es un método de examen especialmente dirigido, que se centra específicamente en el análisis de la superficie de la pieza de trabajo. Es decir, la detección de fallas de color no es una medida de control integral, pero proporciona información sobre fallas externas con una eficiencia relativamente alta. Si este método se complementa con otros métodos para estudiar la estructura interna de la soldadura, se puede obtener información completa sobre la estructura del metal. Además, ya se ha tomado una decisión sobre la posible corrección de los defectos identificados. En algunos casos, se realiza una soldadura secundaria; esto dependerá de la cantidad y la importancia de los defectos en términos de afectar la resistencia de la estructura de la pieza de trabajo. A veces, la resolución de problemas de este tipo también se utiliza para analizar la estructura de costuras y juntas antiguas en estructuras operadas.
Recomendado:
Control visual de soldaduras: la esencia de la conducta y procedimiento paso a paso

Elimine por completo el riesgo de conexiones de baja calidad, ni siquiera permita máquinas de soldadura automáticas y robóticas. Por tanto, independientemente de la tecnología aplicada para la producción de las operaciones de soldadura, tras su ejecución se implanta un procedimiento de control exhaustivo de la calidad de las soldaduras. El método de inspección visual es la etapa inicial en el proceso general de resolución de problemas de soldadura
Color del caballo marrón: descripción, historia, características y curiosidades
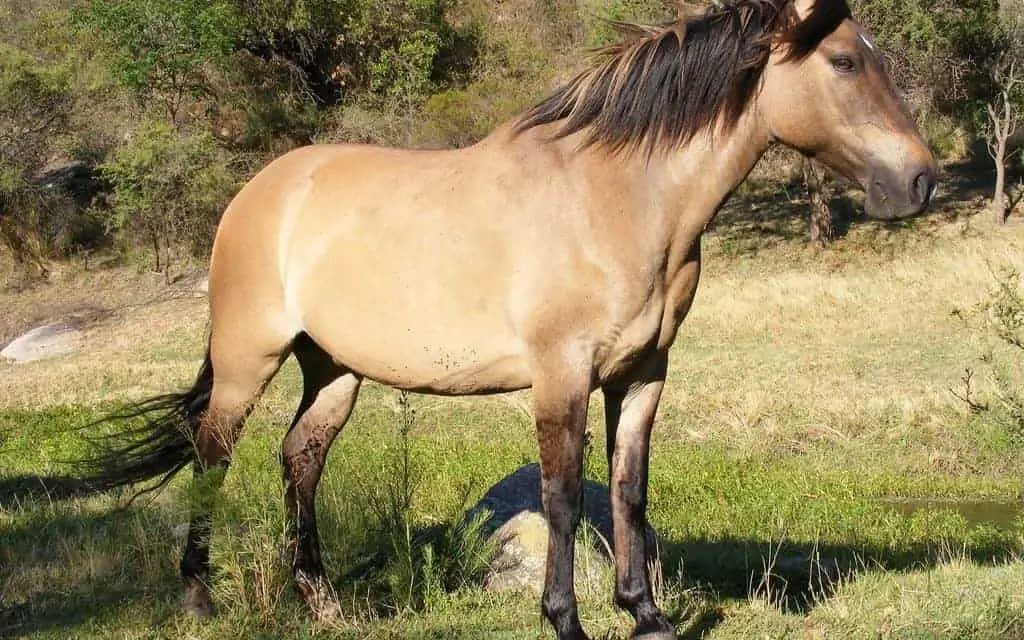
¿De dónde viene el nombre del color del caballo? La historia de la aparición de la raza y algunos datos interesantes. Las principales variedades de caballos de ante. Varias descripciones de la apariencia y características de los caballos de piel de ante. La historia de los caballos de ante en la cultura. Confusión con otras razas
¿Qué son las pruebas radiográficas? Control radiográfico de soldaduras. Control radiográfico: GOST
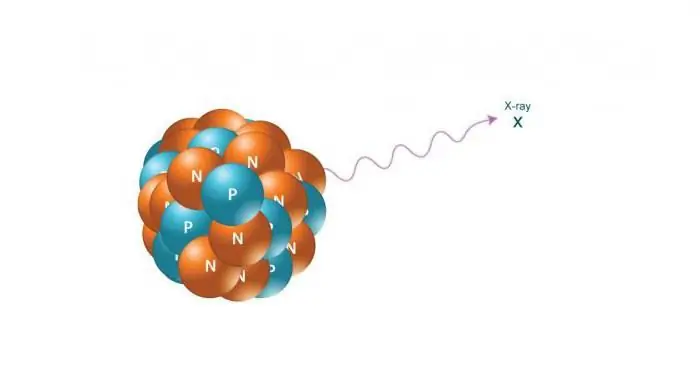
Bases físicas de los métodos de control de la radiación. Características del control radiográfico. Las principales etapas del control radiográfico de las soldaduras. Precauciones de seguridad en la producción de control radiográfico. Documentación normativa y técnica
Defectos de los rieles y su clasificación. Estructura de designación de defectos ferroviarios
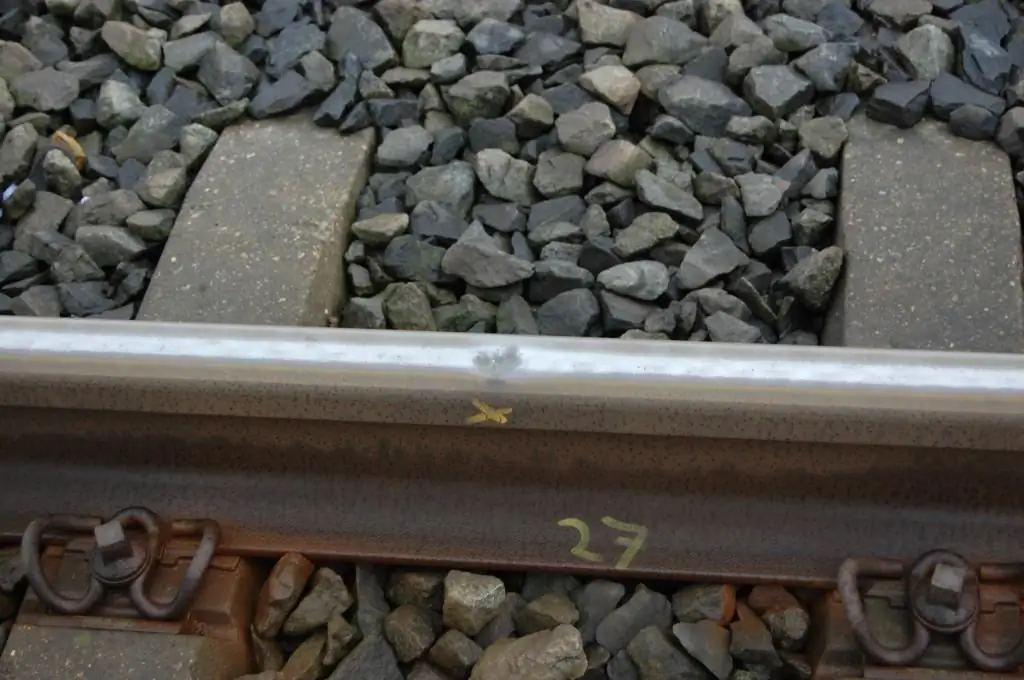
Actualmente, la gente está utilizando activamente el ferrocarril. La entrega de varios tipos de carga por esta ruta es el principal tipo de transporte. Sin embargo, debido al gran peso de los propios trenes, así como a la carga que transportan, existe una fuerte presión sobre los raíles. Los defectos en estos objetos son una ocurrencia bastante común, que debe eliminarse de inmediato
Defectos de la madera: tipos, descripción y remedios
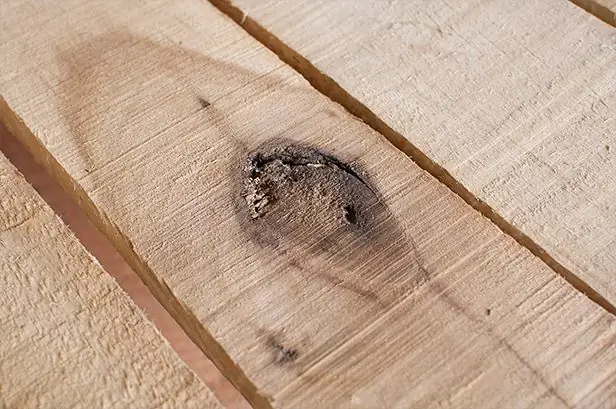
Hoy en día, hay muchos materiales de construcción. Uno de los más antiguos, pero al mismo tiempo, la madera se ha generalizado. Sin embargo, como es sabido, este material está "vivo" y, por lo tanto, no está exento de defectos naturales. La madera es muy susceptible a diversas influencias