2025 Autor: Howard Calhoun | calhoun@techconfronts.com. Última modificación: 2025-01-24 13:15
Un horno de arco de acero (EAF) es un dispositivo que calienta el material por flexión eléctrica.
Los electrodomésticos industriales varían en tamaño desde unidades pequeñas, de aproximadamente una tonelada de energía (utilizadas en fundiciones para fabricar productos de hierro fundido) hasta 400 unidades por tonelada, utilizadas para el reciclaje de acero. Los hornos de arco de acero, EAF, utilizados en laboratorios de investigación pueden tener una capacidad de solo unas pocas decenas de gramos. La temperatura de los dispositivos industriales puede alcanzar los 1800 °C (3272 °F), mientras que las instalaciones de laboratorio superan los 3000 °C (5432 °F).
Los hornos de arco de acero (EAF) se diferencian de los hornos de inducción en que el material que se carga se somete directamente a la flexión eléctrica y la corriente en los terminales pasa a través del material cargado.
Construcción
El horno de acero de arco se utiliza para la producción de acero y se compone de un recipiente refractario. Principalmente dividido en tres secciones:
- Carcasa, que consta de paredes laterales y acero inferiorcuencos.
- Palet de material refractario.
- Techo. Puede ser con revestimiento resistente al calor o refrigerado por agua. Y también se hace en forma de bola o de tronco de cono (sección cónica). El techo también soporta un delta refractario en su centro a través del cual entran uno o más electrodos de grafito.
Artículos individuales
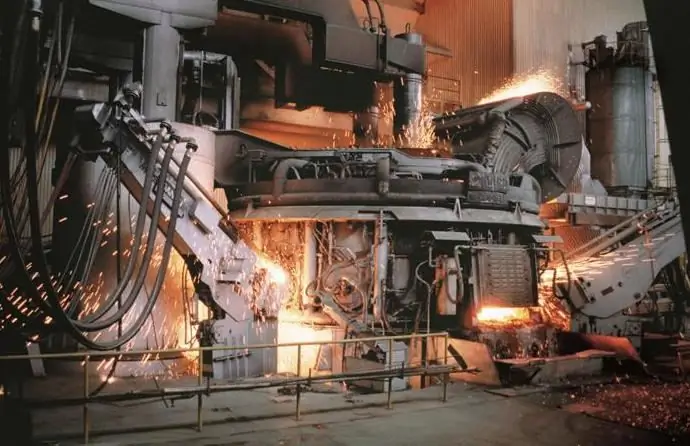
El hogar puede tener una forma semiesférica y se necesita en un horno excéntrico para colar el fondo. En los talleres modernos, el horno de arco de acero - EAF 5 - a menudo se eleva por encima del suelo para que los cucharones y las ollas de escoria se puedan maniobrar fácilmente debajo de cualquiera de los extremos. Separado de la estructura se encuentra el soporte de electrodos y el sistema eléctrico, así como la plataforma inclinada sobre la que se apoya el instrumento.
Herramienta única
Un horno de arco de fundición de acero EAF 3 típico está alimentado por una fuente trifásica y, por lo tanto, tiene tres electrodos. Son de sección redonda y, por regla general, de segmentos con conexiones roscadas, de modo que a medida que se desgastan se pueden añadir nuevos elementos.
El arco se forma entre el material cargado y el electrodo. La carga se calienta tanto por la corriente que pasa a través de ella como por la energía radiada liberada por la onda. La temperatura alcanza unos 3000 °C (5000 °F), lo que hace que las secciones inferiores de los electrodos brillen como lámparas incandescentes cuando el horno de arco está en funcionamiento.
Los elementos suben y bajan automáticamente mediante un sistema de posicionamiento que puede utilizar cualquiercabrestante, polipastos o cilindros hidráulicos. La regulación mantiene una corriente aproximadamente constante. ¿Cuál es el consumo de energía de un horno de arco? Se mantiene constante durante la fusión de la carga, aunque la chatarra puede moverse debajo de los electrodos a medida que se funde. Los manguitos del mástil que sostienen el elemento pueden transportar barras colectoras pesadas (que pueden ser tubos de cobre huecos enfriados por agua que suministran corriente a las abrazaderas) o "manguitos calientes" donde toda la parte superior transporta la carga, lo que aumenta la eficiencia.
Este último tipo puede ser de acero cobreado o de aluminio. Grandes cables refrigerados por agua conectan barras colectoras o soportes a un transformador ubicado al lado del horno. Una herramienta similar se instala en el almacenamiento y se enfría con agua.
Toques y otras operaciones
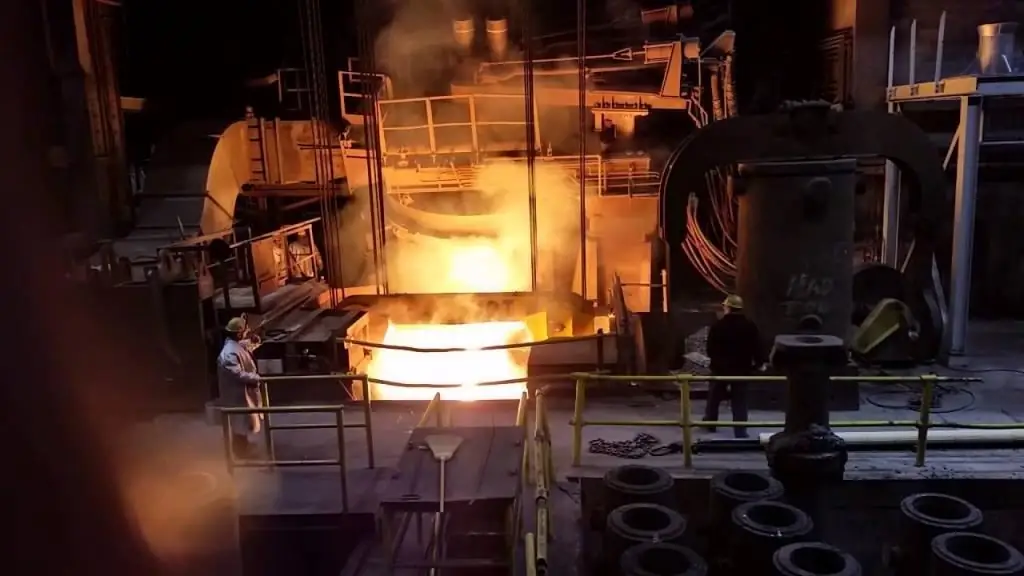
El horno de arco de acero EAF 50 está construido sobre una plataforma inclinada para que el acero líquido se pueda verter en otro contenedor para su transporte. La operación de basculación para transferir acero fundido se denomina roscado. Inicialmente, todas las bóvedas de fabricación de acero del horno de arco tenían un conducto de descarga cubierto con refractario, que se lavaba cuando se inclinaba.
Pero a menudo los equipos modernos tienen una válvula de salida inferior excéntrica (EBT) para reducir la incorporación de nitrógeno y escoria en el acero líquido. Estos hornos tienen una abertura que corre verticalmente a través del hogar y la carcasa y está descentrada en un "pico" angosto en forma de huevo. esta llenoarena refractaria.
Las plantas modernas pueden tener dos caparazones con un juego de electrodos que se pasan entre ellos. La primera parte calienta la chatarra, mientras que la otra se usa para fundir. Otros hornos de CC tienen un diseño similar pero tienen electrodos para cada vaina y un conjunto de componentes electrónicos.
Elementos de oxígeno
Los hornos de CA generalmente tienen un patrón de puntos calientes y fríos a lo largo del perímetro del hogar, ubicados entre los electrodos. En los modernos, los quemadores de oxígeno y combustible están instalados en la pared lateral. Se utilizan para suministrar energía química a las zonas negativas, lo que hace que el calentamiento del acero sea más uniforme. Se proporciona energía adicional al suministrar oxígeno y carbón al horno. Históricamente, esto se hacía con lanzas (tubos huecos de acero dulce) en la puerta de escoria, ahora se hace principalmente con unidades de inyección montadas en la pared que combinan quemadores de oxicombustible y sistemas de suministro de aire en un solo recipiente.
Un horno de acero moderno de tamaño mediano tiene un transformador clasificado en aproximadamente 60 000 000 voltios-amperios (60 MVA), con un voltaje secundario de 400 a 900 y una corriente superior a 44 000. En un taller moderno, tal Se espera que el horno produzca 80 toneladas métricas de acero líquido en unos 50 minutos, desde la carga de chatarra en frío hasta la extracción.
En comparación, los hornos de oxígeno básicos pueden tener una capacidad de 150 a 300 toneladas por lote o "calentarse" y generar calor durante 30 a 40 minutos. Existen enormes diferencias en los detalles del diseño y funcionamiento del horno,según el producto final y las condiciones locales, así como la investigación en curso para mejorar la eficiencia de la planta.
El desecho más grande (en términos de peso de derivación y clasificación del transformador) es un dispositivo de CC exportado de Japón con un peso de derivación de 420 toneladas métricas y alimentado por ocho transformadores de 32 MVA para una potencia total de 256 MBA.
Se necesitan aproximadamente 400 kilovatios-hora para producir una tonelada de acero en un horno de arco eléctrico, o alrededor de 440 kWh por metro. La energía mínima teórica requerida para fundir chatarra de acero es de 300 kWh (punto de fusión 1520 °C / 2768 °F). Por lo tanto, un horno eléctrico eléctrico de 300 toneladas con una potencia de 300 MVA requerirá alrededor de 132 MWh de energía y el tiempo de encendido es de aproximadamente 37 minutos.
La producción de acero con arco eléctrico solo es económicamente viable si hay suficiente electricidad con una red bien desarrollada. En muchos lugares, las plantas operan fuera de las horas pico cuando las empresas de servicios públicos tienen un exceso de capacidad de producción y el precio por metro es más bajo.
Operación
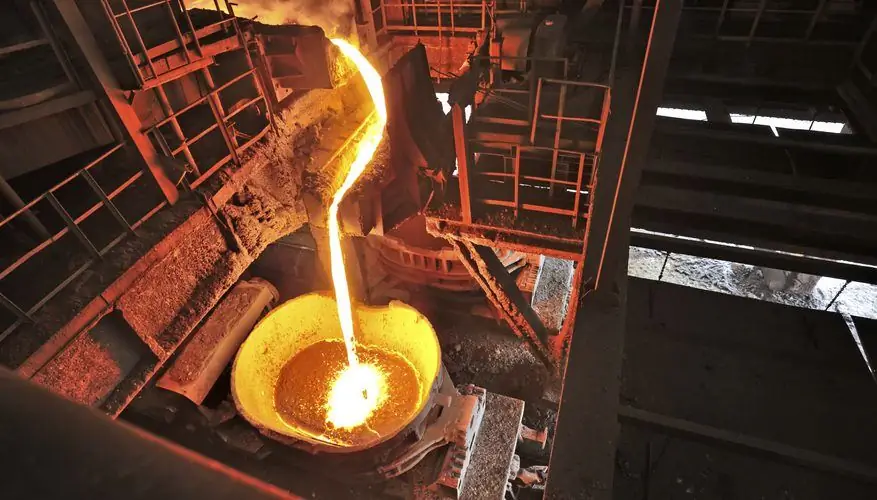
El horno de arco de acero vierte acero en una pequeña máquina de cucharón. La chatarra se entrega a un nicho ubicado al lado de la fundición. La chatarra tiende a presentarse en dos variedades principales: chatarra (electrodomésticos, automóviles y otros artículos hechos de materiales similares).acero ligero) y fundición pesada (losas y vigas grandes), así como algo de hierro reducido directo (DRI) o arrabio para el equilibrio químico. Los hornos separados derriten casi el 100 % de DRI.
Siguiente paso
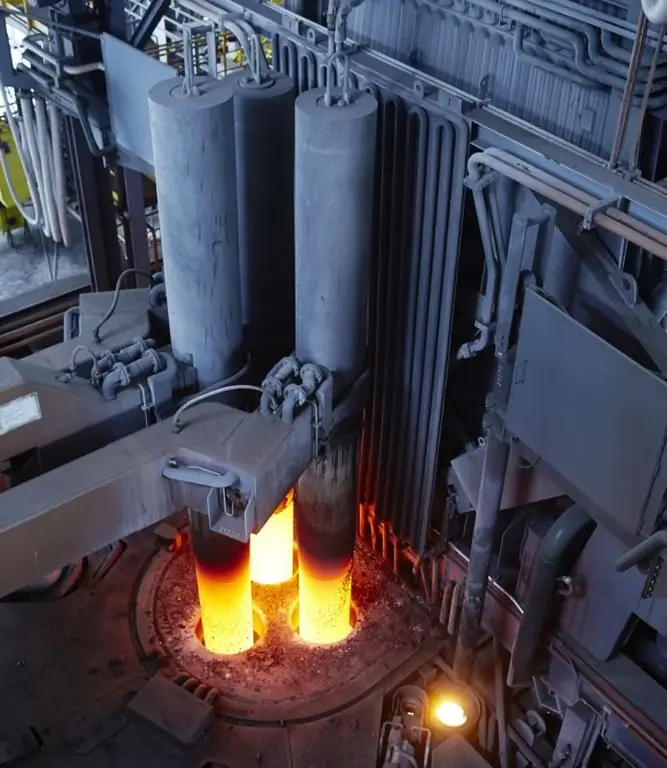
La chatarra se carga en cubos grandes, llamados cestas, con puertas de concha para la base. Se debe tener cuidado para asegurarse de que la chatarra esté en la canasta para garantizar el buen funcionamiento del horno. Se coloca una fuerte fusión encima con una capa ligera de un fragmento protector, encima de la cual se encuentra otra parte. Todos ellos deben estar presentes en el horno después de la carga. En este momento, la canasta puede pasar al precalentador de chatarra, que utiliza los gases de escape calientes de la fundición para recuperar energía y mejorar la eficiencia.
Desbordamiento
Luego se lleva el recipiente al taller de fundición, se abre el techo del horno y se carga el material en él. La transferencia es una de las operaciones más peligrosas para los operadores. Las toneladas de metal que caen liberan mucha energía potencial. Cualquier materia líquida en el horno a menudo es empujada hacia arriba y hacia afuera por chatarra sólida y grasa. El polvo en el metal se enciende si el horno está caliente, lo que hace que estalle una bola de fuego.
En algunos dispositivos de doble capa, la chatarra se carga en el segundo mientras el primero se funde y se precalienta con los gases de escape de la parte activa. Otras operaciones son: carga continua y trabajo con temperatura sobre una cinta transportadora, que luego descarga el metal en el propio horno. Otros dispositivos pueden arrancarsustancia caliente de otras operaciones.
Voltaje
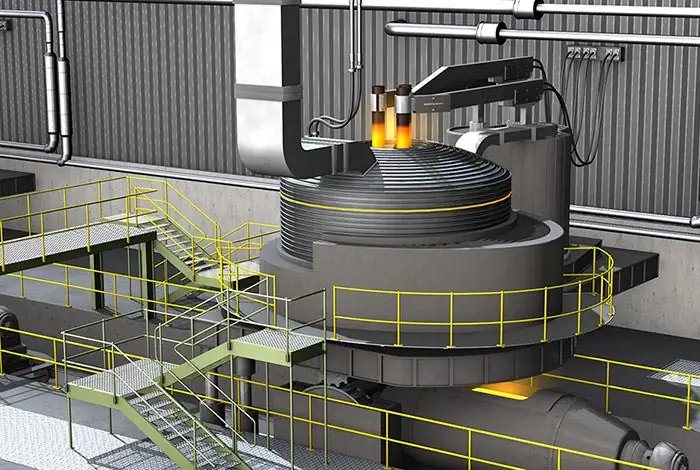
Después de la carga, el techo se inclina hacia atrás sobre el horno y comienza la fusión. Los electrodos se bajan sobre la chatarra, se crea un arco y luego se configuran para que se extiendan en la capa de migajas en la parte superior del dispositivo. Se seleccionan voltajes bajos para esta operación para proteger el techo y las paredes del calor excesivo y del daño del arco.
Una vez que los electrodos han alcanzado la masa fundida pesada en la base del horno y las ondas están protegidas por la palanca, se puede aumentar el voltaje y los electrodos se elevan ligeramente, alargando y aumentando la potencia de la masa fundida. Esto permite que el baño de fusión se forme más rápidamente, lo que reduce el tiempo de derivación.
Se inyecta oxígeno en la chatarra, se quema o se corta el acero, y los quemadores de pared proporcionan calor químico adicional. Ambos procesos aceleran la fusión de la sustancia. Las boquillas supersónicas permiten que los chorros de oxígeno penetren en la escoria espumosa y alcancen el baño líquido.
Oxidación de impurezas
Una parte importante de la fabricación de acero es la formación de escoria que flota en la superficie del acero fundido. Por lo general, se compone de óxidos metálicos y también actúa como un lugar para recolectar impurezas oxidadas, como una manta térmica (deteniendo la pérdida excesiva de calor) y también ayuda a reducir la erosión del revestimiento refractario.
Para un horno con refractarios básicos que producen acero al carbono, los formadores de escoria comunes son el óxido de calcio (CaO en forma de calcinadocal) y magnesio (MgO en forma de dolomita y magnesita.). Estas sustancias se cargan con chatarra o se soplan en el horno durante la fusión.
Otro componente importante es el óxido de hierro, que se forma cuando el acero se quema con la introducción de oxígeno. Más tarde, cuando se calienta, se inyecta carbono (en forma de carbón) en esta capa, que reacciona con el óxido de hierro para formar metal y monóxido de carbono. Esto da como resultado la formación de espuma en la escoria, lo que resulta en una mayor eficiencia térmica. El revestimiento evita daños en el techo y las paredes laterales del horno por el calor radiante.
Combustión de impurezas
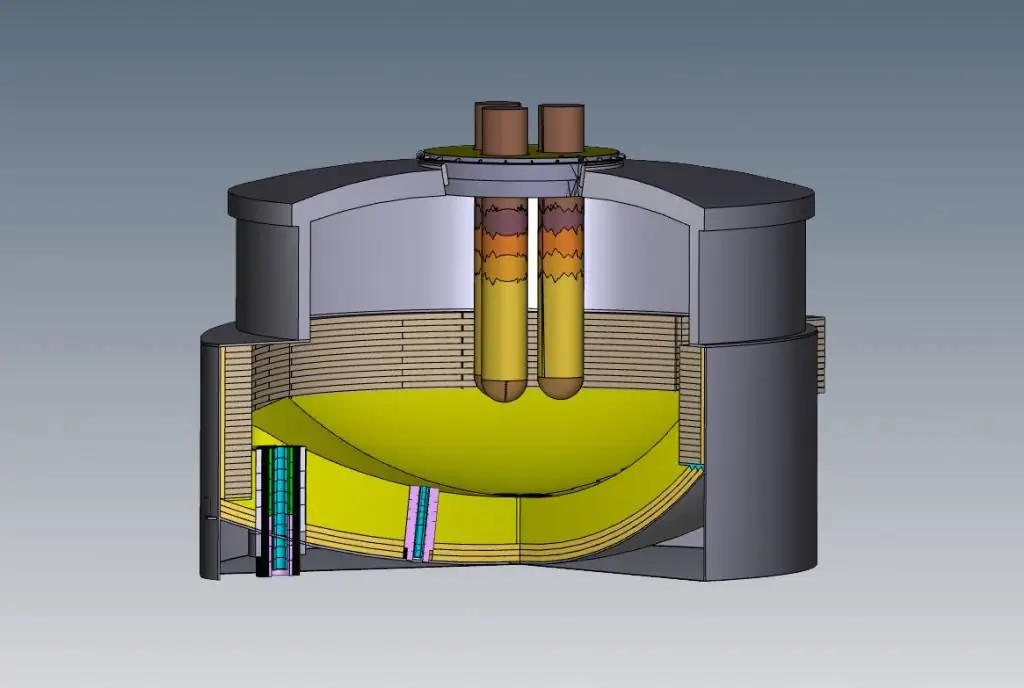
Una vez que la chatarra se haya derretido por completo y se alcance un charco plano, se puede cargar otra cubeta en el horno. Una vez que la segunda carga se funde por completo, se llevan a cabo operaciones de refinado para comprobar y corregir la composición química del acero y sobrecalentar la masa fundida por encima de su punto de congelación en preparación para la colada. Se introducen más formadores de escoria y entra mucho oxígeno en el baño, quemando impurezas como silicio, azufre, fósforo, aluminio, manganeso y calcio, y eliminando sus óxidos en escoria.
La eliminación de carbono ocurre después de que estos elementos se queman primero, ya que son más similares al oxígeno. Los metales que tienen una afinidad menor que el hierro, como el níquel y el cobre, no pueden eliminarse por oxidación y solo deben controlarse mediante química. Esta es, por ejemplo, la introducción de hierro de reducción directa y hierro fundido mencionado anteriormente.
Escoria espumosapersiste en todo el horno y, a menudo, se desborda para desbordarse desde la puerta hacia el hoyo previsto. La medición de la temperatura y la selección química se realizan mediante lanzas automáticas. El oxígeno y el carbono se pueden medir mecánicamente con sondas especiales sumergidas en acero.
Beneficios de producción
Usando un sistema de control para hornos de arco de fundición de acero, es posible producir acero a partir del 100 % de materia prima: chatarra. Esto reduce en gran medida la energía necesaria para producir la sustancia, en comparación con la producción primaria a partir de minerales.
Otro beneficio es la flexibilidad: mientras que los altos hornos no pueden variar significativamente y pueden funcionar durante años, este puede encenderse y apagarse rápidamente. Esto permite que la acería varíe la producción según la demanda.
El horno de acero de arco típico es la fuente de acero para las miniacerías, que pueden producir barras o tiras. Las minifundiciones se pueden ubicar relativamente cerca de los mercados del acero y los requisitos de transporte son menores que para una planta integrada, que generalmente se ubica cerca de la costa para el acceso de envío.
Dispositivo de horno de arco de acero
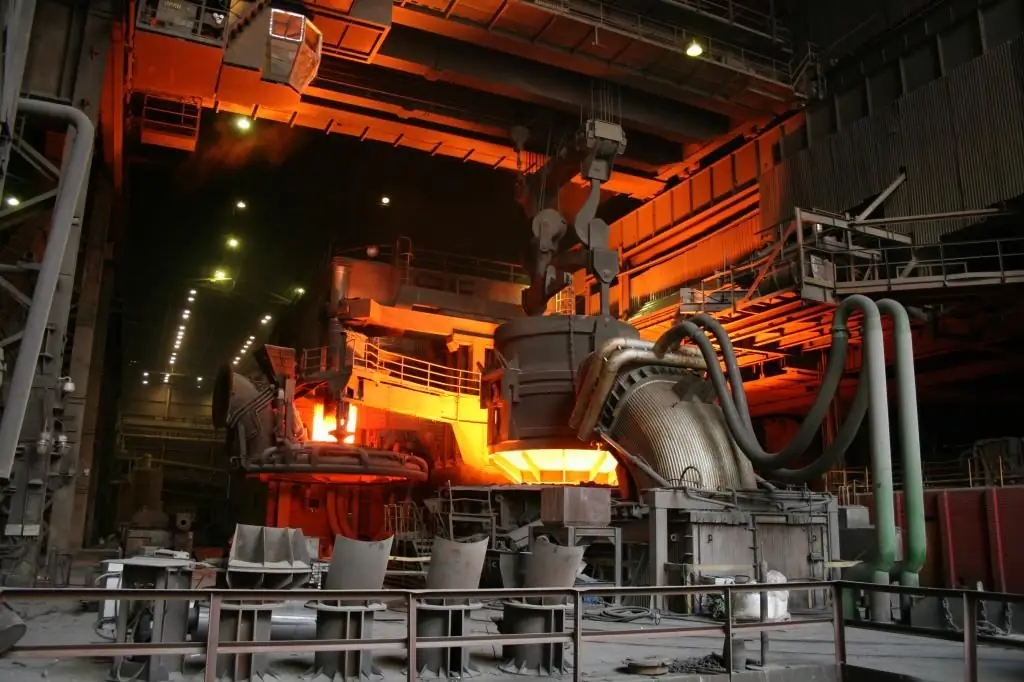
La sección transversal esquemática es un electrodo que sube y baja mediante un accionamiento de piñón y cremallera. La superficie está revestida con ladrillos refractarios y revestimiento de fondo. La puerta permite el acceso al interior.partes del dispositivo. El cuerpo del horno descansa sobre balancines para que pueda inclinarse para golpear.
Recomendado:
Acero inoxidable alimentario: GOST. ¿Cómo identificar el acero inoxidable de calidad alimentaria? ¿Cuál es la diferencia entre el acero inoxidable alimentario y el acero inoxidable

El artículo habla de grados de acero inoxidable apto para alimentos. Lea cómo distinguir el acero inoxidable alimentario del técnico
Máquina perforadora de diamantes: tipos, dispositivo, principio de funcionamiento y condiciones de funcionamiento
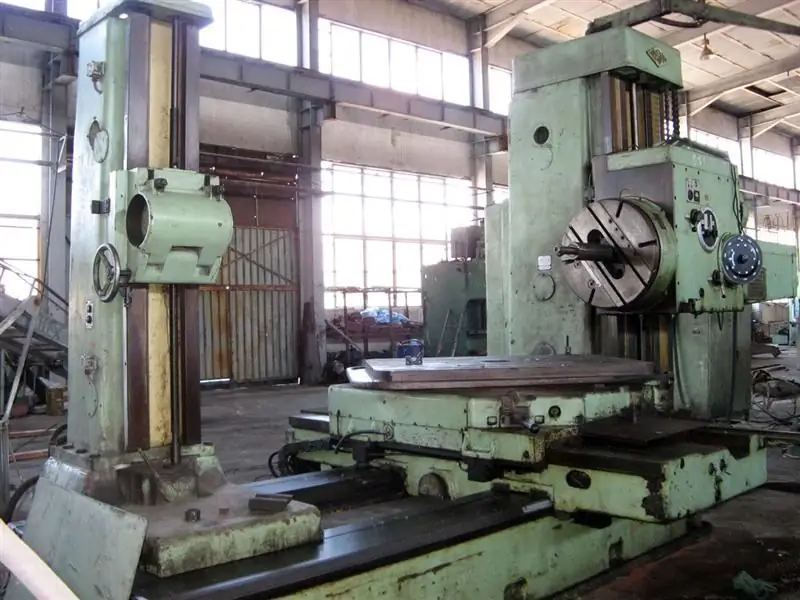
La combinación de una configuración de dirección de corte compleja y un equipo de trabajo de estado sólido permite que el equipo de perforación con diamante realice operaciones de metalurgia extremadamente delicadas y críticas. A estas unidades se les confían las operaciones de creación de superficies moldeadas, corrección de orificios, preparación de extremos, etc. Al mismo tiempo, la máquina perforadora de diamante es universal en términos de posibilidades de aplicación en varios campos. Se utiliza no solo en industrias especializadas, sino también en talleres privados
Acero resistente a la corrosión. Grados de acero: GOST. Acero inoxidable - precio
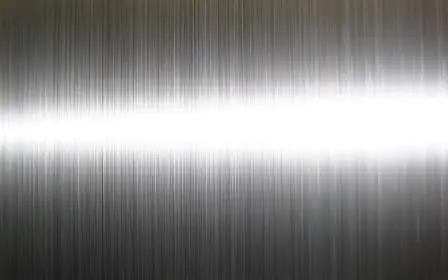
Por qué los materiales metálicos se descomponen. ¿Qué son los aceros y aleaciones resistentes a la corrosión? Composición química y clasificación según el tipo de microestructura del acero inoxidable. Factores que afectan la fijación de precios. Sistema de designación de grado de acero (requisitos GOST). Área de aplicación
¿Qué es la potencia reactiva? Compensación de potencia reactiva. Cálculo de potencia reactiva
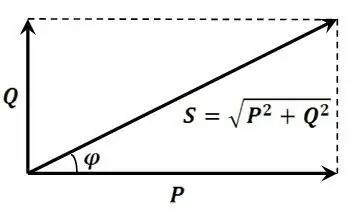
En condiciones reales de producción, prevalece la potencia reactiva de carácter inductivo. Las empresas instalan no un medidor eléctrico, sino dos, uno de los cuales está activo. Y por el gasto excesivo de energía "perseguida" en vano a través de las líneas eléctricas, las autoridades pertinentes son multadas sin piedad
Láser de fibra de iterbio: dispositivo, principio de funcionamiento, potencia, producción, aplicación
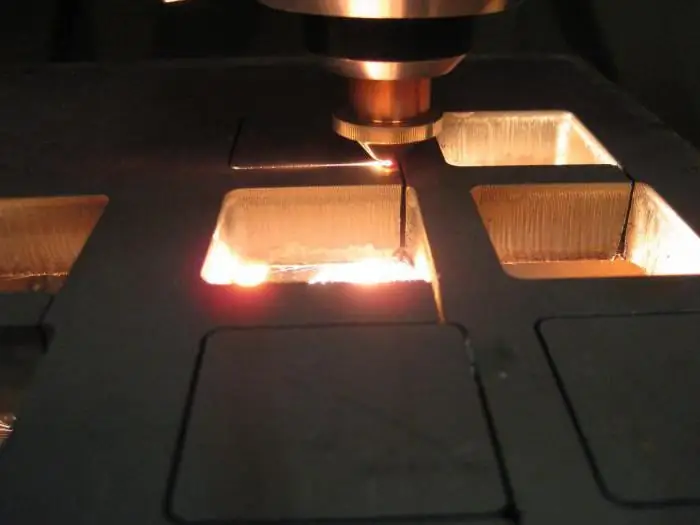
Los láseres de fibra son compactos y resistentes, apuntan con precisión y disipan la energía térmica con facilidad. Vienen en muchas formas y, al tener mucho en común con otros tipos de generadores cuánticos ópticos, tienen sus propias ventajas únicas