2025 Autor: Howard Calhoun | [email protected]. Última modificación: 2025-01-24 13:15
En la industria de la fabricación y la construcción, las pruebas no destructivas son uno de los métodos más populares para diagnosticar materiales. Usando este método, los constructores evalúan la calidad de las uniones soldadas, verifican la densidad en ciertas secciones de estructuras, revelando defectos y fallas profundas. Los detectores de defectos magnéticos de diagnóstico pueden detectar daños tanto en la superficie como en el subsuelo con un alto grado de precisión.
Dispositivo dispositivo
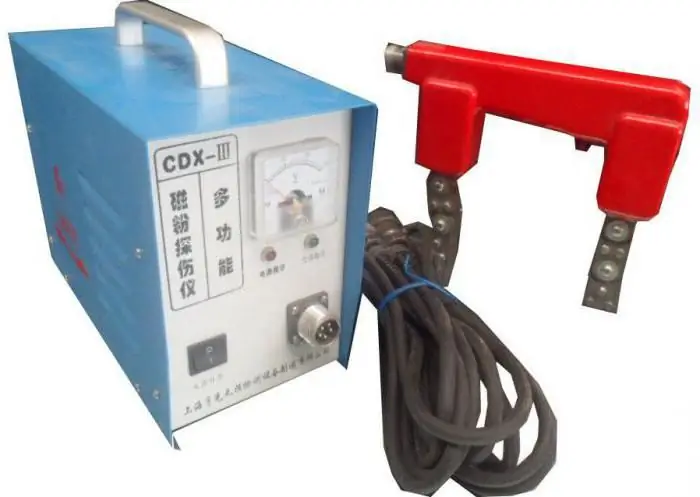
La base del segmento de medidores de espesor magnéticos y detectores de fallas son dispositivos portátiles provistos de cuerpos de trabajo magnetizables, generalmente en forma de pinzas. Exteriormente, estos son pequeños dispositivos, cuyo relleno es un electroimán que regula los polos de la acción de las olas. La clase media le permite trabajar con permeabilidad magnética, cuyo coeficiente es superior a 40. El cuerpo está provisto de un mango ergonómico, gracias al cual el dispositivo puede usarse en lugares de difícil acceso. Para suministrar corriente eléctrica, los instrumentos también están provistos de un cable conectado a una estación generadora (si el trabajo se realiza al aire libre) o a una red eléctrica doméstica de 220 V. Equipos de ensayos no destructivos más sofisticadostiene una base estacionaria conectada a una computadora. Estas herramientas de diagnóstico se utilizan con mayor frecuencia para verificar la calidad de las piezas fabricadas en producción. Realizan controles de calidad, corrigiendo las más pequeñas desviaciones de los indicadores estándar.
Detectores de fallas Ferroprobe
Una variedad de dispositivos magnéticos diseñados para detectar defectos a una profundidad de hasta 10 mm. En particular, se utilizan para corregir discontinuidades en la estructura de estructuras y piezas. Estos pueden ser puestas de sol, conchas, grietas y líneas finas. El método fluxgate también se utiliza para evaluar la calidad de las soldaduras. Después del final de la sesión de trabajo, los detectores de defectos magnéticos de este tipo también pueden determinar el nivel de desmagnetización de la pieza como parte de diagnósticos complejos. En términos de aplicación a piezas de diferentes formas y tamaños, los dispositivos prácticamente no tienen restricciones. Pero, de nuevo, uno no debe olvidarse de la profundidad máxima del análisis de estructura.
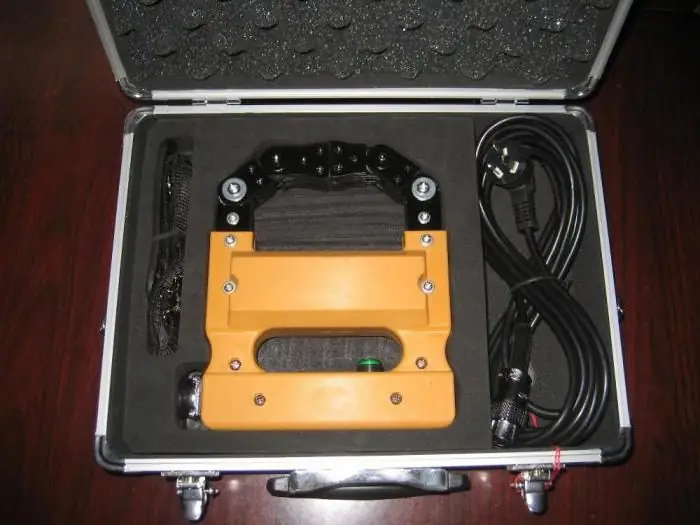
Detectores de fallas magnetográficas y de corrientes de Foucault
Con la ayuda de dispositivos magnetográficos, el operador puede detectar fallas en el producto a una profundidad de 1 a 18 mm. Y nuevamente, los signos objetivo de desviaciones en la estructura son discontinuidades y defectos en las uniones soldadas. Las características de la técnica de prueba de corrientes de Foucault incluyen el análisis de la interacción del campo electromagnético con las ondas generadas por las corrientes de Foucault que se alimentan al sujeto de control. En la mayoría de los casos, se utiliza un detector de defectos por corrientes de Foucault para examinar productos fabricados con materiales conductores de electricidad. Dispositivos de este tipomuestran un resultado muy preciso al analizar piezas con propiedades electrofísicas activas, pero es importante tener en cuenta que funcionan a poca profundidad, no más de 2 mm. En cuanto a la naturaleza de los defectos, el método de las corrientes de Foucault permite detectar discontinuidades y grietas.
Detectores de defectos por partículas magnéticas
Dichos dispositivos también se enfocan principalmente en defectos superficiales que se pueden reparar a una profundidad de hasta 1,5-2 mm. Al mismo tiempo, se permite la posibilidad de investigación para revelar una amplia gama de defectos, desde los parámetros de la soldadura hasta la detección de signos de delaminación y microfisuras. El principio de funcionamiento de este equipo de ensayo no destructivo se basa en la actividad de las partículas de polvo. Bajo la acción de una corriente eléctrica, se dirigen hacia la f alta de homogeneidad de las oscilaciones magnéticas. Esto le permite corregir las imperfecciones de la superficie del objeto de estudio de destino.
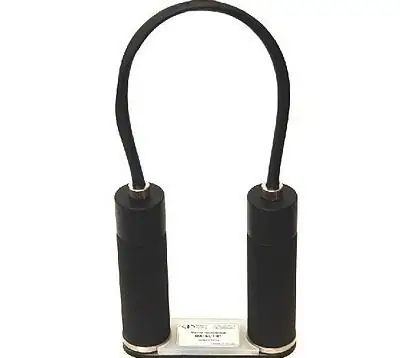
La mayor precisión en la determinación de áreas defectuosas por este método estará presente si el plano del área defectuosa forma un ángulo de 90 grados con la dirección del flujo magnético. A medida que nos desviamos de este ángulo, la sensibilidad del instrumento también disminuye. En el proceso de trabajar con dichos dispositivos, también se utilizan herramientas adicionales para corregir los parámetros de los defectos. Por ejemplo, el detector de fallas magnéticas "Magest 01" en la configuración básica está provisto de una lupa doble y una linterna ultravioleta. Es decir, la determinación directa del defecto en la superficie la realiza el operador mediante inspección visual.
Preparación para el trabajo
Las actividades preparatorias se pueden dividir en dos grupos. El primero incluirá la preparación directa de la superficie de trabajo y el segundo, la configuración del dispositivo. En cuanto a la primera parte, la parte debe limpiarse de óxido, varios tipos de grasa, manchas de aceite, suciedad y polvo. Solo se puede obtener un resultado de alta calidad sobre una superficie limpia y seca. A continuación, se configura el detector de fallas, en el que el paso clave será la calibración con verificación contra estándares. Estos últimos son muestras de materiales con defectos, que se pueden utilizar para evaluar la exactitud de los resultados del análisis del dispositivo. Además, según el modelo, puede fijar el rango de profundidad de trabajo y la sensibilidad. Estos indicadores dependen de las tareas de detección de defectos, las características del material que se examina y las capacidades del dispositivo en sí. Los modernos detectores de fallas de alta tecnología también permiten el ajuste automático de acuerdo con los parámetros especificados.
Magnetización de la pieza
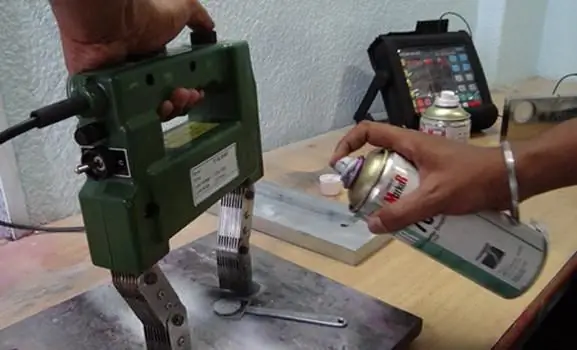
La primera etapa de las operaciones de trabajo, durante la cual se realiza la magnetización del objeto que se examina. Inicialmente, es importante determinar correctamente la dirección del flujo y el tipo de magnetización con parámetros de sensibilidad. Por ejemplo, el método de polvo le permite realizar impactos de poste, circulares y combinados en la pieza. En particular, la magnetización circular se realiza haciendo pasar una corriente eléctrica directamente a través del producto, a través del conductor principal, a través del devanado oa través de una sección separada del elemento con la conexión de contactores eléctricos. AEn el modo de acción de polos, los detectores de fallas magnéticas brindan magnetización usando bobinas, en un medio de solenoide, usando un electroimán portátil o usando imanes permanentes. En consecuencia, el método combinado le permite combinar dos métodos conectando equipos adicionales en el proceso de magnetización de la pieza de trabajo.
Aplicación de indicador magnético
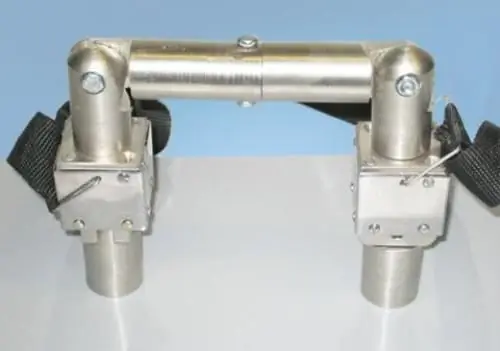
El material indicador se aplica a la superficie previamente preparada y magnetizada. Le permite identificar los defectos de la pieza bajo la influencia de un campo electromagnético. Ya se ha dicho que se pueden usar polvos en esta capacidad, pero algunos modelos también funcionan con suspensiones. En ambos casos, antes de trabajar, es importante considerar las condiciones óptimas para usar el dispositivo. Por ejemplo, se recomienda utilizar el detector de defectos magnéticos "MD-6" a temperaturas que oscilan entre -40 y 50 °C y con una humedad del aire de hasta el 98 %. Si las condiciones cumplen con los requisitos para la operación, puede comenzar a aplicar el indicador. El polvo se aplica en toda el área, de modo que también se proporciona una pequeña cobertura de áreas que no están destinadas al estudio. Esto proporcionará una imagen más precisa del defecto. La suspensión se aplica a chorro con manguera o aerosol. También existen métodos para sumergir la pieza en un recipiente con una mezcla de indicador magnético. Luego puede proceder directamente a la solución de problemas del producto.
Pieza de inspección
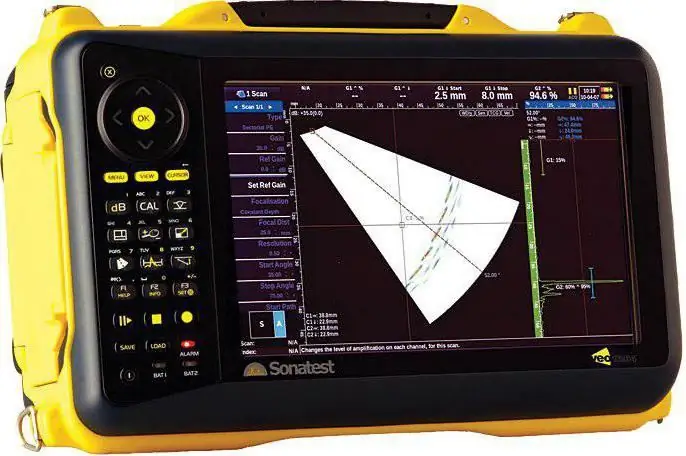
El operador debe esperar hasta que termine la actividad del indicador,ya sea partículas de polvo o suspensión. El producto se comprueba visualmente con los dispositivos antes mencionados en forma de dispositivos ópticos. En este caso, el poder de aumento de estos dispositivos no debe exceder x10. Además, según los requisitos para el examen, el operador puede tomar fotografías para un análisis informático más preciso. Las estaciones-detectores de fallas magnéticas multifuncionales cuentan en su equipamiento básico con equipos para la decodificación de réplicas con depósitos de polvo. Los dibujos obtenidos en el curso de la clasificación se comparan posteriormente con muestras estándar, lo que nos permite llegar a una conclusión sobre la calidad del producto y su admisibilidad para el uso previsto.
Conclusión
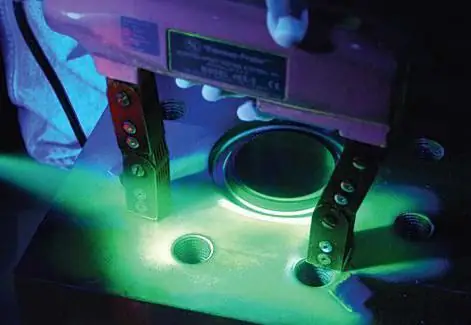
Los instrumentos de detección de fallas magnéticas son ampliamente utilizados en varios campos. Pero también tienen desventajas que limitan su uso. Dependiendo de las condiciones de operación, estos incluyen los requisitos para las condiciones de temperatura y, en algunos casos, precisión insuficiente. Como medio universal de control, los expertos recomiendan utilizar un detector de fallas magnéticas multicanal, que también es capaz de admitir la función de análisis ultrasónico. El número de canales puede llegar a 32. Esto significa que el dispositivo podrá mantener parámetros óptimos de detección de fallas para la misma cantidad de tareas diversas. En esencia, los canales se entienden como el número de modos de operación enfocados en ciertas características del material objetivo y las condiciones ambientales. Tales modelos no son baratos, pero proporcionanla exactitud de los resultados al detectar defectos superficiales y estructuras internas de varios tipos.
Recomendado:
Control de imágenes térmicas de equipos eléctricos: concepto, principio de funcionamiento, tipos y clasificación de cámaras termográficas, características de aplicación y verificac
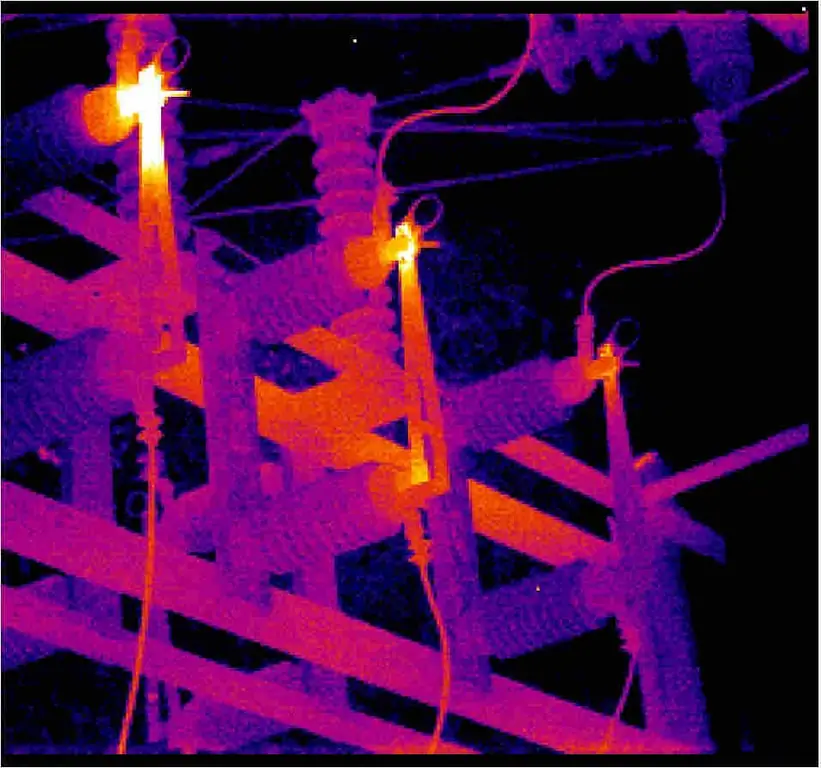
El control por imagen térmica de los equipos eléctricos es una forma eficaz de identificar defectos en los equipos de potencia que se detectan sin apagar la instalación eléctrica. En lugares de poco contacto la temperatura sube, que es la base de la metodología
Defectos del pan: fotos, causas, problemas de horneado y cómo solucionarlos
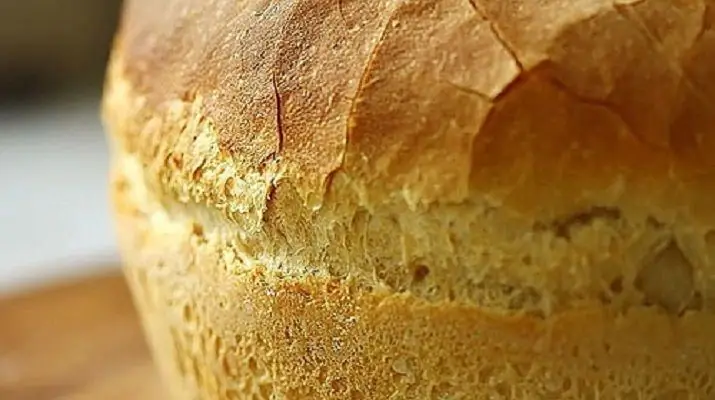
La elaboración del pan es un proceso tecnológico complejo. No en vano, los productos de panadería terminados pueden tener varios defectos. Pueden ser causados por la mala calidad de las materias primas, los errores del panadero que amasa la masa y la hornea. Vale la pena señalar que las fallas asociadas con la calidad de los ingredientes son extremadamente difíciles de corregir, mientras que las fallas tecnológicas se pueden corregir. El artículo habla sobre los defectos del pan y cómo eliminarlos
Defectos de los rieles y su clasificación. Estructura de designación de defectos ferroviarios
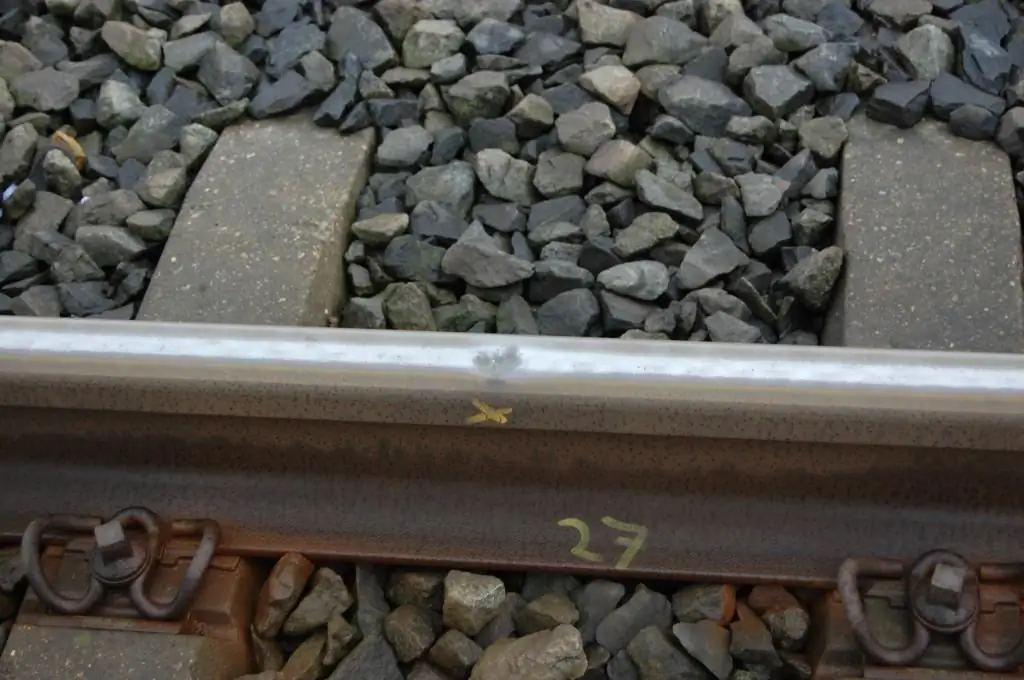
Actualmente, la gente está utilizando activamente el ferrocarril. La entrega de varios tipos de carga por esta ruta es el principal tipo de transporte. Sin embargo, debido al gran peso de los propios trenes, así como a la carga que transportan, existe una fuerte presión sobre los raíles. Los defectos en estos objetos son una ocurrencia bastante común, que debe eliminarse de inmediato
Defectos de la madera: tipos, descripción y remedios
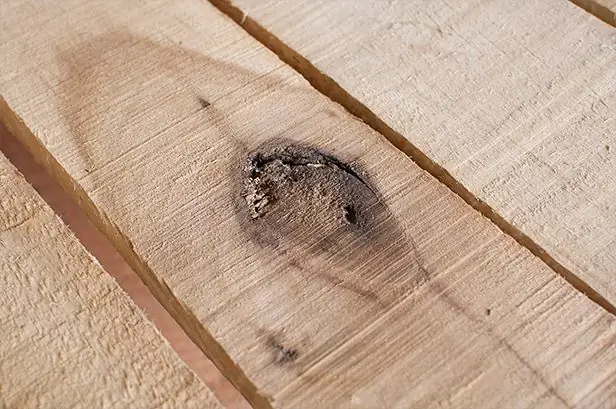
Hoy en día, hay muchos materiales de construcción. Uno de los más antiguos, pero al mismo tiempo, la madera se ha generalizado. Sin embargo, como es sabido, este material está "vivo" y, por lo tanto, no está exento de defectos naturales. La madera es muy susceptible a diversas influencias
Detección de defectos de color en soldaduras: características y descripción
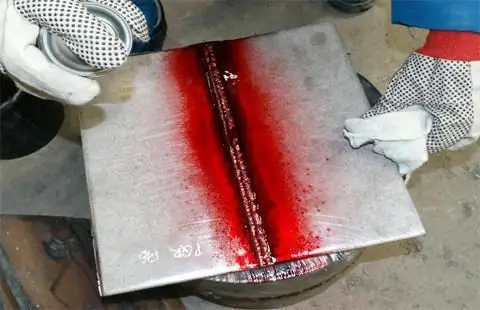
El artículo está dedicado a la detección de defectos de color en soldaduras. Se consideran las características del procedimiento, su descripción, etapas tecnológicas, etc