2025 Autor: Howard Calhoun | [email protected]. Última modificación: 2025-01-24 13:15
El taladrado es uno de los tipos de mecanizado de materiales por corte. Este método utiliza una herramienta de corte especial: un taladro. Con él, puedes hacer un agujero de diferentes diámetros, así como profundidades. Además, es posible crear agujeros poliédricos con diferentes secciones.
Asignación de operación
La perforación es una operación necesaria si se desea perforar un producto metálico. La mayoría de las veces, hay varias razones para perforar:
- requerido para crear un agujero para roscar, avellanar, escariar o taladrar;
- necesario colocar cables eléctricos, tornillería en los agujeros, pasar pernos de anclaje, etc.;
- separación en blanco;
- debilitar estructuras colapsadas;
- dependiendo del diámetro del agujero, incluso se puede usar para plantar explosivos, como cuando se extrae piedra natural.
Esta lista puede continuar por mucho tiempo, pero ya podemos concluir que la operación de perforación esuna de las cosas más sencillas y a la vez bastante necesarias y comunes.
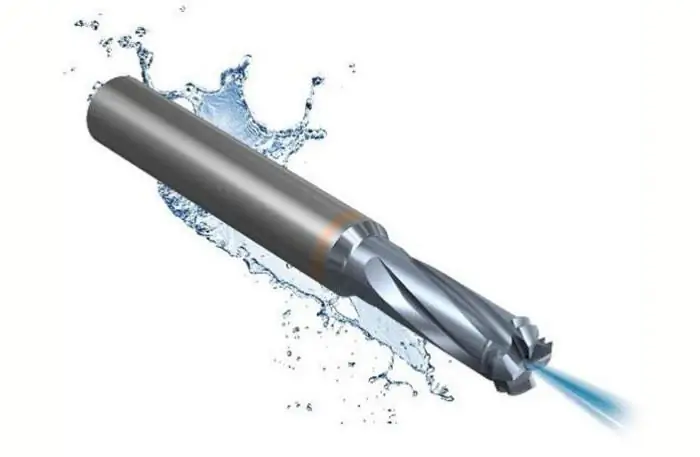
Consumibles
Naturalmente, para llevar a cabo el proceso de perforación, es necesario contar con taladros. Dependiendo de este consumible, cambiará el diámetro del agujero, así como el número de sus caras. Pueden ser redondos o multifacéticos: triangulares, cuadrados, pentagonales, hexagonales, etc.
Además, la perforación es una operación en la que el taladro se calentará a altas temperaturas. Por ello, es necesario seleccionar con precisión la calidad de este elemento, en función de las exigencias del material a trabajar.
- Un material bastante común para la producción de accesorios de perforación es el acero al carbono. Los elementos de este grupo están marcados de la siguiente manera: U8, U9, U10, etc. El objetivo principal de estos consumibles es perforar agujeros en madera, plástico, metales blandos.
- Los siguientes son taladros hechos de acero de baja aleación. Están destinados a taladrar los mismos materiales que los de carbono, pero su diferencia radica en que esta marca de elementos tiene un mayor valor de resistencia al calor de hasta 250 grados centígrados, así como una mayor velocidad de taladrado.
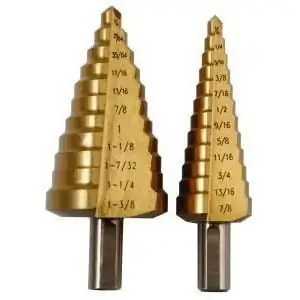
Ejercicios mejorados
Hay varios tipos de brocas diseñadas para materiales de mayor calidad:
- El primer tipo de taladro está hecho de acero de alta velocidad. La resistencia al calor de estos consumibles es mucho mayor- 650 grados centígrados, y están diseñados para taladrar cualquier material estructural en estado no endurecido.
- El siguiente grupo son las brocas de carburo. Se utilizan para hacer agujeros en cualquier acero estructural no templado, así como en metales no ferrosos. Una característica es que se utiliza la perforación a altas velocidades. Por la misma razón, la resistencia al calor se ha aumentado a 950 grados centígrados.
- Uno de los elementos más duraderos son los taladros Borazon. Se utiliza para trabajar con hierro fundido, acero, vidrio, cerámica, metales no ferrosos.
- El último grupo son las perforadoras de diamante. Se utiliza para taladrar los materiales más duros, vidrio, cerámica.
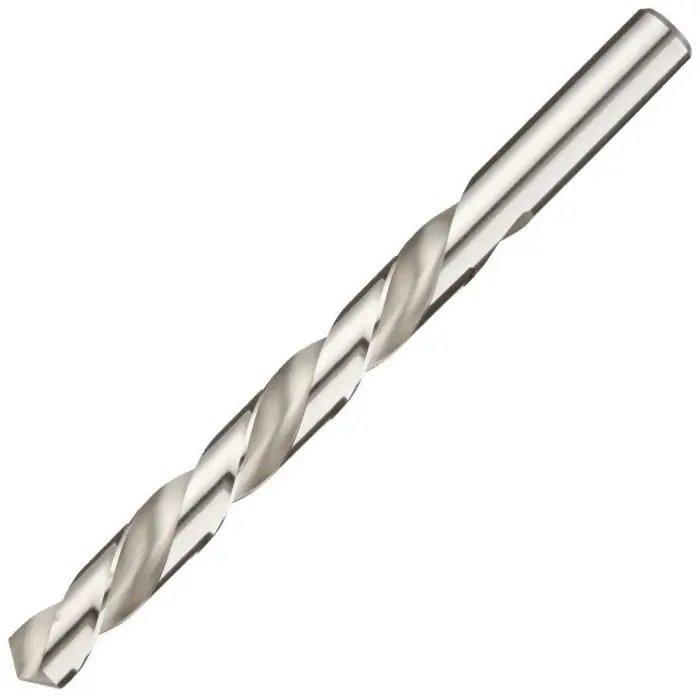
Tipos de perforadoras
Para realizar la operación de taladrado se pueden utilizar los siguientes tipos de taladradoras:
- Dispositivos de perforación vertical y horizontal. Perforar agujeros para tales máquinas es la operación principal.
- Se utilizan máquinas de mandrinado vertical y horizontal. La perforación se considera una operación auxiliar para estos dispositivos.
- Fresadoras verticales, horizontales y universales. Para estas unidades, la perforación también es una operación secundaria.
- Tornos y tornos. En el primer tipo de dispositivos, el taladro es una parte fija y la pieza de trabajo gira. Para el segundo tipo de dispositivo, la perforación no es la operación principal, y el taladro es un elemento fijo, como en el primerocaso.
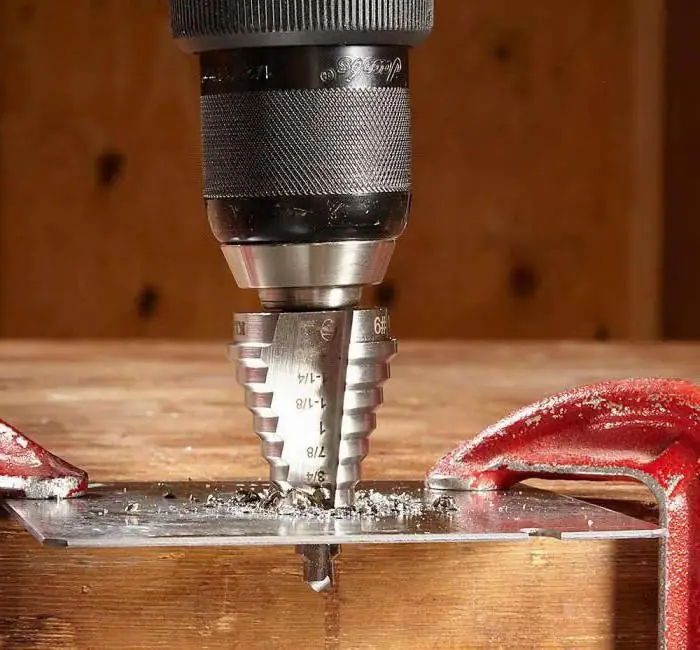
Estos son todo tipo de máquinas perforadoras que pueden realizar todas las operaciones requeridas.
Herramientas manuales y operaciones auxiliares
Para facilitar el proceso de perforación, se utilizan varias operaciones auxiliares. Estos incluyen lo siguiente:
- Refrigeración. Al perforar, se utiliza una variedad de fluidos de corte. Estos incluyen, por ejemplo, agua, emulsiones, ácido oleico. También se pueden utilizar sustancias gaseosas como el dióxido de carbono.
- Ultrasonido. Las vibraciones ultrasónicas producidas por el taladro se utilizan para aumentar la productividad del proceso, así como para mejorar la rotura de virutas.
- Calentado. Para mejorar la perforación de metal de alta densidad, se precalienta.
- Huelga. Algunas superficies, como el hormigón, requieren el uso de movimientos de impacto giratorio para aumentar la productividad.
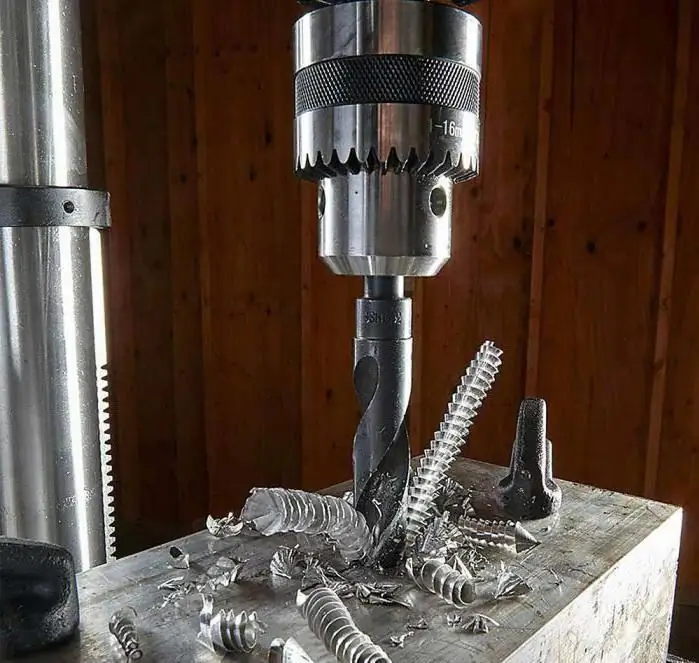
Este procedimiento se puede realizar no solo en máquinas en modo automático, sino también en equipos manuales. La perforación manual implica el uso de herramientas como:
- Taladro mecánico. La perforación utiliza energía mecánica humana.
- Taladro eléctrico. Puede realizar perforaciones convencionales y rotativas de impacto. Alimentado por electricidad.
Tipos de tratamiento y enfriamiento
Hay varios tipos básicos de perforación - estos sonrealizar agujeros cilíndricos, poliédricos u ovalados, así como perforar agujeros cilíndricos existentes para aumentar su diámetro.
El principal problema que se presenta en el proceso de taladrado de metal es el fuerte calentamiento del elemento consumible, es decir, el taladro, así como el lugar de trabajo. La temperatura del material puede alcanzar los 100 grados centígrados o más. Si alcanza ciertos valores, entonces puede ocurrir combustión o fusión. Es importante tener en cuenta aquí que muchos de los aceros que se utilizan para fabricar taladros pierden su dureza cuando se calientan, lo que solo aumentará la fricción, por lo que, lamentablemente, el elemento se desgastará más rápido.
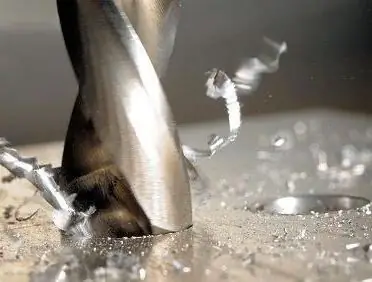
Para combatir esta deficiencia, se utilizan varios refrigerantes. La mayoría de las veces, con la perforación vertical en la máquina, es posible organizar el suministro de refrigerante directamente al lugar de trabajo. Si se lleva a cabo con herramientas manuales, luego de un cierto período de tiempo es necesario interrumpir el proceso y sumergir el taladro en el líquido.
La esencia de perforar
La tecnología de perforación de agujeros es el proceso de formación de ranuras mediante la eliminación de virutas en un material sólido con una herramienta de corte. Este elemento realiza movimientos de rotación y traslación o rotación-traslación al mismo tiempo, lo que forma un agujero.
El uso de este tipo de procesamiento de materiales sirve para:
- obtener agujeros no críticos con un bajo grado de precisión y grado de rugosidad utilizados para montar pernos, remaches, etc.;
- hacer agujeros para roscar, escariar, etc.
Opciones de procesamiento
Mediante el procedimiento de taladrado profundo o escariado, se pueden obtener orificios que se caracterizarán por el grado 10 u 11 de rugosidad superficial. Si es necesario obtener un mejor orificio, luego de completar el proceso de procesamiento, es necesario avellanarlo y escariarlo adicionalmente.
Para aumentar la precisión del trabajo, en algunos casos, puede recurrir a un ajuste cuidadoso de la posición de la máquina, consumibles debidamente afilados. También se utiliza un método en el que el trabajo se realiza a través de un dispositivo especial que aumenta la precisión. Este dispositivo se llama conductor. También hay una división de ejercicios en varias clases. Hay brocas helicoidales de flauta recta, brocas de pala que se usan para perforaciones profundas o sacanúcleos y brocas de centro.
Descripción del diseño del taladro
La mayoría de las veces, se utiliza un taladro helicoidal convencional para trabajar. Los especiales se usan con mucha menos frecuencia.
El elemento espiral es una pieza de corte de dos dientes, que incluye solo dos partes principales: un vástago y una pieza de trabajo.
Si hablamos de la parte de trabajo, entonces se puede dividir en cilíndrica y de calibración. En la primera parte del taladro, hay dos ranuras helicoidales opuestas. Principalel propósito de esta parte es eliminar las virutas que se liberan durante la operación. Es importante señalar aquí que las estrías tengan el perfil correcto, lo que garantiza la correcta formación de los filos de la broca. Además, se crea el espacio necesario, que es necesario para la eliminación de virutas del agujero.
Tecnología de perforación
Aquí es importante conocer algunas reglas específicas. Es muy importante que la forma de las acanaladuras, así como el ángulo de inclinación entre la dirección del eje de la broca y la tangente a la correa, sea tal que asegure una fácil evacuación de la viruta sin debilitar la sección de los dientes. Sin embargo, vale la pena señalar aquí que esta tecnología, y especialmente los valores numéricos, cambiarán notablemente según el diámetro de la broca. El caso es que un aumento en el ángulo de inclinación conduce a un debilitamiento de la acción del taladro. Esta desventaja es más pronunciada cuanto menor es el diámetro del elemento. Por esta razón, debe ajustar el ángulo del taladro. Cuanto menor sea el taladro, menor será el ángulo, y viceversa. El ángulo total de las ranuras es de 18 a 45 grados. Cuando se trata de taladrar acero, es necesario utilizar taladros con un ángulo de inclinación de 18 a 30 grados. Si los agujeros se hacen en materiales quebradizos como el latón o el bronce, el ángulo se reduce a 22-25 grados.
Principios de trabajo
Aquí es importante comenzar con el hecho de que dependiendo del material de la herramienta, la velocidad de corte también cambiará. Por ejemplo:
- Si la perforación se realiza con elementos de acero para herramientas, la velocidad mínima es de 25 m/min y la velocidad máxima de 35m/min.
- Si el mecanizado se realiza con brocas HSS, la velocidad mínima es de 12 m/min y la máxima de 18 m/min.
- Si se utilizan brocas de carburo, los valores son 50 m/min y 70 m/min.
Es importante señalar aquí que la tecnología de taladrado implica la elección de la velocidad del procedimiento en función del diámetro del propio elemento y del bajo avance (al aumentar el diámetro, la velocidad también aumenta).
Un rasgo característico de la obra es el uso de un ángulo estándar en la parte superior para el taladro, que es de 118 grados. Si es necesario trabajar con materias primas que se caracterizan por una alta dureza de aleación, entonces el ángulo debe aumentarse a 135 grados.
Seguridad de los taladros
Una de las tareas importantes en este tipo de mecanizado era preservar las propiedades de corte del consumible. La seguridad de estos parámetros depende directamente de qué método de operación se eligió y si era adecuado para este material. Por ejemplo, para eliminar la rotura de una broca en una pasada, es necesario reducir mucho el avance en el momento de retirar la broca del agujero.
Se debe prestar especial atención a la tecnología de perforación en situaciones en las que la profundidad del orificio supere la longitud de la ranura helicoidal del consumible. En el momento de la inserción del taladro, todavía se formarán virutas, pero durante la salida ya no lo estarán. Debido a esto, los taladros se rompen con mucha frecuencia. Si no hay forma de salir de la situación, debe quitar periódicamente el taladro y limpiarlo manualmente de elementos innecesarios, es decirvirutas.
Brocas de perforación
Para hacer un agujero en un determinado revestimiento, es necesario utilizar coronas. Sin embargo, también deben elegirse correctamente, en función de ciertos parámetros. Actualmente, se utilizan tres tipos principales de material para crear coronas: diamante, carburo y carburo de tungsteno. Una característica de la corona de diamante es que realiza una perforación sin golpes. En este caso, se obtiene una geometría de agujero más correcta.
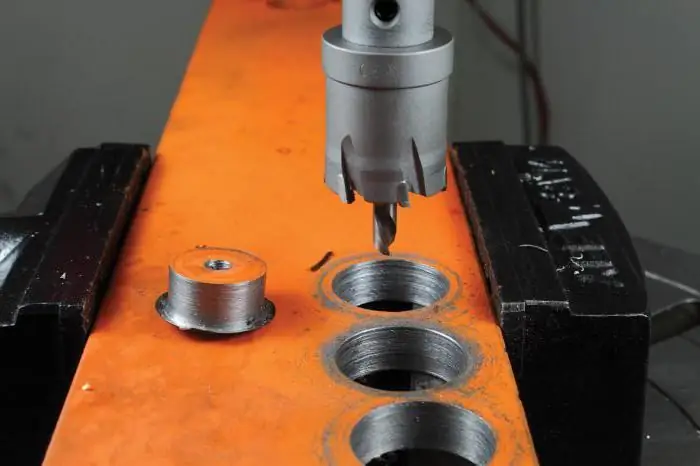
Las principales ventajas de las boquillas de diamante fueron las siguientes: la capacidad de cortar materiales de hormigón armado, bajos niveles de ruido y polvo, sin daños en la estructura de la estructura, ya que la tecnología no utiliza fuerza de impacto.
Recomendado:
Perforación exploratoria: características, equipamiento. Asistente de perforación para perforación de producción y exploración
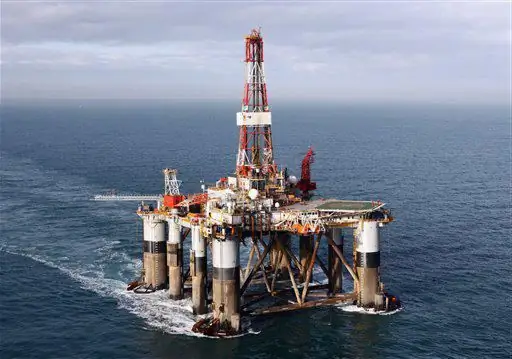
La perforación exploratoria es una actividad destinada a encontrar materias primas en las entrañas de la tierra. A principios del siglo XIX en Francia, buscaban agua de esta manera. En los años 50 del mismo siglo se buscaba petróleo con la ayuda de perforaciones exploratorias
Carne: procesamiento. Equipos para el procesamiento de carnes y aves. Producción, almacenamiento y procesamiento de carne
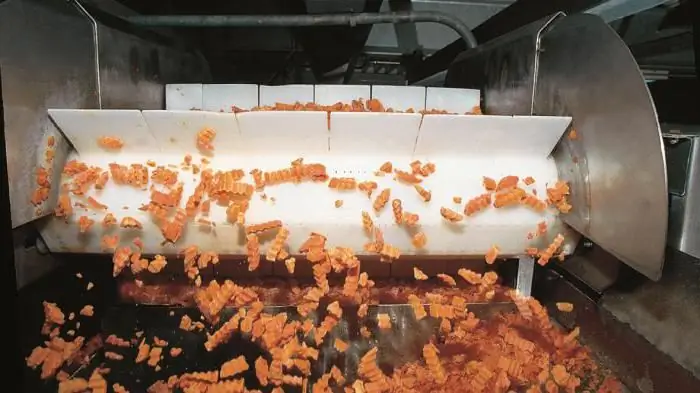
La información de las estadísticas estatales muestra que el volumen de carne, leche y aves consumidas por la población ha disminuido significativamente en los últimos años. Esto se debe no solo a la política de precios de los fabricantes, sino también a la escasez banal de estos productos, cuyos volúmenes requeridos simplemente no tienen tiempo de producir. ¡Pero la carne, cuyo procesamiento es un negocio extremadamente rentable, es muy importante para la salud humana
Mecánico de trabajos de montaje mecánico: características de la profesión
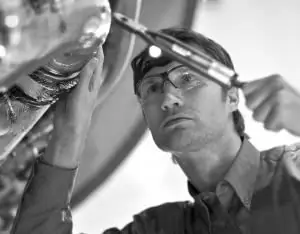
El trabajo de montaje mecánico es un especialista que se dedica no solo al montaje de mecanismos, sino también a la producción de piezas para ellos
HDD - tecnología de perforación. Perforación direccional horizontal
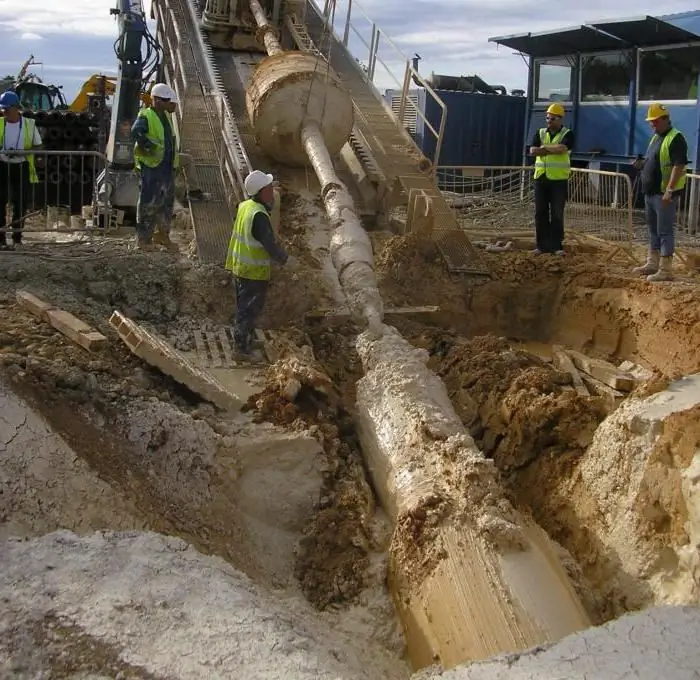
El artículo está dedicado a la tecnología de perforación direccional horizontal. Se consideran las características del método, los matices de su implementación, etc
La mecánica automotriz es una profesión para automovilistas. La profesión de mecánico de automóviles (mecánico de automóviles): formación, cualidades necesarias
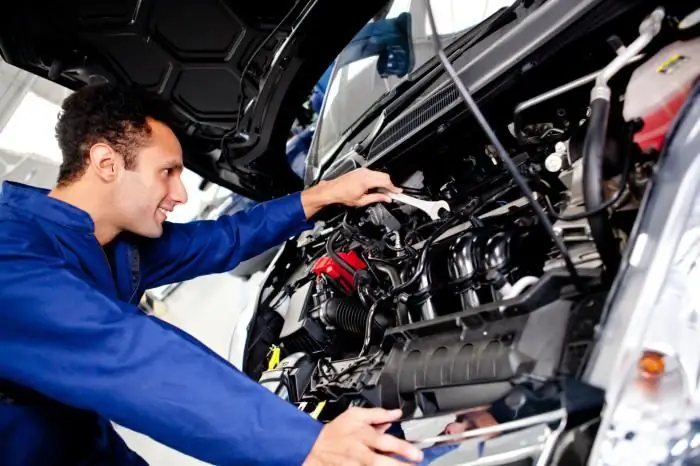
No sorprenderá a nadie con la presencia de un automóvil ahora, especialmente porque en algunas familias puede haber incluso varios de ellos. Pero, como cualquier mecanismo, la máquina necesita un cuidado constante y, a veces, reparación. No todos pueden resolver un problema de este tipo por sí mismos, por lo tanto, en la sociedad moderna, ha aparecido una especialidad como la mecánica automotriz. Esta profesión es difícil, lo que significa que las personas que la dominan valen su peso en oro